
차륜형장갑차 실내용 흡음재 성능개선 및 엔진 인캡슐레이션을 통한 주행 실내소음 개선 연구
Copyright Ⓒ 2021 KSAE / 185-07
This is an Open-Access article distributed under the terms of the Creative Commons Attribution Non-Commercial License(http://creativecommons.org/licenses/by-nc/3.0) which permits unrestricted non-commercial use, distribution, and reproduction in any medium provided the original work is properly cited.
Abstract
In the defense industry and automobile industry, the importance of noise reduction is emerging for the hearing protection of the occupants and the operational meetings conducted in vehicles. In this research, in order to reduce the driving interior noise of a wheeled armored vehicle, the sound absorption coefficient was improved by material selection and layer optimization. Then, the engine-radiated noise was reduced by powerpack encapsulation using high heat-resistant material, and the engine temperature increase was evaluated via driving test. As a result, the weight of the sound absorption material was reduced by 21 kg, and the driver and passenger noise was improved by 2.4 dB and 3.1 dB. Articulation Index(AI, %) was increased by 10.8 %p and 7.0 %p, respectively.
Keywords:
Wheeled armored vehicle, Driving interior noise, Sound absorption material, Articulation index, Encapsulation키워드:
차륜형장갑차, 주행실내소음, 흡음재, 명료도 지수, 인캡슐레이션1. 서 론
차량 운행간 실내소음은 주행노면, 풍절음, 엔진 및 구동계 소음 등에 의해 발생된다. 자동차 산업에서 시험과 해석을 통한 저소음 설계 기술이 큰 발전을 이루었으나, 흡차음재 최적화 기술이 실내소음 저감에 널리 사용되고 있으며 소재 및 배열 최적화를 통한 경량화, 실내 음질 개선이 요구되고 있다.
또한 디젤엔진을 사용하는 승용차량을 대상으로 높은 면밀도가 사용되는 차음재 대신 엔진 표면에 경량화 가능한 고내열 흡음재를 부착하는 인캡슐레이션을 통하여 정차 및 주행간 실내소음과 음색을 개선한 연구들이 보고되고 있다. 타이밍 벨트 커버, 블록패널, 오일팬, 상부 밸브커버 등 디젤엔진의 특정지점에 소음커버를 직접 부착하는 방식의 연구가 수행되는데 이러한 연구들은 특정주파수 소음저감을 위한 것으로 소음레벨을 줄이기 위해서는 엔진 전체를 인캡슐레이션 하는 것이 효과적이다.1)
최근에는 자동차산업뿐만 아니라 방위산업에서도 조종수 및 탑승자의 청력 보호, 차량 내 작전회의 등의 이유로 군용 차량의 소음 저감 중요성 또한 대두되고 있다. 이를 위해 본 연구에서는 차륜형장갑차를 대상으로 공기기인소음(Air-borne noise) 저감을 통해 조종수석 및 보병석 소음과 더불어 대화 명료도를 개선하였다. 흡음재 소재 및 레이어 최적화 시험을 거쳐 기존 사양 대비 경량화 및 흡음률 개선을 확인하고 차량 적용 시험 수행 후 엔진 인캡슐레이션을 통해 실내소음 저감 및 대화명료도 개선효과를 검증하였다. 시험 대상차량은 직렬 6기통 10 L급 420마력 H엔진을 적용하고 있으며 국군 보병부대의 수송, 보병전투 등 임무수행을 지원한다.2)
본 연구 결과는 차량 실내소음 저감을 위한 흡음재최적화에 활용할 수 있으며, 특히 앞서 연구되지 않은 10L급 디젤엔진의 인캡슐레이션은 엔진룸 내벽이 아닌 엔진 표면을 차폐시키는 방식을 적용하여 군용장비와 더불어 버스, 상용차량 등의 NVH 성능 개선에 활용 가능할 것으로 보인다.
2. 이론적 배경
차량 실내용 흡음재가 갖추어야 할 조건은 성능을 나타내는 흡음률, 면밀도, 두께 등이 있으며 실내 적용을 위한 난연성, 단열성능, 분진 및 냄새 또한 고려하여야 한다.
2.1 흡음률
자동차용 흡음재의 흡음률을 측정하는 방법에는 수직 입사음에 대한 임피던스관(Impedance tube)의 전달함수법(Transfer function)과 난방향 입사음에 대한 잔향실법(Reverberation chamber)이 있으나, 실제 자동차 소음 방사조건을 고려했을 때 간이 잔향실법이 확산음장으로 이루어져 있어 실제 자동차 환경과 동일하기 때문에 주로 간이 잔향실법이 사용된다.3,4)
Fig. 1에서 나타낸 것과 같이 1차원 수직입사 음장에서 음압 p(x)는 흡음재에 입사파와 반사파의 합으로 표현되며 식 (1)과 같이 표현할 수 있다.
(1) |
1번과 2번 위치의 전달함수(H12)를 반사계수()를 이용하여 표현하면 아래와 같다.
(2) |
(3) |
위의 반사계수와 임피던스(Z), 공기의 밀도(ρ), 음속(c)으로 흡음률을 표현하면, 수직입사 흡음률은 식 (5)로 구할 수 있다.5,6)
(4) |
(5) |
잔향실법 시험방법은 난입사 조건에서의 잔향시간 계측을 통한 흡음률 측정 방법으로, 주파수 영역이 100~10 kHz까지 전 주파수에 걸쳐 현실적인 흡음률 측정이 가능하나 잔향실 용적이 큰 만큼 유지보수와 상당한 크기의 시험편 관리에 어려움이 있어, 차량 용적면적과 유사한 간이잔향실(Alpha cabin)로 흡음률을 평가할 수 있다.7) 흡음률은 Fig. 2와 같이 초기상태(공실)와 흡음재 설치 후 잔향시간(-60 dB, RT 60)의 차이를 이용하여 세이빈(Sabine)식으로 계산할 수 있으며 아래 식 (6)과 같다.
(6) |
여기서,
as = 흡음률
C = 측면효과 보정계수
V = 간이잔향실 체적, m3
S = 흡음재 표면적, m3
T0 = 빈 상태에서의 잔향시간, sec
T1 = 흡음재가 있는 상태에서의 잔향시간, sec
2.2 엔진 인캡슐레이션
엔진 인캡슐레이션은 차량 주요 소음원인 파워트레인을 차폐하는 기술로 아이들 및 주행 시 소음저감이 가능하며, 아래의 Fig. 3과 같이 그 형태에 따라 엔진 표면에 직접 부착하는 EME(Engine-Mounted Encapsulation) 방식과, 엔진룸 주변 바디에 부착하는 BME(Body-Mounted Encapsulation) 방식으로 나눌 수 있다.8)
BME 방식은 엔진룸 내벽을 차폐하는 기술로 많은 양의 흡음재가 필요하지만 형상이 비교적 단순하여 차량 개발 공정에 큰 영향을 주지 않는다. EME 방식은 파워트레인에 직접 부착하는 기술로 열원에 가까이 노출되어 내구성을 확보해야 하지만, 소량의 흡음재로 큰 소음개선효과를 기대할 수 있다.9) EME 방식에서 소재 선정 시 140 °C 이상의 엔진표면 온도, 오일과 연료에 의한 오염 보호, 냉각 공기의 유동저항, 난연성 및 안전성과 내구성을 고려하여야 하며 양산성 측면에서는 소재의 제조, 엔진표면 부착 방식, 열전도성, 생산비용 등을 검토하여야 한다.
2.3 명료도 지수
차량 실내에서 배경 소음에 의해 방해 받지 않고 상대방과 의사소통 할 수 있는 정도를 정량적으로 표현할 수 있는 방법으로 명료도 지수(Articulation Index, AI(%))가 있다. 주파수별 측정된 소음 레벨에 사람의 청각 민감도를 반영하여 규정된 AI(%)를 부여하고, 이를 관심 주파수 대역별 값에 대해 합산된 총계로 음질을 평가한다.3) 즉, 소음에 의해 대화를 방해 받지 않는 정도를 0~100 %로 평가하는 방법으로 100 %는 주변 소음에 방해 없이 대화할 수 있고, 0 %는 소음으로 인해 대화를 할 수 없는 상태를 나타낸다. 아래 Fig. 4의 주파수별 대화 가능한 소음레벨 범위를 바탕으로 AI를 계산하면 식 (7)과 같다.10)
(7) |
여기서,
200 Hz ≤f≤ 6 kHz 1/3 옥타브 밴드
Lu(f) : 대화 가능한 소음레벨 상한치, dB
Ll(f) : 대화 가능한 소음레벨 하한치, dB
L(f) : 소음 스펙트럼, dB
P(f) : 주파수별 보정계수
3. 시 험
차륜형장갑차에 실내 설치된 기존 흡음재와 개선 흡음재를 대상으로 비교시험 진행 후 최적사양을 반영하여 차량 주행간 소음저감효과를 검증하였다. 이후 엔진과 변속기를 EME 방식의 인캡슐레이션 기술을 적용하여 추가 소음개선을 수행하였다.
3.1 소재 흡음률 시험
현재 차륜형장갑차 실내에 적용중인 흡음재는 극세사, PET(Polyethylene Terephthalate), PU폼(Poly Urethane foam) 등의 적층 구조로 이루어져 있으며 냄새, 경화방지, 난연성 등 실내 사용 적합성을 갖추고 있다. 실내 사용 적합성은 유지한 채 경량화 및 흡음률 개선을 통한 차량소음 저감을 위해 아래 Fig. 6의 간이잔향실(Alpha cabin)을 이용하여 흡음률을 평가하였다.11) 기존사양 대비 소재 조성, 두께, 밀도, 적층 순서를 조절하며 약 40여종의 시편에 대한 흡음률을 평가하여 최적의 소재 및 레이어를 선정하였다.12,13)
Fig. 7과 8은 흡음률 시험 결과 중 주요 개선안 3종에 대한 결과를 나타내고 있다. 흡음률이 1.0 이상이 나타나는 것은 간이잔향실법에 의한 흡음률 계산에서 보정 값(C)에 의해 나타나는 현상이며, 차량용 흡음시험에 사용하는 통상적인 값을 사용하였다. 개선사양 1은 극세사-PET, 개선사양 2는 PET-극세사-PET, 개선사양 3은 극세사-PET-극세사-PET로 구성되어 있다. 각각의 소재 및 레이어는 서로 다른 밀도, 두께, 소재 조성, 제조공정으로 제작되었다.
NRC(Noise Reduction Coefficient: 500, 1 k, 2 k, 4 kHz 평균 흡음률) 개선률 비교결과 기존 0.77에서 1안 44 %, 2안 46 % 그리고 3안은 40 %가 개선되었다. 주파수별 흡음률 그래프를 살펴보면 개선안 3종 모두 동일한 경향으로 중저주파(0~1 kHz) 영역에서 140 % 내외로 크게 개선되고, 고주파(1~10 kHz)에서 20 % 내외로 개선됨을 확인할 수 있다. 3종 모두 기존 중량대비 25~30 % 경량화를 보이고 있으며, 향후 생산성을 고려하여 최적 사양인 1안으로 선정 후 차량 소음저감 검증시험을 진행하였다. 1안의 경우 기존 사양과 대비하여 30 %의 중량 저감을 실현하였다. 장치류 및 보강재 근처 흡음재 설치를 고려한 최대 두께로 설계하여 2배 내외의 증가된 두께를 사용하였으나, 승용 및 상용 차량과 달리 차륜형장갑차는 천정과 측벽 모두 보병좌석에서의 여유공간이 확보되어 있어, 임무수행에 차질이 없도록 하였다.
Fig. 9는 추가 소음개선에서 엔진 및 변속기 인캡슐레이션에 사용 될 소재에 대한 흡음시험 결과이다. 차륜형장갑차 운용환경 분석을 바탕으로 엔진 연소, 배기계통의 온도를 고려한 고내열 소재와 중저주파 흡음률을 보강하기 위한 소재, 시험 간 흡음재 파워팩 체결성을 고려한 소재 등을 사용하였다.
3.2 차량 소음 시험
차륜형장갑차를 대상으로 개선 흡음재에 대한 차량 소음저감효과를 분석하였다. 현재 적용중인 흡음재는 보병석 상부, 측면 및 조종수석에 설치되어 있으며 현 상태에서 기준소음을 평가 후 개선 흡음재로 교체하여 정속 주행 간 조종수석, 보병석 소음저감효과를 분석하였다. 시험장비는 LMS TestLab, B&K 마이크로폰, PCB 가속도계 및 V-Box를 사용하고 측정 위치는 Fig. 10과 같다.
소음저감효과 평가의 신뢰성을 높이기 위해 Fig. 11과 같이 차량 운행 간 이상소음 및 진동이 발생할 수 있는 외부 거치대, 손잡이류, 클램프 등 장치류들을 고정하고 체결장치를 점검하였다.
아래 Fig. 12의 (a)는 조종수석과 보병석에 설치된 흡음재를 나타낸 것이며 (b)와 (c)는 각각 현재 부착중인 흡음재와 개선효과 검증시험을 위한 시편 제작 후 부착된 모습이다. 차량 주행 간 조종수석과 보병석의 주파수 영역별 소음 평가결과는 Fig. 13과 같다. 개선 전 소음레벨을 기준(0 dB)으로 개선량을 그래프로 나타낸 것이다.
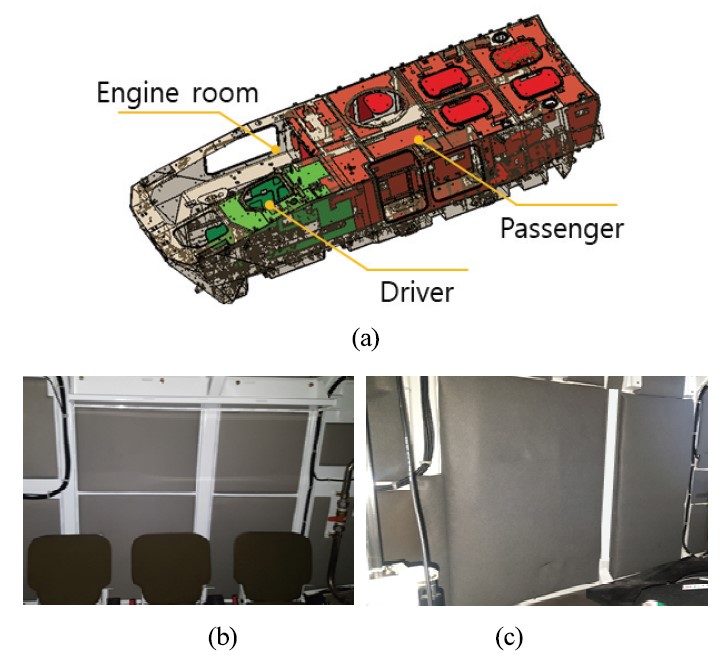
Installation of improved sound absorption material: (a) the driver and passenger location (b) current and (c) improved SAM (Sound Absorption Material)
조종수석과 보병석의 흡음성능 개선에 의해 전체소음레벨(Overall)은 조종수석 1.3 dB, 보병석 2.8 dB이 개선되었다. 주파수 영역별 결과를 보면 저주파수(0~500 Hz)는 조종수석 1.1 / 보병석 2.8 dB이며 중주파수(500~1 kHz)는 조종수석 4.8 / 보병석 3.1 dB, 고주파수(1 k~20 kHz)는 조종수석 3.1 / 보병석 1.8 dB이 저감되었다. 잘 알려진 바와 같이 흡음재에 의한 소음저감효과는 저주파 대비 중고주파에서 크게 나타났다. 조종수석이 보병석에 비해 상대적으로 파워팩과 인접해있어 저주파 소음이 크게 나타나기 때문에 흡음재에 의한 소음레벨 저감효과는 낮아 보이며, 저주파 소음이 작은 보병석의 소음레벨 저감효과는 크게 나타난다.
실내 흡음재 개선효과 검증시험 후 개선흡음재가 설치된 상태에서 추가 실내소음 저감을 위해 엔진 및 변속기 인캡슐레이션을 수행하였다.
흡음재 중량 및 부착면적 대비 효과적인 소음 개선을 고려하여 EME 방식을 채택하고 흡음재 고정방법, 레이아웃, 사용온도, 소재 내열 및 성능저하를 고려하여 Fig. 14와 같이 흡음소재를 적층하여 배치하였다.
Fig. 15는 (a)조종수석과 (b)보병석의 소음저감효과를 나타내고 있다. 실내 흡음재 성능개선 후 엔진과 변속기 인캡슐레이션으로 조종수석 및 보병석 전체소음 각각 1.1 / 0.3 dB 추가 개선하여, 기존차량 대비 조종수석 2.4 dB, 보병석 3.1 dB을 개선하였다. 주파수 영역별 결과는 Fig. 15에서 보는 것과 같이 조종수석은 저주파 2.3 중주파 5.0 고주파 4.6 dB, 보병석은 저주파 2.9 중주파 4.3 고주파 2.1 dB이 개선되었다. 엔진과 변속기 소음의 흡음 및 차폐 효과에 의해, 주요 소음원인 파워팩과 인접한 조종수석 소음이 인캡슐레이션에 의한 개선 효과가 우수하며, 그중에서도 소음레벨이 높은 저주파영역에서 크게 저감되었다.
최종 시험의 결과에서 볼 수 있는 것처럼 중고주파에서의 소음저감효과는 조종수석 기준으로 4~5 dB로 크게 개선되기 때문에 동일 장비에서 저주파 구조기인소음 개선 후 본 연구내용을 적용할 경우 소음레벨이 크게 개선될 것으로 보인다.
소음 저감에 따른 AI(%) 분석 결과는 Fig. 16과 같다. 흡음재 성능개선 시 기존차량 대비 조종수석 7.8 %p, 보병석 5.7 %p 개선되었다. 흡음재 성능개선과 파워팩 인캡슐레이션 후 AI(%)는 소음 저감에 의하여 크게 개선되었으며, 기존차량 대비 조종수석과 보병석 각각 10.8 %p, 7.0 %p 개선되어 29.5 %, 21.5 %로 향상되었다.
AI(%)에 따른 명료도를 5단계로 구분하면 불가능(5이하), 미흡(5~20), 보통(20~30), 우수(30~70), 매우우수(70 이상)로 나눌 수 있는데 기존 차량은 조종수석과 보병석 모두 미흡한 수준이다.14) 개선 후 명료도 보통 수준이 되어 육성에 의한 의사소통이 개선되었다. 조종수는 별도의 장치를 이용하여 차외 통신을 할 수 있으나 차량 내 조종수와 보병 또는 보병 간 의사소통은 육성을 통해 이루어짐으로 AI(%)개선을 통해 군 임무수행에 도움이 될 것으로 보인다. 다만, 차량 주행 간 실내에서의 원활한 의사소통을 위해서는 별도의 통신장치가 필요할 것이다.
엔진 인캡슐레이션 전후 흡음재의 단열효과에 의한 온도 상승을 평가하기 위하여 엔진블럭 표면에 써모커플을 설치하여 온도변화를 측정하였다. 가장 온도가 높은 엔진 우측 배기장치 부근 한 지점의 인캡슐레이션용 흡음재 안쪽 엔진표면에 설치하였으며 동일한 차량 운행조건으로 인캡슐레이션 전후 각각 안정화 온도가 될 때까지 측정하였다. 엔진표면온도가 정상상태가 되기까지 약 20분이 소요되었으며, 각각 91 °C에서 94 °C로 측정되어 해당 위치에서 엔진 인캡슐레이션에 의한 온도 상승은 3 °C 내외로 차량 운행 간 엔진 냉각에 미치는 영향은 크지 않은 것으로 보인다.
4. 결 론
본 연구에서는 차륜형장갑차의 흡음재 성능개선을 통한 실내소음 저감을 위해 간이 잔향실을 이용하여 흡음재의 흡음률을 측정하고 경량화를 고려한 최적의 흡음재 사양을 선정하였다. 차량에 설치된 기존 흡음재를 교체 후 소음 개선효과를 평가하였으며, 엔진과 변속기 인캡슐레이션으로 추가 소음 개선하였다. 이를 통해 다음과 같은 결론을 얻었다.
- 1) 흡음재 샘플시험을 통해 기존 실내 흡음재 대비 흡음률(NRC)을 44 % 개선하고 중량 30 %를 저감하여 차량 중량 21 kg을 개선하였다.
- 2) 직렬 6기통 10 L급 420마력 엔진을 탑재한 차륜형장갑차 실내 흡음재를 개선사양으로 교체하여 정속주행 간 조종수석 소음 1.3 dB 보병석 소음 2.8 dB을 저감하고, AI(%)는 각각 7.8 %p, 5.7 %p 개선했다.
- 3) 실내 흡음재 개선에 추가 소음개선 연구로 EME 방식의 엔진 및 변속기 인캡슐레이션을 통해 기존차량 대비 조종수석 2.4 dB 보병석3.1 dB 저감하고, AI(%) 또한 각각 10.8 %p, 7.0 %p 개선하였다.
- 4) 특히 흡음재 개선에 의해 500 Hz 이상 영역의 소음이 크게 저감되고 인캡슐레이션을 통해 파워팩과 가장 인접한 조종수석 소음이 크게 개선되는 것으로 보아, 저주파 구조기인소음 개선 후 본 연구 결과인 개선흡음재와 인캡슐레이션을 적용할 때 실내소음은 크게 개선될 것이다.
- 5) 엔진 인캡슐레이션에 의한 엔진 온도상승은 3 °C 내외로 차량 운행 간 엔진 냉각에 미치는 영향은 크지 않음을 확인하였다.
향후 연구 활동으로는 인캡슐레이션 소재의 위치별 두께, 밀도, 레이어 최적화와 흡음재 부착으로 인한 엔진룸 내 유동저항에 대한 해석 연구가 진행될 예정이다. 본 연구결과는 군용 전투차량뿐만 아니라 승용, 상용차량 및 버스 등의 소음개선 연구에 활용될 수 있다.
Nomenclature
α : | sound absorption ratio |
A : | amplitude of sound, m |
ω : | angular velocity, rad/s |
rp : | reflection coefficient |
γ : | phase difference when incident sound is reflected, rad |
References
- S. S. Nathak, M. D. Rao and J. R. Derk, “Development and Validation of an Acoustic Encapsulation to Reduce Diesel Engine Noise,” SAE 2007-01-2375, 2007.
- Defense Media Agency, “Journal of defense-July,” No.511, pp.50-53, 2016.
- J. W. Lee, S. N. Lee, J. H. Shim, P. K. Jung, W. K. Lee and B. J. Bang, “The Study on Improvement of Acoustic Performance for Automobile Sound-absorbing Materials Using Hollow Fiber,” Transactions of the Korean Society for Noise and Vibration Engineering, Vol.21, No.9, pp.850-857, 2011.
- J. W. Lee, J. H. Gu, H. K. Park and D. J. Kang, “Comparison of Absorption Coefficient According to Test Methods,” Transactions of the Korean Society for Noise and Vibration Engineering, Vol.17, No.5, pp.373-378, 2007.
- ISO 10534, Acoustics - Determination of Sound Absorption Coefficient and Impedance in Impedance Tube, 1998.
- M. Kimura, J. Kunio, A. Schuhmacher and Y. Ryu, “A New High-frequency Impedance Tube for Measuring Sound Absorption Coefficient and Sound Transmission Loss,” Inter-noise, 2014.
- K. W. Yang, “Automotive Performance Sound Absorption, Insulation Technology Trends,” Prospective of Industrial Chemistry, Vol.16, No.6, pp.2-10, 2013.
- S. Lee, J. K. Namgung, H. K. Mo and O. K. Ahn, “Improvement of Interior Noise Using Engine Encapsulation,” Proceedings of the KSNVE Annual Spring Conference, pp.412-415, 2015.
- G. S. Lee, S. W. Han and H. C. Kim, “Development Trend of Engine Encapsulation,” KSAE, Auto Journal, Vol.36, No.12, pp.16-19, 2014.
- H. Onusic, E. L. Baptista and M. M. Hage, “Using SIL/PSIL to Estimate Speech Intelligibility in Vehicles,” SAE 2005-01-3973, 2005.
- P. C. Lee, S. K. Jeoung, J. U. Ha, B. R. Kim and J. K. Han, “Flame Retardancy and Sound Absorption Properties of Polyurethane/Expandable Graphite Foams,” Transaction of KSAE, Vol.27, No.6, pp.441-445, 2019.
- K. J. Kim, S. H. Kim and J. K. Park, “Investigation of Sound Absorbing Characteristics of the Railway Noise Barrier by Changing the Configuration of the Front Perforated Panel and Absorbing Material,” Proceedings of the KSNVE Annual Autumn Conference, pp.575-580, 2013.
- J. W. Oh, J. H. Lee, K. S. Kim, J. H. Lee, S. H. Lee and H. S. Kim, “The Study on Shift of Absorption Coefficient by Finishing Layer,” Proceedings of the KSNVE Annual Autumn Conference, pp.477-481, 2015.
- A. Michaud, “Silence is Golden: Optimizing the Acoustic Environment,” Price Industries, 2019.