
설계변수에 따른 알루미늄 범퍼 시스템의 저속 충돌해석
Copyright Ⓒ 2017 KSAE
Abstract
In the present study, the low speed (4 km/h) crash behaviour of an aluminium bumper system was characterised by FE analyses based on the FMVSS 581, which regulates automotive bumpers. Two types of cross-sectional designs, i.e., Model 1, which contains a single rib and Model 2, double ribs, have been considered along with Al7021, 6082 and 6060 for the aluminium bumper back beam. Variations in thickness starting from 2 to 4 mm of the bumper system cross-section in the FE model was implemented in order to investigate the thickness effect on the bumper’s crash behaviour.. Three kinds of design variables, namely, number of ribs, material and thickness, are considered. The FE analysis results are summarised with the maximum load and the Specific Energy Absorption (SEA) since they are the key factors in determining the crashworthiness of automotive structures. The results may also be able to indicate how to achieve lightweight structure of the automotive bumper system either directly or indirectly.
Keywords:
Crash behaviour, Design variable, Bumper standard, FMVSS part 581, Specific Energy Absorption, SEA키워드:
충돌해석, 설계변수, 범퍼 규격, 단위 질량당 흡수에너지1. 서 론
최근 고 안전 부재들이 위치한 전방 차체 구조물에 알루미늄 적용을 확대하여 차체 경량화와 차량충돌 성능을 확보하고 있다. 일반적으로 알루미늄차체는 기존 철강재 대비 동일한 차체강성을 만족시킬 때 약 30 % 수준의 경량화가 가능한 것으로 알려져 있다.1,2) 그리고 동일한 차체강성을 보상하기 위해 알루미늄 소재 두께가 증가됨에 따라 차체 굽힘・비틀림 강성 증가와 내구수명 측면에서 우수할 뿐만 아니라, 경량화에 따른 고유진동수 증가 효과가 있다. 또한, 알루미늄 압출재는 철강재에 비하여 고가이지만 부품을 일체 성형 할 수 있어 제품 생산공정을 줄이고 가공 공정을 차별화하면 가격 상승을 억제할 수 있다. 그리고 압출형상의 자유도가 있어 구조적인 강성 보강이 가능하며 균일한 품질의 제품을 연속적으로 생산 할 수 있는 장점이 있어 자동차구조용 부재로 알루미늄 압출재의 적용이 확대되고 있다.3,4)
그래서 차량의 안전성 확보를 위한 중요한 범퍼 시스템에 알루미늄 압출재를 적용하려는 연구가 계속적으로 확대되고 있다. 범퍼 시스템은 차량 충돌 시 발생하는 충돌에너지가 차체에 전달되기 전에 흡수하여 차체 및 승객을 보호하는 것이 목적이기 때문에, 경량화를 이루면서 높은 강도를 유지할 필요가 있다. 범퍼 시스템은 크게 커버(cover), 폼(foam) 구조의 충격흡수재, 범퍼 백빔(bumper back beam), 스테이(stay)로 구성되며, 이 중 범퍼 백빔과 스테이는 차체사이드 멤버(side member)에 장착되어 충돌 시 대부분의 충돌에너지를 흡수한다.5-9) 그래서 안전성 확보를 위해 범퍼 시스템의 저속(4 km/h, 8 km/h)충돌 시 차체 및 승객에게 피해를 입히지 않을 것을 각국에서 강제 법규로 규정하고 있다.7,11) 강제 법규는 저속 충돌 시 차체로 전달되는 충돌에너지가 범퍼 시스템의 적절한 변형 발생으로 흡수되어 최소화해야 함을 규정하고 있다.10) 범퍼 시스템 안전성을 평가하기 위한 시험조건은 우리나라의 경우 자동차안전기준 시행세칙에 명시하고 있으며, 미국에서는 미연방 도로교통안전국(NHTSA)의 FMVSS (Federal Motor Vehicle Safety Standards) Part 581에서 명시하고 있다.11)
기존의 많은 범퍼 시스템 연구가 차량 수리비용에 대한 관점에서 비용절감에 초점을 두고 있는데,12,13) 이것은 경제적인 측면에서는 중요하다. 하지만 경량화에 의한 안정성을 동시에 추구하는 측면에서는 충분한 에너지 흡수력과 강도 확보를 위한 기초연구와 DB구축이 필요하다. 따라서 범퍼 시스템 설계 초기단계에서부터 해석적 방법으로 재질이나 구조물의 형상, 두께 등에 대한 기초연구의 필요성이 요구되고 있다.
본 논문에서는 알루미늄 압출재를 적용하여 새로운 구조적 안전성이 고려된, 두 종류(Model 1, 2)의 범퍼 시스템을 선정하였다. 그리고 범퍼 시스템의 기초연구로 FMVSS Part 581에서 정의하는 범퍼 규격을 참조하여 4 km/h의 저속 충돌해석을14,15) 진행하였다. 그리고 재질·두께별 특성 평가를 위한 변수로 세 종류의 압출 알루미늄(Al7021-T7, Al6082-T6, Al6060-T6), 두께변경은 범퍼 백빔과 크래쉬 박스(crash box)로 결정하였다. 전체 고정변수로 무게를 4 kg으로 정하였다. 평가분석을 위해 충돌에 의한 최대하중과 이때 발생되는 단위 질량당 흡수에너지(Specific Energy Absorption, SEA)를 기준으로 결과를 비교분석하였다.
2. 범퍼 시스템의 충돌해석
2.1 유한요소 해석 모델
본 논문에서는 자동차 범퍼 시스템 규격인 FMVSS part 581을 적용하였으며, 평가를 위한 충돌해석용 모델은 Fig. 1과 같이 두 가지 모델(Model 1, 2)을 선정하였다. 두 모델의 차이는 범퍼 백빔 내부에 보강된 리브(rib)의 차이가 되겠다. 모델 구성은 범퍼 백빔, 크래쉬 박스, 플레이트로 구성된다. 이렇게 정해진 범퍼 시스템의 충돌해석을 위하여 전처리 과정을 마친 모델은 Fig. 2와 같다. 요소분할은 약 4 mm의 요소크기로 하였으며, 두께 변화에 따른 영향을 분석하기 때문에 쉘(shell) 요소로 모델링을 진행하였다. 요소 수는 Model 1, 2 약 24300, 26300개로 되었다. Fig. 3 차량의 무게중심점(center of gravity)에 차량무게 약 2000 kg의 무게를 정의하고, 플레이트와 강체(rigid)로 연결하여 차량 무게가 정의 될 수 있도록 하였다. 그리고 각 부재 접합방법인 용접과 볼팅은 강체로 연결하여 접합부를 모사하였다. 마지막으로 충돌해석 조건은 고정 벽(rigid wall)에 4 km/h (2.5 mph)의 속도로 해석이 진행되었다.
2.2 범퍼 시스템 설계변수의 다변화 및 분석
먼저 범퍼 시스템의 최적화를 위하여 목표 무게를 4 kg로 설정하였다. 또한 제안된 Model 1, 2 모델의 소재는 세 가지 종류의 알루미늄 압출재(Al7021-T7, Al6082-T6, Al6060-T6(이하, 7021, 6082, 6060))를 적용하였으며, 소재변화에 따라 Table 1처럼 6가지의 변수 조합을 구성하였다. 그리고 두께 변화(2, 3, 4 mm)를 달리하면서 범퍼 백빔과 크래쉬 박스를 Table 2처럼 9가지로 변수 조합을 구성하였다. 그리고 Table 3에는 9가지의 두께 변화에 따른 무게를 나타내었다.
Table 1, 2의 변수 조합을 합치면 총 54가지(Case A1 ~ F8)의 설계변수가 구성된다. 플레이트는 소재 6060에 두께 4 mm의 고정변수로 정하여 설계변수에서 제외하였다. 그리고 본 논문에서 사용된 알루미늄 압출재의 진응력-진변형률 선도를16,17) Fig. 4에 정리하여 나타내었다.
충돌해석에서 도출되는 하중-변위의 면적이 범퍼 시스템이 흡수한 흡수에너지가 되며, 단위질량당 흡수에너지는 흡수에너지를 범퍼 시스템의 질량으로 나눈 값으로 식 (1)과 같이 구할 수 있다.
(1) |
여기서, ES : 단위질량당 흡수에너지, EA : 흡수에너지, MB : 범퍼 백빔의 질량, MC : 크래쉬 박스의 질량을 나타낸다.
3. 충돌해석 결과
충돌해석을 진행한 결과를 세 가지 유형으로 정리하였는데, 유한요소해석 Model 1, 2의 충돌특성에 대한 분석과 단위 질량당 흡수에너지 변화에 관하여 분석으로 정리하였다. 참고로 Model 2의 No.9는 전체 무게가 4 kg가 초과하지만 결과 비교를 위하여 참고자료로 삽입하였다. 그리고 적절한 범퍼시스템의 강도를 만족하는 최대하중 범위 선정은 선행연구18,19)에 나타난 최대하중(80 kN~ 110 kN)을 기준으로 비교 평가하였다.
3.1 Model 1의 충돌특성
Fig. 5(a)에 범퍼 백빔의 두께 변화에 따른 영향을 정리하여 나타내었다. 고정변수가 두께 2 mm의 크래쉬 박스인 경우 강도가 높은 7021보다 6082인 경우에 최대하중이 상대적으로 높게 나타났다. 범퍼 백빔의 두께가 두꺼워 짐에 따라 Case A ~ F의 최대하중 분포범위가 최대 28 kN에서 10 kN으로 감소하는 결과를 보였다. 그리고 Case B, E외의 Case는 같은 재질의 크래쉬 박스 Case끼리 유사하게 최대하중변화가 나타났다.
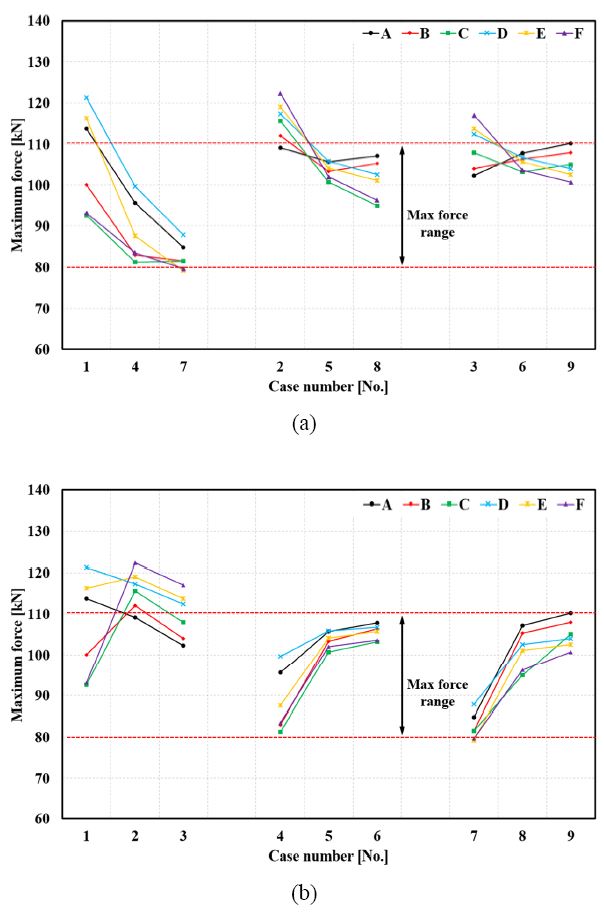
Comparison with analysis result of model 1: (a) Effect of bumper back beam thickness, (b) Effect of crash box thickness
고정변수가 두께 3 mm의 크래쉬 박스인 경우 범퍼 백빔의 두께가 증가할수록, 최대하중의 분포범위는 감소하였다 다시 확대되는 경향을 보였다. 그리고 Case A, B만은 범퍼 백빔 두께가 두꺼워짐에 따라 최대하중이 낮아지지 않고, 다시 높아지는 특성을 나타냈다. No.2에서는 Case F에서 A로 순차적으로 최대하중이 낮아지는 특징을 보이고 있다. 이것은 No.8에도 같은 양상을 보이고 있다. 그리고 No.5에서는 Case A와 D, B와 E, C와 F가 짝을 지어 최대하중이 유사하게 나타났으며, No.8 경우에는 Case A와 B, D와 E, C와 F가 짝을 지어 최대하중이 유사하게 나타났다. 이것은 크래쉬 박스의 두께와 범퍼 백빔의 두께가 같거나 두꺼워지면 크래쉬 박스의 재질 강도에 최대하중이 영향을 받는다고 생각된다.
고정변수가 두께 4 mm의 크래쉬 박스인 경우 범퍼 백빔이 7021일 때 두께가 증가하면 최대하중도 같이 증가하는 경향을 보였지만, 6082일 경우 두께가 증가하면 최대하중은 반대로 감소하는 경향을 보였다. 예외적으로 Case C는 위의 두 가지 재질의 혼합된 변화 경향을 보이고 있다. 이것은 상대적으로 두꺼운 크래쉬 박스가 적용 되었을 경우 범퍼 백빔의 재질에 따라 최대하중의 변화가 다른 특성을 보일 수 있다고 생각된다.
Fig. 5(b)에 크래쉬 박스의 두께 변화에 따른 영향을 정리한 결과이다. 고정변수가 두께 2 mm의 범퍼 백빔인 경우 크래쉬 박스의 두께가 두꺼워 짐에 따라 Case A와 D의 최대하중은 감소하였다. 그리고 범퍼 백빔 7021 경우보다 6082 경우에 두께가 변하더라도 최대하중은 약 10 kN 높게 나타나는 결과를 보였다. 상대적으로 범퍼 백빔의 두께가 얇은 경우 범퍼 백빔의 대변형이 많이 이루어져서 최대하중이 높게 나타나는 것으로 생각된다.
고정변수가 두께 3 mm의 범퍼 백빔인 경우 크래쉬 박스의 두께가 두꺼워 짐에 따라 최대하중 값은 증가하지만 그 증가량은 감소하면서 약 105 kN 부근으로 집중되는 양상을 보였다. 크래쉬 박스 두께가 일정 두께 이상이면 최대하중은 일정수준의 하중부근으로 집중되며 재질의 영향도 낮아지는 것을 알 수 있다. 고정변수가 두께 4 mm의 범퍼 백빔인 경우도 두께 3 mm처럼 최대하중 변화 양상이 유사함을 알 수 있다.
Model 1의 범퍼 백빔의 두께는 3 ~ 4 mm 가 접합하다고 할 수 있다. 그리고 크래쉬 박스 두께 역시 3 ~ 4 mm 가 적합한 범위라고 할 수 있다. 다만 적용 차량의 프론트 사이드 멤버의 최대하중 보다는 낮은 하중이 적용 될 수 있도록 본 논문의 결과를 참조하여 선정할 수 있다.
3.2 Model 2의 충돌특성
Fig. 6(a)에 범퍼 백빔의 두께 변화에 따른 영향을 정리하여 나타내었다. 고정변수가 두께 2 mm의 크래쉬 박스인 경우 같은 두께의 범퍼 백빔이 적용되었을 때 최대하중의 분포범위가 약 30 kN으로 넓게 분포하였는데, 이는 범퍼 백빔의 두께가 상대적으로 얇은 영향인 것으로 생각된다. 그러나 범퍼 백빔 3, 4 mm에서는 최대하중이 81 kN 부근에서 비슷한 크기를 유지하는 것으로 나타났다.
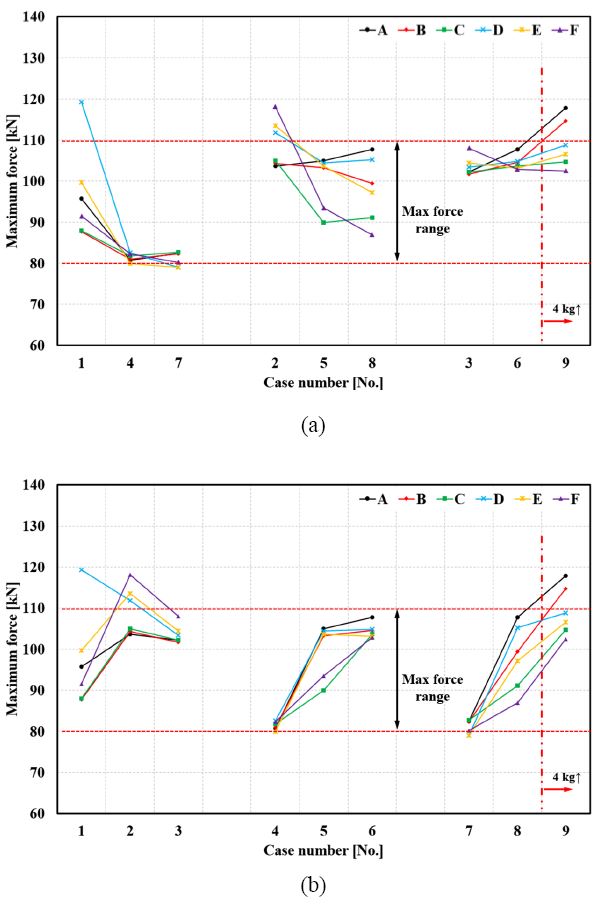
Results of model 2 from FE analysis: (a) Effect of bumper back beam thickness, (b) Effect of crash box thickness
고정변수가 두께 3 mm의 크래쉬 박스인 경우 No.5의 Case A, B, D, E는 최대하중이 104 kN 부근에 집중되었다. 다만, 크래쉬 박스 재질이 6060 계열인 Case C, F는 그 보다 낮은 90 kN ~ 93 kN의 최대하중을 나타내었다. 그리고 No.8에서는 크래쉬 박스의 강도가 높을수록 최대하중도 높아지고, 범퍼 백빔의 재질이 다르더라도 크래쉬 박스 재질별로 짝을 이루어 최대하중이 유사하게 분포하는 양상을 보였다.
고정변수가 두께 4 mm의 크래쉬 박스인 경우 No.3, 6은 최대하중이 10 %이내(102 kN ~ 109 kN)에서 유사한 크기를 보이는 것으로 확인되었다.
Fig. 6(b)에 크래쉬 박스의 두께 변화에 따른 영향을 정리한 결과이다. 고정변수가 두께 2 mm의 범퍼 백빔인 경우 크래쉬 박스가 두꺼워짐에 따라 최대 하중의 변화 양상이 Model 1과 유사하는 양상을 보였다. 다만 Case D만이 크래쉬 박스 두께변화에 따라 최대하중이 낮아지는 결과를 보였다.
고정변수가 두께 3 mm의 범퍼 백빔인 경우 No.4에서는 82 kN을 기준으로 3 kN 범위 내에서 최대하중 값이 모두 존재하였다. 그리고 크래쉬 박스 두께가 증가함에 따라 최대하중이 증가하지만, 증가 양상이 6060과 나머지 재질이 차이를 보이면서 증가하였다.
고정변수가 두께 4 mm의 범퍼 백빔인 경우 No.7은 No.4와 비슷하게 82 kN 부근에서 4 kN 범위 내에 최대하중이 모두 존재하였다.
Model 2의 경우 적합한 범퍼 백빔의 두께는 2 mm ~ 4 mm 모두 적합하다고 판단된다. 다만 크래쉬 박스의 두께는 Model 1처럼 적용하려는 차량의 최대하중 범위에 따라서 적절한 두께가 선정되어야 할 것으로 생각된다.
충돌특성 분석결과 Model 1, 2 모두 두께 조합에 따른 최대하중 변화 양상은 유사하게 나타났다. 다만 최대하중의 차이가 나타나는 조합도 있지만 이것은 예외적인 부분이라고 할 수 있다. 서로 다른 두께 조합에서 유사한 최대하중 결과들이 나타나고, 재질별 특성을 확인할 수 있기에, 본 결과를 토대로 차량 상황에 맞는 적절한 알루미늄 범퍼 시스템 설계의 DB자료로 활용 할 수 있다고 생각된다.
3.3 단위 질량당 흡수에너지 특성변화
Model 1, 2의 단위 질량당 흡수에너지의 변화는 Fig. 7에 정리하여 나타내었다. 단위 질량당 흡수에너지는 전체적인 모델 대부분이 질량이 증가하면서 흡수에너지는 낮아지는 결과를 보였다. 범퍼 백빔 두께를 기준으로 두께가 두꺼워 짐에 따라 No.1 ~ 3에서는 뚜렷하게 나타난 범퍼 백빔 재질별 단위 질량당 흡수 에너지의 차이가 No.4 ~ 6, No. 7과 8로 두께가 두꺼워지면서 그 경계는 사라지고 최대하중의 분포가 조밀해졌다. 그 특징은 Model 2 보다 Model 1에서 조금 더 뚜렷하게 나타났다. 그래도 Model 1과 Model 2를 비교하였을 때 무게가 무거운 Model 2 보다는 Model 1이 단위 질량당 흡수에너지가 높기 때문에 범퍼 시스템 선정에 유리하다고 생각된다.
4. 결 론
본 논문에서는 알루미늄 범퍼 시스템 초기 설계단계에서 안전성 확보를 위해 재질·두께별 평가를 FMVSS part 581의 평가방법에 따라 유한요소법으로 충돌해석을 진행하였고 다음과 같은 결론을 얻을 수 있었다.
- 1) Model 1의 경우 범퍼 백빔 두께는 3 mm ~ 4 mm가 접합하다고 할 수 있다. 그리고 Model 2는 범퍼 백빔 두께가 2 mm ~ 4 mm 모두 적합하다고 생각된다. 다만 크래쉬 박스의 두께는 Model 1, 2 모두 사이드 멤버의 최대하중 범위에 따라서 적절한 두께가 선정되어야 할 것으로 판단된다.
- 2) 충돌특성 분석결과 Model 1, 2 모두 두께 조합에 따른 최대하중 변화 양상은 유사하게 나타났다. 서로 다른 두께 조합에서 유사한 최대하중 결과들이 나타나고, 재질별 특성을 확인할 수 있다.
- 3) 본 연구결과를 토대로 차량 상황에 맞는 적절한 알루미늄 범퍼 시스템 설계의 DB자료로 활용 할 수 있다고 생각된다. 경량화와 고강도의 부재가 적용된 범퍼 시스템 설계가 가능할 것으로 판단된다.
Acknowledgments
본 연구는 산업통상자원부와 한국산업기술진흥원이 지원하는 경제협력권산업육성사업으로 수행된 연구결과입니다(R0004151).
References
- S. B. Kim, K. H. Lee, H. Huh, J. S. Yoo, and M. Y. Lee, “Crashworthiness Evaluation of Aluminum Crash Box for an Auto-body, KSAE Fall Conference Proceedings, p1106-1111, (2006).
-
C. J. Lee, S. B. Lee, D. C. Ko, and B. M. Kim, “Effect of Bead Shape in Aluminum Crash Box for Effective Impact Energy Absorption Under Low-Velocity Impact Condition, Transactions of KSME(A), 36(10), p1155-1162, (2012).
[https://doi.org/10.3795/KSME-A.2012.36.10.1155]
-
J. S. Yoo, S. B. Kim, M. Y. Lee, and H. Huh, “Development of Al Crash Box for High Crashworthiness Enhancement, Transactions of Materials Processing, 17(3), p182-188, (2008).
[https://doi.org/10.5228/KSPP.2008.17.3.182]
-
M. Langseth, and O. S. Hopperstad, “Local Buckling of Square Thin-walled Aluminium Extrusions, Thin-walled Structures, 27(1), p117-126, (1997).
[https://doi.org/10.1016/0263-8231(96)00007-9]
- I. J. Ahn, H. W. Bai, and M. S. Lee, “Bumper System Optimization for EU and NA RCAR, KSAE Annual Conference Proceedings, p2556-2559, (2010).
- S. J. Lee, J. S. Park, D. H. Koo, and B. H. Jung, “The Development of Material Technology Applied to Bumper Beam, Transactions of KSAE, 10(4), p206-215, (2002).
- S. T. Won, and K. J. Kim, “Effect of Structural Variables on Automotive Body Bumper Impact Beam, KSPE Conference Proceedings, p521-522, (2007).
-
K. J. Kim, and S. T. Won, “Effect of Structural Variables on Automotive Body Bumper Impact Beam, Int. J. Automotive Technology, 9(6), p713-717, (2008).
[https://doi.org/10.1007/s12239-008-0084-8]
- S. W. Lee, H. W. Bai, and J. H. Yim, “A Study for RCAR Bumper Over/Under-ride Impact of Passenger Vehicles, KSAE Fall Conference Proceedings, p1458-1465, (2007).
- D. P. Kang, W. S. Lee, M. Y. Lee, and D. U. Kim, “Development of Lightweight & High Strength Bumper Beam of 7XXX Series Aluminum Alloy, The Korean Society for Technology of Plasticity Conference Proceedings, p30-33, (2005).
- K. H. Lee, and W. S. Joo, “Optimum Design of Automobile Front Bumper Using Design of Experiments, KSAE Fall Conference Proceedings, p542-547, (2002).
- I. S. Park, S. J. Heo, and T. Y. Chung, “Damageability, Repairability and Safety of Vehicles at Low Speed 40 % Offset Crash Test, Transactions of KSAE, 7(9), p203-211, (1999).
-
J. W. Kim, I. S. Park, and C. S. Lee, “A Study on the Improvement of a Damageability and Repairability by Improving Mounting Structure of a Bumper for Passenger Cars, Transactions of KSME(A), 34(1), p1-9, (2010).
[https://doi.org/10.3795/KSME-A.2010.34.1.1]
- FMVSS part 581, Vehicle Bumper Standard.
- W. Rosenbluth, and L. Hicks, “Evaluating Lowspeed Rear-end Impact Severity and Resultant Occupant Stress Parameters, ASTM International, 39(6), p1393-1424, (1994).
- I. Scheider, W. Brocks, and A. Cornec, “Proce dure for the Determination of True Stress- Strain Curves From Tensile Tests With Rec tangular Cross-section Specimens, J. Eng. Mater. Technol, Transactions of the ASME, 126(1), p70-76, (2004).
-
M. Kamaya, and M. Kawakubo, “A Procedure for Determining the True Stress-strain Curve over a Large Range of Strains Using Digital Image Correlation and Finite Element Analysis, Mechanics of Materials, 43(5), p243-253, (2011).
[https://doi.org/10.1016/j.mechmat.2011.02.007]
-
N. Tanlak, F. O. Sonmez, and M. Senaltun, “Shape Optimization of Bumper Beams under High-velocity Impact Loads, Engineering Structures, 95, p49-60, (2015).
[https://doi.org/10.1016/j.engstruct.2015.03.046]
-
D. H. Kim, H. G. Kim, and H. S. Kim, “Design Optimization and Manufacture of Hybrid Glass/ Carbon Fiber Reinforced Composite Bumper Beam for Automobile Vehicle, Composite Structures, 131(1), p742-752, (2015).
[https://doi.org/10.1016/j.compstruct.2015.06.028]