
강도, 회전 내구성 및 비틀림 내구성을 고려한 인텀 샤프트 어셈블리의 설계
Copyright Ⓒ 2023 KSAE / 212-02
This is an Open-Access article distributed under the terms of the Creative Commons Attribution Non-Commercial License(http://creativecommons.org/licenses/by-nc/3.0) which permits unrestricted non-commercial use, distribution, and reproduction in any medium provided the original work is properly cited.
Abstract
The intermediate shaft assembly must be designed to satisfy the requirements for yield strength, ultimate strength, rotational durability and torsional durability. In the past, it was considered acceptable when the maximum stress did not exceed the yield strength under a torque of 200 Nm. Recently the standard has been strengthened to satisfy the yield strength requirement under a torque of 280 Nm. Under a torque of 280 Nm, the original design did not satisfy the yield strength requirement at the yoke of the shaft. The thickness of the yoke was increased from 7.7 mm to 9.1 mm to satisfy the yield strength requirement. Then efforts were made to reduce the thicknesses of shaft and tube where the maximum stress was relatively low in the original design. By reducing their thickness, the weight of intermediate shaft assembly was reduced by 8.14 % while all the four requirements were satisfied with the modified design.
Keywords:
Intermediate shaft assembly, Steering, Yield strength, Ultimate strength, Rotational durability, Torsional durability키워드:
인텀 샤프트 어셈블리, 조향, 항복강도, 극한강도, 회전 내구성, 비틀림 내구성1. 서 론
인텀 샤프트 어셈블리는 조향 컬럼의 토크를 기어박스에 전달하는 장치이다.1-3) 인텀 샤프트는 스티어링 핸들의 조향력을 전달하는 주된 기능 외에 차량 주행 시 차체의 전달음, 노면의 진동, 소음 등을 흡수하는 기능, 차량 충돌 시 차체에서 밀려오는 변위를 흡수하여 운전자의 하체 상해를 방지할 수 있는 충격 흡수 기능 등을 수행하는 중요 부품이다.4,5)
인텀 샤프트 어셈블리의 형상 설계와 해석 등에 대한 많은 연구가 진행되어 왔다. Koparde 등6)은 설계 변경을 통하여, 요크 부위에서의 응력을 감소시키면서 경량화를 시키는 연구를 수행하였다. Kim 등7)은 유한요소해석을 통하여 인텀 샤프트 어셈블리의 강성, 강도 및 내구성을 예측하였다. Gandhi 등8)은 강재로 만들어진 요크의 강도와 강성을 향상시키는 연구를 수행하였다.
자동차의 경량화에 대한 요구에 따라서, 조향 장치에서 사용되는 인텀 샤프트 어셈블리의 소재가 기존의 강재에서 알루미늄으로 변경되었다. 내연기관 자동차에서는 고온에서의 물성이 중요하므로, 6xxx 계열의 알루미늄 합금이 인텀 샤프트 어셈블리의 소재로 많이 사용되어 왔다. 강신재 등9)은 6xxx 계열의 알루미늄을 소재로 사용하여 내열성 및 강성에 대한 요구 조건을 충족하였다. Gupta 등10)은 6xxx 계열의 알루미늄 합금을 사용하여 조향장치를 설계하였다. Miyake 등11)은 미끄럼 방식의 인텀 샤프트 어셈블리의 미끄럼 특성을 향상시키기 위해서 폴리아미드 코팅을 사용하였다.
자동차의 동력원이 내연기관으로부터 전기로 전환되는 최근의 추세에서는, 고온 재료 물성의 중요성이 점점 감소하고 있다. 이에 따라서 상온에서 더 높은 물성을 갖는 섬유강화복합재료나 7xxx 계열의 알루미늄 합금이 인텀 샤프트 어셈블리의 재료로 고려되고 있다. Cho 등12)은 선박의 인텀 샤프트에 고강도 경량 탄소섬유강화복합재료를 사용하는 연구를 수행하였다. 방우석과 이광주13)는 7xxx 계열의 알루미늄 합금으로 제작된 인텀 샤프트의 설계를 변경하여 자중을 감소시키는 연구를 수행하였다.
인텀 샤프트 어셈블리의 주요 구성품은 샤프트와 튜브이다(Fig. 1). 샤프트와 튜브의 끝단에는 하중을 전달하기 위하여 요크를 연결하게 된다. 기존에는 요크를 별도로 제작하여 샤프트와 튜브에 연결하였지만, 최근에는 요크 일체형으로 샤프트와 튜브를 제작하는 경우가 많다(Fig. 1). 요크에는 핀을 연결하여 토크 하중을 전달하게 된다.
인텀 샤프트 어셈블리는 다음과 같은 네 가지 요구 조건을 충족하도록 설계되어야 한다:14) (1) 280 Nm의 토크가 가해질 때 발생하는 응력이 항복강도를 초과하지 않아야 한다(200 Nm의 토크가 가해질 때 발생하는 응력이 항복강도를 초과하지 않아야 한다는 기존의 요구 조건이 상향되었음). (2) 400 Nm의 토크가 가해질 때 발생하는 응력이 극한강도를 초과하지 않아야 한다. (3) 100만 사이클 이상의 회전 내구 수명을 가져야 한다. (4) 100만 사이클 이상의 비틀림 내구 수명을 가져야 한다.
본 논문에서는 7xxx 계열의 알루미늄 합금을 사용하여, 위와 같은 요구 조건을 모두 충족하는 인텀 샤프트 어셈블리를 설계하고자 한다.
2. 인텀 샤프트 어셈블리 소재의 물성 평가
본 연구에서 사용된 인텀 샤프트 어셈블리의 소재는 7xxx 계열의 알루미늄 소재이다. 해석에 사용할 소재의 기계적 물성을 확보하기 위하여 인장 시험을 수행하였다. 인장 시험을 위하여, ASTM E8M에서 제시된 크기와 형상으로 Fig. 2와 같이 시편을 제작하였다.15)
시험 장비로 MTS 810 Material Test System을 사용하여 상온에서 인장 시험을 수행하였다(Fig. 3). 인장 시험에서는 변형률의 크기에 따라서 시험 속도를 다르게 적용하였다. 즉 변형률이 0 ~ 1 % 구간과 1 % 이상인 구간에서, 시험 속도를 각각 0.5 mm/min과 5 mm/min로 설정하여 인장 시험을 수행하였다. 총 7개의 시편을 사용하여 시편이 완전히 파단될 때까지 인장 시험을 수행하였다.
인장 시험의 결과로 응력-변형률 선도를 확보하였다(Fig. 4). 또한 탄성계수, 항복강도 및 극한강도를 구할 수 있었다. 시험에 사용된 소재의 평균 탄성계수는 70.23 GPa, 평균 항복응력은 382.23 MPa 및 평균 극한응력은 421.99 MPa임을 확인하였다(Table 1).
3. 항복강도 및 극한강도 요구 조건
조향장치의 설정에 따라서 샤프트가 튜브에 삽입된 깊이가 달라지게 된다(Fig. 5). 항복강도 및 극한강도 요구 조건을 확인하기 위한 해석에서는, 샤프트와 튜브가 서로 조립된 상태가 아닌 각각의 단품에 대한 해석을 수행한다. 단품에 대한 강도 평가에서는, 샤프트가 튜브에 최대한 깊게 삽입된 상태를 경계조건으로 설정한다.14) 따라서 본 연구에서 항복강도 및 극한강도 요구 조건의 충족 여부를 확인하기 위해서는, 샤프트가 튜브에 최대로 삽입된 Fig. 5(a)와 같은 경계조건에서 샤프트와 튜브의 단품에 대한 해석을 각각 수행하였다.
인텀 샤프트 어셈블리의 구조 해석을 위해서 상용 소프트웨어인 LS-Dyna를 사용하였다. 하중으로 작용하는 토크의 크기에 따라서 인텀 샤프트 어셈블리에 발생하는 응력이 항복강도를 초과하는 경우가 있기 때문에, 인장 시험을 통하여 확보한 응력-변형률 선도(Fig. 4)를 이용하여 재료 물성의 비선형을 고려한 해석을 수행하였다.
3.1 샤프트
샤프트 끝단에 위치한 요크 부위의 구멍에 삽입한 핀의 표면 노드에 z-축을 중심으로 크기가 280 Nm와 400 Nm의 토크를 하중으로 부여하였다(Fig. 6). 토크의 크기가 280 Nm와 400 Nm일 때, 샤프트에 발생하는 최대응력의 크기가 각각 항복강도와 극한강도를 초과하지 않는지 해석을 통하여 확인하였다. 튜브 내부 표면과 맞닿는 샤프트 내부 표면의 모든 노드를 고정하는 경계조건을 사용하였다(Fig. 6).
샤프트에 대한 해석에서, 샤프트 끝단에 부착된 요크 부위에서 발생하는 응력을 우선 살펴보았다. 토크가 200 Nm일 때 요크 부위에서의 최대응력의 크기는 379.55 MPa로 항복강도 382.23 MPa보다 더 작은 값을 갖는다. 그러나 토크가 280 Nm일 때에는 요크 부위에서의 최대응력이 389.90 MPa로 항복강도 382.23 MPa을 초과하였다. 이는 제시된 요구 조건을 충족하지 못한 결과이다. 따라서 Fig. 7에서와 같이, 요크 부위의 두께를 초기 설계 값인 7.7 mm에서 8.4 mm와 9.1 mm로 증가시킨 다음에 요크 부위에 대한 해석을 수행하였다.
비틀림 토크가 각각 280 Nm과 400 Nm일 때 샤프트의 요크 부위에서의 응력분포를 구하여 아래 그림에서 정리하였다(Fig. 8, Fig. 9).
이상의 결과를 이용하여, 각각의 경우에 최대응력의 크기를 아래 표에서 정리하였다.
인텀 샤프트 어셈블리의 설계에서, 토크가 280 Nm일 때 샤프트의 요크 부위에서 발생하는 최대응력이 항복강도 382.23 MPa를 초과하지 않아야 한다. 요크 부위의 두께가 7.7 mm와 8.4 mm일 때의 최대응력은 각각 389.90 MPa과 387.60 MPa로 모두 항복강도를 초과한 응력이 발생하였다(Fig. 8, Table 2). 요크 부위의 두께가 9.1 mm일 때에는 최대응력이 374.21 MPa로 항복강도를 초과하지 않았다(Fig. 8, Table 2). 따라서 토크가 280 Nm일 때 항복강도에 대한 조건을 충족하기 위해서는 샤프트 요크 부위의 두께가 9.1 mm가 되어야 하는 것을 알 수 있다.
인텀 샤프트 어셈블리의 설계에서, 토크가 400 Nm일 때 샤프트의 요크 부위에서 발생하는 최대응력이 극한강도 421.99 MPa을 초과하지 않아야 한다. 두께가 7.7 mm, 8.4 mm, 및 9.1 mm인 모든 경우에서 최대응력이 각각 405.85 MPa, 395.40 MPa 및 388.95 MPa로 나타났으며, 이들 값은 모두 극한강도를 초과하지 않았다(Fig. 9, Table 2). 따라서 토크가 400 Nm일 때, 모든 두께의 요크 부위가 극한강도에 대한 조건을 충족하는 것을 알 수 있다.
이상으로 항복강도와 극한강도에 대한 요구 조건을 모두 충족하기 위해서는 샤프트에 부착된 요크 부위의 두께가 9.1 mm가 되어야 하는 것을 확인하였다. 따라서 샤프트의 요크 부위의 두께를 9.1 mm로 증가한 다음에 샤프트 전체에 대한 해석을 계속 수행하였다.
Fig. 10(a)와 같이 샤프트의 단면은 중공 원형의 형상을 가지고 있다(외부직경 do=18.54 mm, 내부직경 di=7 mm). 샤프트의 내부직경을 증가시키면서(두께를 감소시키면서), 샤프트의 자중을 얼마나 줄일 수 있는지 확인하기 위해서 다양한 내부직경의 크기에 대한 해석을 수행하였다. 해석에서는 외부직경을 do=18.54 mm으로 고정하고, 내부직경을 di=7, 8, 9, 10 mm으로 모두 4개의 크기를 고려하였다(Fig. 10(a)).
토크가 각각 280 Nm와 400 Nm일 때의 해석결과를 각각 Fig. 11과 Fig. 12에 도시하였다.
내부직경이 10 mm인 샤프트에서, 280 Nm의 토크가 가해질 때 최대응력은 386.09 MPa으로 항복강도인 382.23 MPa을 초과하였으며(Fig. 11(d)) 400 Nm의 토크가 가해 질 때 최대응력은 421.99 MPa로 극한응력 421.99 MPa에 도달하였음을 알 수 있다(Fig. 12(d)). 내부직경이 9 mm인 샤프트에서는, 280 Nm의 토크가 가해질 때 최대응력은 380.65 MPa으로 항복강도인 382.23 MPa보다 작으며(Fig. 11(c)) 400 Nm의 토크가 가해 질 때 최대응력은 411.67 MPa로 극한응력 421.99 MPa보다 작음을 알 수 있다(Fig. 12(c)). 따라서 샤프트의 내부직경을 초기의 7 mm에서 최대 9 mm까지 증가시켜도, 항복강도와 극한강도에 대한 요구 조건을 충족함을 알 수 있다.
3.2 튜브
튜브 끝단에 위치한 요크 부위의 구멍에 핀을 삽입하고, 이 핀의 표면 노드에 z-축을 중심으로 크기가 280 Nm와 400 Nm인 토크를 하중으로 부여하였다. 샤프트 외부 표면과 맞닿는 튜브 내부 표면의 모든 노드를 고정하는 경계조건을 사용하였다(Fig. 13).
Fig. 10(b)와 같이 튜브의 단면은 중공 원형의 형상을 가지고 있다(외부직경 do=28.0 mm, 내부직경 di=22.5 mm). 튜브의 외부직경을 감소시키면서(두께를 감소시키면서), 튜브의 자중을 얼마나 줄일 수 있는지 확인하기 위해서 다양한 외부직경의 크기에 대한 해석을 수행하였다. 해석에서는 내부직경을 di=22.50 mm로 고정하고, 외부직경을 do=28.0, 27.5, 26.5, 25.5 mm으로 모두 4개의 크기를 고려하였다(Fig. 10(b)). 토크가 각각 280 Nm와 400 Nm일 때의 해석결과를 각각 Fig. 14와 Fig. 15에 도시하였다.
외부직경이 25.5 mm인 튜브에서, 280 Nm의 토크가 가해질 때 최대응력은 386.50 MPa으로 항복강도인 382.23 MPa을 초과하였으며(Fig. 14(d)) 400 Nm의 토크가 가해 질 때 최대응력은 421.99 MPa로 극한응력 421.99 MPa에 도달하였음을 알 수 있다(Fig. 15(d)). 외부직경이 26.5 mm인 튜브에서는, 280 Nm의 토크가 가해질 때 최대응력은 381.05 MPa으로 항복강도인 382.23 MPa보다 작으며(Fig. 14(c)) 400 Nm의 토크가 가해 질 때 최대응력은 403.90 MPa로 극한응력 421.99 MPa보다 작음을 알 수 있다(Fig. 15(c)). 따라서 튜브의 외부직경을 초기의 28.0 mm에서 최대 26.5 mm까지 감소시켜도, 항복강도와 극한강도에 대한 요구 조건을 충족함을 알 수 있다.
3.3 설계 변경에 따른 자중 변화
초기 설계 형상과 변경된 형상에서의 인텀 샤프트 어셈블리의 자중을 아래 표에서 정리하였다. 샤프트의 경우, 샤프트에 연결된 요크 부위의 두께가 증가하였지만 샤프트의 내부직경을 증가(두께 감소)시키면서 초기 설계 자중 164.66 g을 159.64 g으로 줄일 수 있었다. 튜브의 경우, 외부직경을 감소(두께 감소)시키면서 초기 설계 자중 158.15 g을 136.88 g으로 줄일 수 있었다. 설계 변경을 통하여, 인텀 샤프트 어셈블리 전체의 자중 322.81 g을 296.52 g으로 감소시킴으로써 26.29 g(8.14 %)의 무게를 줄일 수 있게 되었다.
4. 회전 내구성 및 비틀림 내구성 요구 조건
인텀 샤프트 어셈블리의 내구해석을 위해서 상용 소프트웨어인 HyperLife를 사용하였다. 내구 해석을 위해서 구조 해석이 선행되어야 하는데, 구조 해석에서는 상용 소프트웨어인 Optistruct를 사용하여 토크 20 Nm 또는 29.4 Nm를 부여한 다음에 인텀 샤프트 어셈블리 전체에서 응력 분포를 구하였다.
내구 해석에서는, 샤프트에 연결된 요크 부위의 두께를 9.1 mm(Fig. 6), 샤프트의 내부직경을 di=9 mm(Fig. 10(a)), 튜브의 외부직경을 do=26.5 mm(Fig. 10(b))의 값을 사용하였다. 또한 경계조건으로 샤프트가 튜브에 최대로 삽입된 Fig. 5(a)와 같은 상태를 고려하였다.
4.1 회전 내구성 요구 조건
아래 표와 같은 조건을 부여할 때 인텀 샤프트 어셈블리가 100만 사이클 이상의 수명을 가질 것을 요구하는 것을 회전 내구성 요구 조건이라고 한다.14)
회전 내구 해석에서는, 인텀 샤프트 어셈블리의 축과 일치하는 축을 중심으로 샤프트에 연결된 핀에 20 Nm 크기의 정하중 토크를 부여한다. 이 때 튜브에 연결된 핀을 고정하는 경계조건을 사용한다(Fig. 16).

Intermediate shaft assembly which is used in the structural analysis. The axis of intermediate shaft assembly is in the direction of the axis of the applied torque
상용 소프트웨어인 Optistruct를 사용하여 토크가 20 Nm일 때 Fig. 16의 인텀 샤프트 어셈블리에 대한 구조 해석을 수행하였다. 그 결과를 아래 그림에 도시하였다(Fig. 17).
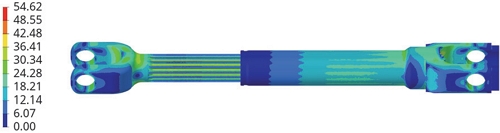
Stress distribution of intermediate shaft assembly under torque T=20 Nm. The axis of intermediate shaft assembly is in the direction of the axis of the applied torque
구조 해석의 결과와 상용 소프트웨어 HyperLife를 사용하여 회전 내구 해석을 수행하였다. 그 결과를 아래 그림에 도시하였다(Fig. 18, Fig. 19).
회전 내구 해석 결과 Damage의 크기는 거의 0이며 수명은 거의 무한임을 확인하였다. 따라서 인텀 샤프트 어셈블리의 현재 설계는 100만 사이클 이상의 회전 내구 수명을 충족함을 확인하였다.
4.2 비틀림 내구성 요구 조건
아래 표와 같은 조건을 부여할 때 인텀 샤프트 어셈블리가 100만 사이클 이상의 수명을 가질 것을 요구하는 것을 비틀림 내구성 요구 조건이라고 한다.14)
비틀림 내구 해석에서는, 인텀 샤프트 어셈블리의 축과 각도 12o 만큼 기울어진 축을 중심으로 샤프트에 연결된 핀에 29.4 Nm 크기의 정하중 토크를 부여한다. 이 때 튜브에 연결된 핀을 고정하는 경계조건을 사용한다(Fig. 20).
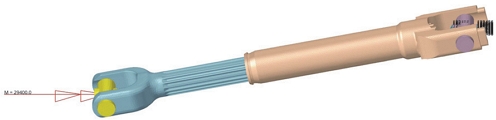
Intermediate shaft assembly which is used in the structural analysis. The axis of intermediate shaft assembly is tilted by 12o from the axis of the applied torque
상용 소프트웨어인 Optistruct를 사용하여 토크가 29.4 Nm일 때 Fig. 20의 인텀 샤프트 어셈블리에 대한 구조 해석을 수행하였다. 그 결과를 위 그림에 도시하였다(Fig. 21).
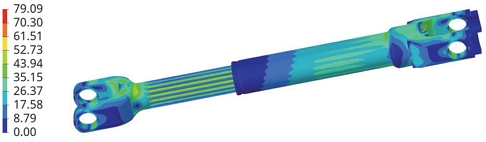
Stress distribution of intermediate shaft assembly as the results of structural analysis under torque T=29.4 Nm. The axis of intermediate shaft assembly is tilted by 12o from the axis of the applied torque
구조해석의 결과와 상용 소프트웨어 HyperLife를 사용하여 비틀림 내구 해석을 수행하였다. 그 결과를 위 그림에 도시하였다(Fig. 22, Fig. 23).
비틀림 내구 해석 결과 Damage의 크기는 거의 0이며 수명은 거의 무한임을 확인하였다. 따라서 인텀 샤프트 어셈블리의 현재 설계는 100만 사이클 이상의 비틀림 내구 수명을 충족함을 확인하였다.
5. 결 론
항복강도, 극한강도, 회전 내구성 및 비틀림 내구성에 대한 모든 요구 조건을 충족하는 인텀 샤프트 어셈블리를 설계하는 과정을 통하여 다음과 같은 결론을 얻을 수 있었다.
- 1) 기존의 인텀 샤프트 어셈블리는 200 Nm의 토크가 가해질 때, 항복강도 이하의 응력이 발생하여야 한다는 요구 조건을 충족하였다. 그러나 이 요구 조건에서 가해지는 토크의 크기가 280 Nm로 상향됨에 따라서 기존의 인텀 샤프트 어셈블리는 항복강도에 대한 요구 조건을 충족하지 못하게 되었다. 이에 따라서 샤프트 요크 부위의 두께를 7.7 mm에서 9.1 mm로 증가시켜서 항복강도에 대한 요구 조건을 충족할 수 있게 되었다.
- 2) 인텀 샤프트 어셈블리를 구성하는 샤프트의 내부직경을 7.0 mm에서 9.0 mm로 증가시키면서 샤프트의 두께를 감소시켜도, 샤프트가 항복강도와 극한강도에 대한 요구 조건을 모두 충족함을 확인하였다.
- 3) 인텀 샤프트 어셈블리를 구성하는 튜브의 외부직경을 28.0 mm에서 26.5 mm로 감소시키면서 튜브의 두께를 감소시켜도, 튜브가 항복강도와 극한강도에 대한 요구 조건을 모두 충족함을 확인하였다.
- 4) 설계 변경된 인텀 샤프트 어셈블리의 모든 부품이 회전 내구 100만 사이클 이상의 요구 조건을 충족하였다.
- 5) 설계 변경된 인텀 샤프트 어셈블리의 모든 부품이 비틀림 내구 100만 사이클 이상의 요구 조건을 충족하였다.
- 6) 설계 변경을 통하여 인텀 샤프트 어셈블리 전체의 자중을 322.81 g에서 296.52 g으로 줄임으로써 26.29 g(8.14 %)의 무게 경감의 효과를 거둘 수 있었다.
Acknowledgments
이 논문은 2021년도 한국기술교육대학교 교수 교육연구진흥과제의 지원 및 중소벤처기업부 기술개발사업[과제번호 S2950221]의 지원 결과입니다.
References
-
J. Hauhoff and R. Sedlmeier, Steering Column and Intermediate Steering Shaft, Steering Handbook, pp.215-248, 2017.
[https://doi.org/10.1007/978-3-319-05449-0_10]
-
T. Sebastian, M. S. Islam and S. Mir, Automotive Steering Systems, Handbook of Automotive Power Electronics and Motor Drives, CRC Press, pp.625-632, 2017.
[https://doi.org/10.1201/9781420028157-31]
-
M. Harrer and P. Pfeffer (Eds.), Steering handbook, Springer International Publishing, 2017.
[https://doi.org/10.1007/978-3-319-05449-0]
-
S. Lee, H. Lee, K. Koo and J. Woo, “Effects Analysis of I-Shaft Torque Modulation According to the True Position of Yoke Bearing Hole,” Transactions of KSAE, Vol.25, No.6, pp.742-749, 2017.
[https://doi.org/10.7467/KSAE.2017.25.6.742]
-
A. Emadi (Ed.), Handbook of Automotive Power Electronics and Motor Drives. CRC Press, pp.625-632, 2017.
[https://doi.org/10.1201/9781420028157]
-
A. Koparde, N. Mithra and S. Ahankari, “Numerical and Experimental Analysis of Torsional Stress of Traditional and Modified Steering Yoke,” Materials Today: Proceedings, Vol.46, pp.7099- 7104, 2021.
[https://doi.org/10.1016/j.matpr.2020.10.167]
-
J. -S. Kim, M. -J. Kim, O. -H. Kwon, K. -J. Oh, B. -I. Lee and S. Kim, “Computational Structural Analysis for Torsional Stiffness Test of Intermediate Shaft Assembly,” Journal of the Korean Society of Manufacturing Process Engineers, Vol.21, No.12, pp.88-93, 2022.
[https://doi.org/10.14775/ksmpe.2022.21.12.088]
-
C. Gandhi, P. Shinde, M. Rammamoorthi, B. Krshnadoss and A. Yadav, “Design and Analysis of Automotive Steering Sheet Metal Yoke for High Strength and Rigidity Requirement,” SAE 2019-28-0122, 2019.
[https://doi.org/10.4271/2019-28-0122]
-
S. Kang, B. Kim, D. Kim, H. Lee, I. Lee, J. Woo, H. Shin and Y. Ryu, “Developed Lightweight Aluminum Universal-joint with Improved High Temperature Performance and Rigidity,” Transactions of KSAE, Vol.28, No.5, pp.315-321, 2020.
[https://doi.org/10.7467/KSAE.2020.28.5.315]
-
A. Gupta, Arnav, V. P. Yashvanth and L. B. Rao, “Design of Gears Using Aluminium 6061-T6 Alloy for Formula SAE Steering System,” Recent Trends in Mechanical Engineering, Springer, pp.489-505, 2021.
[https://doi.org/10.1007/978-981-15-7557-0_41]
-
K. Miyake, T. Nishida, T. Kurokawa and H. Arai, “Sliding Properties of Polyamide Coating in High Temperature for Intermediate Shaft of Electric Power Steering,” SAE 2016-01-0507, 2016.
[https://doi.org/10.4271/2016-01-0507]
-
J. H. Cho, S. W. Yoon, T. Y. Kim, M. H. Kim and Y. H. Kim, “A Study on the Design for High-Strength Composites Applied to the Intermediate Shaft,” International Journal of Modern Physics B, Vol.32, No.19, Paper No.1840048, 2018.
[https://doi.org/10.1142/S0217979218400489]
-
W. Bang and K. Lee, “Design of Lightweight Steering Intermediate Shaft Which Satisfies Requirements for Static Strength and Fatigue Life,” Transactions of KSAE, Vol.30, No.7, pp.575-579, 2022.
[https://doi.org/10.7467/KSAE.2022.30.7.575]
- Hyundai Motor Co., Engineering Standard 56400.
- ASTM International, ASTM E8: Standard Test Methods for Tension Tesing of Metallic Materials, Annual Book of ASTM Standards, 2021.