
핀부트 홀 직경 축소와 브레이크 래틀노이즈의 상관 관계 분석
Copyright Ⓒ 2023 KSAE / 215-03
This is an Open-Access article distributed under the terms of the Creative Commons Attribution Non-Commercial License(http://creativecommons.org/licenses/by-nc/3.0) which permits unrestricted non-commercial use, distribution, and reproduction in any medium provided the original work is properly cited.
Abstract
Caliper rattle noise is mostly caused by vibrations applied to the wheel when the vehicle drives on an unpaved road or a paved road with continuous steps. This can be attributed to loosely fitted components, such as rubber or spring in the caliper. In this paper, we studied the relationship between reducing the size of the pin-boot hole and the brake rattle noise of a two-piston floating caliper. After analyzing the sound sources of the rattle noise, we controlled the tightening force of the pin-boot to improve rattle noise characteristics. This was achieved by reducing the diameter of the pin-boot seating hole in the torque member. The results of our study showed a high correlation between the reduction of the pin-boot seating hole and improvement in rattle noise, as the caliper body and the torque member can vibrate under a more integrated condition. However, as an adverse effect, caliper sliding resistance may increase, leading to high drag and accelerating pad wear. Thus, we are proposing an optimal improvement design range after considering the trade-off relationship between caliper rattle noise and sliding resistance.
Keywords:
Caliper, Brake rattle nosie, Pin-boot hole size, Rubber tightening force, Caliper sliding resistance키워드:
캘리퍼, 브레이크 래틀노이즈, 핀부트 홀 직경, 고무 긴박력, 캘리퍼 접동저항1. 서 론
캘리퍼는 가압된 브레이크 액으로 1개 혹은 다수의 피스톤을 전진시켜 패드와 디스크 사이 마찰을 발생시키고, 차량을 제동하는 장치이다. 작동 방식에 따라 플로팅 캘리퍼와 대향형 캘리퍼로 나뉘며, 피스톤이 차량 내측 방향에만 위치하고 있는 플로팅 캘리퍼가 일반적으로 적용되고 있다. 플로팅 캘리퍼는 캘리퍼바디, 토크멤버, 패드, 가이드핀 등의 구성 요소들로 이루어져 있으며 독립 거동이 이루어지는 단품 사이에서 충돌 혹은 공진 특성이 발생할 수 있다. 근래에 전기차 보급이 본격적으로 이루어지면서 파워트레인 이외의 요소에서 발생할 수 있는 노이즈 저감에 대한 요구치가 높아지고 있고, 캘리퍼를 포함한 제동 부품 부문에서도 다양한 노이즈 강건 화 설계가 적용되고 있다.
구동계를 제외한 차량 구성품들에서 래틀노이즈는 대부분 차량이 비포장 도로나 연속적인 단차로 이루어진 포장 도로를 주행할 때 휠에서 가해지는 진동에 의해 발생한다. 고무 재질로 느슨하게 고정되어 있는 부위나 특정 갭만큼 이격되어 있는 금속 단품 사이에서 주로 발생하며 차체, 윈도우, 캐빈 등 대부분의 차량 구성요소에서 래틀노이즈가 발생할 여지가 있다.1-3)
플로팅 캘리퍼는 진퇴운동을 하는 제품 특성으로 인해 고무나 스프링을 활용한 고정 구조가 적용되어 있다. 이로 인해 가진 진동수나 스트로크가 증가하게 되면 부품들 간의 충돌이 발생하여 래틀노이즈가 발생할 수 있다. 특히 전륜에 장착되는 플로팅 캘리퍼는 운전자와의 거리가 가깝고, 더 큰 제동력이 요구되어 중량이 무겁기 때문에 래틀노이즈 문제에 더욱 민감하다.
캘리퍼 래틀노이즈와 관련된 선행 논문들은 주로 노이즈 분석과 관련된 연구를 진행하였다.4) Hamdi 등5)은 캘리퍼 패드 래틀노이즈 평가를 위해 Band-pass filter을 적용한 가속도 측정 결과로 노이즈 수준을 예측할 수 있는 방법을 제시하였다. Liang 등6)은 실험실 환경에서 진행한 래틀노이즈 평가 결과에 실차 주행 환경을 반영할 수 있는 Weighted factor에 대한 연구를 진행하였고, Lee 등7)은 알고리즘을 활용한 분석을 통해 Squeak/ Rattle 노이즈를 구분할 수 있는 방법을 제시하였다. 이렇듯 많은 선행 연구들이 래틀노이즈 분석과 관련된 내용들을 주로 다루고 있기에 근본적인 노이즈 저감 방법에 대한 연구가 필요하다.8)
일반적으로 캘리퍼의 중량이 증대될수록 래틀노이즈에 취약해지는 경향이 있다. 본 연구에서는 캘리퍼 중량이 8.8 kg으로 상대적으로 무거운 2-piston 플로팅 캘리퍼의 래틀노이즈 발생 인자에 대한 분석을 진행하고, 개선 인자에 대해 사양 별로 평가하였다. 가진기를 통해 캘리퍼를 상하 방향으로 가진하고, 점진적으로 가진 주파수를 증가시켰다. 노이즈 측정 결과를 통해 래틀노이즈가 발생하는 주요 주파수 및 그 특성을 확인하고, 노이즈 발생 요인에 대한 비교 분석을 진행하였다. 우리는 래틀노이즈 개선 인자로 가이드핀 부트의 긴박력을 증대하는 방안을 제안하였다. 토크멤버 내에 핀부트가 안착되는 홀 내경을 축소하여 고무 재질의 핀부트 변형량을 증대함으로써 가이드핀을 구속하는 긴박력을 높일 수 있다. 이러한 방안은 캘리퍼 접동 저항이 증대되어 패드 마모를 가속화하고, 드래그에 영향을 줄 수 있기 때문에 개선안 적용에 따른 상관 관계를 분석하여 래틀노이즈 개선의 방향성을 제시하고자 한다.
2. 캘리퍼 래틀노이즈 분석
2.1 캘리퍼 래틀노이즈 측정 방법
무향실 환경에서 캘리퍼 이외의 외부 소음 영향을 최소화한 상태에서 래틀노이즈 평가를 진행하였다. Fig. 1(a) 하단에 위치하고 있는 가진기는 MB dynamics의 MB vibration test bench이다. 3 mm 상하 방향 스트로크로 초기 5 Hz를 유지하다가 30초 동안 5 Hz에서 20 Hz으로 가진 주파수를 점진적으로 증대하였다. 가진 장비 특성상 상하 방향 스트로크가 과도하게 증대되면, 장비 작동 노이즈에 영향을 주게 된다. 우리는 가진 스트로크에 따른 장비 작동 노이즈를 분석하여 가진기 노이즈가 용인할 만한 수준이면서 진동 스트로크가 최대가 될 수 있는 조건을 파악하였고, 3 mm 조건을 선정하였다. 또한 해당 스트로크에서 20 Hz를 넘어서는 주파수로 진동할 경우에도 가진기 노이즈가 크게 증대되었기 때문에 최대 진동 주파수를 20 Hz까지로 설정하였다. 이러한 평가 조건에서 캘리퍼는 최대 4.1 g의 가속도로 진동하였으며, 이를 통해 가진기 노이즈를 억제한 상태에서 도달할 수 있는 최대 가속도 수준을 파악할 수 있었다.
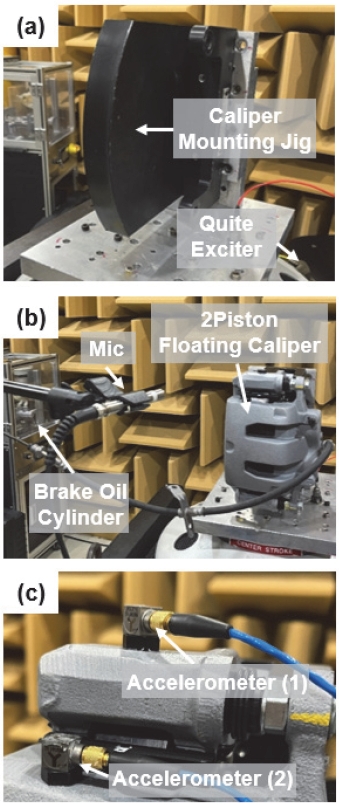
Caliper rattle noise test conditions. (a) caliper mounting jig on quite exciter (b) caliper and microphone setting condition (c) accelerometers installed on side flat area of caliper body and torque member
캘리퍼가 장착되는 지그는 지면과 평행하고, 가진기의 진동 방향과는 수직을 이루도록 장착되었으며 30 mm 두께 상당의 디스크 형상을 포함하여 실제 차량 장착 조건을 모사하였다. 캘리퍼의 장착 방향은 차량 전륜 오른쪽 방향으로 통일하였으며, 높이는 캘리퍼 측면부가 지그의 하단부에 간섭되지 않도록 충분히 높게 설정하였다. 캘리퍼에는 노이즈 저감 목적으로 다양한 위치에 그리스가 적용되어 있다. 그리스의 도포량에 따라 노이즈 평가 결과가 달라질 수 있기 때문에 본 연구에서는 캘리퍼 전체 부위에 그리스를 도포하지 않은 상태에서 평가하였다.
Fig. 1(b)와 같이 캘리퍼를 지그에 장착하고, 브레이크 실린더와 연결하여 브레이크 액을 캘리퍼 내에 주입하였다. 5 bar 상당의 가압 및 해제하는 과정을 10회 반복하여 패드와 피스톤을 디스크 방향으로 전진시켰고, 평가 사양이 변경할 때마다 동일하게 진행하였다. 평가 사양마다 피스톤과 디스크 사이 간극을 일정하게 유지하기 위함이다.
래틀노이즈는 캘리퍼에서 15 cm 떨어진 거리에 설치되어 있는 Type 4189-A-021 마이크로폰을 통해 측정하였다. 노이즈 비교 평가에 활용한 주파수는 300 Hz ~ 15 kHz 대역으로 그 이외의 주파수 대역은 Cut-off 하였다. 추가적으로 캘리퍼에 가해지는 가속도를 측정하기 위해 가속도계를 부착하였다. Fig. 1(c)와 같이 캘리퍼바디와 토크멤버 측면에 각각 하나씩 부착하였으며, 수평한 면을 선정하여 가속도계에서 측정되는 진동 방향이 가진기의 진동 방향과 일치하도록 하였다. 가속도계는 Dytran Instruments, Inc의 Single axis IEPE 3056d2으로 최대 50 g까지 계측할 수 있다. 평가 장비와 관련된 정보는 Table 1에 제시되어 있다.
캘리퍼 외에 다른 평가 장비에서 유입되는 노이즈 수준을 확인하고자 지그만 장착한 상태에서 가진기를 작동하여 노이즈 측정을 하였다. 래틀노이즈 평가 조건은 5 Hz에서 30초 동안 점진적으로 20 Hz까지 가진하는 조건이므로 비교군이 되는 지그 가진 조건 또한 동일하게 평가하였다. Fig. 2(a)에 제시된 노이즈 평가 결과를 통해 캘리퍼 이외의 요인으로 유입되는 노이즈는 매우 낮은 수준임을 확인할 수 있다. 가진 장비에 의해 간헐적으로 발생하는 노이즈 띠가 측정되었으나, 앞으로 분석할 캘리퍼 래틀노이즈 결과에 큰 영향을 주지 않는 수준으로 판단되었다. Fig. 2(b)에는 시간에 따른 가진 진동수가 제시되어 있다. 해당 진동 조건을 고정해 놓고, 다양한 사양의 캘리퍼 샘플들을 장착하여 래틀노이즈 비교 평가를 진행하였다.
2.2 캘리퍼 래틀노이즈 발생 요인 분석
캘리퍼에 장착되는 마찰재는 Low-steel 재질에 신품 기준 10.5 mm 두께이며, 패드 마모 상태에 따른 영향을 확인하고자 신품 패드와 2.0 mm 두께의 마모 패드를 준비하여 사양 별로 패드 마모 상태에 따른 비교 평가를 진행하였다. 마모 패드 장착 상태에서는 신품 패드 대비 피스톤이 캘리퍼바디에서 17 mm 만큼 전진한 상태이며, 캘리퍼바디는 고정부인 토크멤버에서 8.5 mm 만큼 차량 내측으로 이동한 상태이다.
플로팅 캘리퍼에서 래틀노이즈가 발생할 수 있는 요인들을 정리해보면, Fig. 3에 표시해 놓은 구성요소들 사이들로 추정할 수 있다. 첫 번째로는 가이드핀과 토크멤버 핀 홀 사이, 두 번째로는 피스톤과 캘리퍼바디 실린더부 사이. 그리고 마지막으로 패드와 토크멤버 습동부 사이이다. 플로팅 캘리퍼의 구조적인 특성상 진퇴운동이 발생하는 부위들로 진동에 대한 강건화를 위해 최소 갭을 유지하는 방향으로 설계되어 있다. 또한 각각 피스톤 씰, 가이드핀 부쉬와 부트, 패드라이너 러버 코팅을 적용함으로써 댐핑 특성을 활용한 고정 구조가 적용되어 있다. 그러나 캘리퍼에 높은 진동수의 가진이 가해져서 진동 방향으로의 가속도가 증가하게 되면, 댐핑을 활용한 구속 조건을 이겨내고 금속 재질의 단품들 사이에서 충돌이 발생할 수 있다. 우리는 기본 사양의 2-piston 캘리퍼에서 래틀노이즈가 발생하는 원인을 파악하고자 일부 단품들을 제거하여 평가하면서 래틀노이즈 영향을 분석하였다.
Fig. 4(a)는 2-piston 캘리퍼에서 내외측 패드를 제외하고 가진 시켰을 때의 래틀노이즈 측정 결과이다. 가진 20초 부근에서 노이즈가 발생하기 시작하였으며, 가진 진동수 20 Hz에 근접하는 30초 부근에서는 빨간 점선으로 표시된 35 dB(A) 이상의 비교적 높은 노이즈가 5 kHz 이하의 주파수 대역에서 전반적으로 발생하였다. 이와 대조적으로 토크멤버와 신품 패드만 장착한 샘플의 평가 결과인 Fig. 4(b)에서는 래틀노이즈가 크게 발생하지 않았다. 최대 가진 진동수에 근접하는 30초 부근에서 노이즈 띠가 미세하게 형성되어 있으나, 35 dB(A) 이상의 노이즈 대역은 나타나지 않았다. 이를 통해 패드와 토크멤버 습동부 사이는 래틀노이즈 발생에 큰 영향이 없음을 확인할 수 있었다.
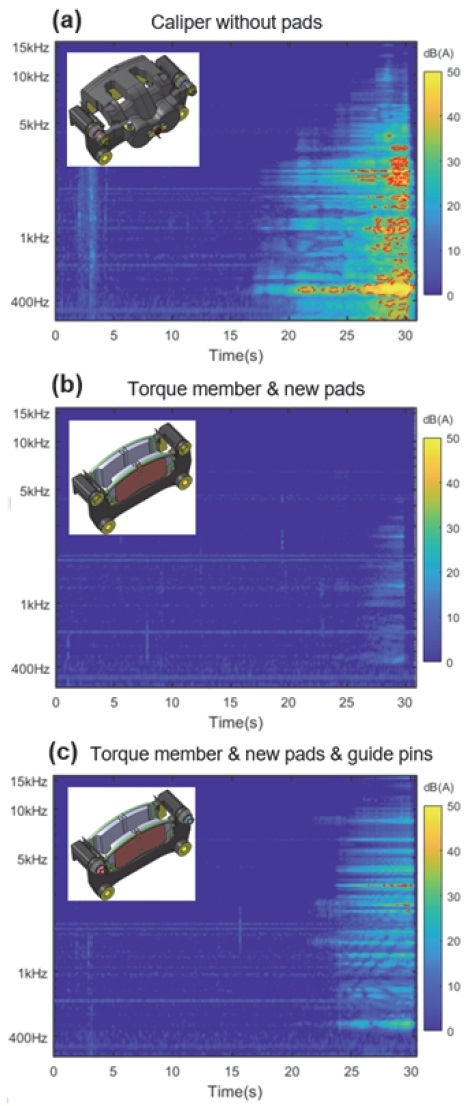
Analysis of caliper rattle noise risk interfaces (a) caliper without pad (b) torque member and new pads mounted condition (c) torque member, new pads and guide pins mounted condition
Fig. 4(c)는 Fig. 4(b) 사양에서 가이드핀들을 추가하여 평가하였을 때의 결과이다. 지그 장착 조건에서 상단에는 EPDM 재질의 부쉬가 포함되어 있는 가이드핀이 추가되었으며, 하단에는 부쉬가 포함되지 않은 가이드핀이 추가되었다. 가이드핀과 토크멤버 핀홀 사이의 래틀노이즈 발생 인자가 추가됨에 따라 노이즈 띠의 발생 시점이 앞당겨지고 노이즈 수준이 증대되었으며, 가이드핀에 추가적으로 무게가 가해지게 된다면 그 경향은 더욱 두드러질 것이라 추정할 수 있다.
Fig. 5(a)와 같이 캘리퍼바디가 체결되어 가이드핀에 가해지는 무게가 증가함에 따라 래틀노이즈의 발생 시점이 앞당겨지고, 35 dB(A) 이상의 노이즈가 가진 30초 부근에서 집중적으로 발생하였다. 측정된 래틀노이즈의 주요 주파수 대역이 Fig. 4(c)와 유사하여 공진 모드에 의한 영향보다는 가이드로드에 지지되는 중량이 증대되어 래틀노이즈에 취약해진 것으로 판단된다. Fig. 5(b)에 나타나는 것처럼 마모 패드 장착 조건에서는 신품 패드 조건에 비해 래틀노이즈가 저감되면서 주요 주파수 대역이 축소되었는데, 400 ~ 800 Hz 대역과 2 ~ 3.5 kHz 대역이다.
Fig. 6에 제시된 가속도계 측정 결과를 통해 가이드핀 부근에서 래틀노이즈가 발생하는 원인에 대한 분석을 진행하였다. Accelerometer 1은 토크멤버 측면에 부착한 가속도계이고, Accelerometer 2는 캘리퍼바디 측면에 부착한 가속도계이다. 진동 주파수 20 Hz에 근접하는 29.9 ~ 30.0 s 사이의 가속도 측정 결과를 신품패드와 마모패드 장착 상태에서 각각 비교하였다.
동일 시점에서 캘리퍼바디와 토크멤버의 가속도 차이가 커진다는 것은 가이드핀을 매개로 연결되어 있는 두 단품이 분리되어 진동하는 경향이 커지는 것을 의미한다. 그 차이가 클수록 가이드핀 부트와 부쉬의 긴박력에 의해 고정되는 것을 이겨내고 상호간에 분리되어 진동함으로써 가이드핀과 토크멤버 핀홀 사이에서 금속성 충돌 소음이 발생할 수 있다. 신품 패드를 장착하였을 때, 가진 29.0 ~ 30.0 s 동안 캘리퍼바디와 토크멤버의 평균 가속도 차이는 3.57 m/s2이었다. 반면, 마모 패드 장착 시에는 1.75 m/s2으로 신품 패드 대비 분리 진동 경향이 줄어들었고 캘리퍼 래틀노이즈도 이와 대응되는 결과를 보였다.
Fig. 7은 가속도 측정값에 샘플링 주파수 44.1 kHz, 50 Hz 하이패스 필터를 적용한 결과이다. 하이패스 필터를 통해 가진기에 의해 유발되는 가속도 성분을 제거하고, 캘리퍼바디와 토크멤버가 분리 진동되는 경향을 보다 명확히 파악하고자 하였다. 해당 시점에서의 진동 주기인 0.05 s 간격으로 분리 진동되는 패턴이 확인되며, 앞서 분석한 내용과 동일하게 마모패드 장착 조건 대비 신품패드 장착 조건에서 뚜렷한 가속도 값 차이가 발생하여 패드 장착 조건에 따라 래틀노이즈 수준이 차이나는 원인을 파악할 수 있었다.
패드 장착 조건에 따른 캘리퍼 단면도는 Fig. 8에 제시되어 있다. 토크멤버는 지그에 고정되어 있으며, 장착되는 패드의 마모량에 비례하여 가이드핀과 캘리퍼바디는 차량 내측으로 이동한다. 이에 따라 가이드핀 부트와 가이드핀 부쉬 사이의 거리가 패드 마모량인 8.5 mm 만큼 좁혀지게 된다.
우리는 래틀노이즈 발생의 원인이 되는 가이드핀과 토크멤버 홀 사이를 개선하기 위해 토크멤버의 부트 안착부 치수를 축소하는 방안을 적용하였다. 부트 안착부 직경이 작아질수록 핀부트가 내측으로 탄성 변형되어 가이드핀을 조이는 긴박력이 증대되며, 이를 통해 높은 가진 진동수에서도 캘리퍼바디와 토크멤버의 단일화된 진동 경향을 확보할 수 있다. 또한 토크멤버 주물품의 가공 사양을 변경하는 방안이기에 금형과 제작 공정을 유지한 채로 적용이 가능하다. 캘리퍼 개발 과정에서 래틀노이즈 이슈가 발생하였을 때 즉각적으로 적용하기에 용이한 방안이다. 앞서 분석한 기본 사양의 부트 안착부 치수를 ØA라고 지정하고, 점차적으로 직경을 축소한 ØB, ØC, ØD 사양을 제작하였다. 상세 도면 치수는 기술 보안 사항이므로 알파벳 레터링으로 표기하였으며, 제작된 샘플들의 홀 치수는 모두 ±Ø0.02의 공차 범위 내에 포함되었다.
3. 개선 사양 설계 및 평가
3.1 개선 사양 별 래틀노이즈 평가
신품 패드와 마모 패드 장착 조건에서 부트 안착부 직경에 따른 래틀노이즈 측정 결과는 Fig. 10과 Fig. 11에 각각 정리되어 있다. 공통적으로 400 ~ 800 Hz 대역과 2.0 ~ 3.5 kHz 대역에서 래틀노이즈 발생이 집중되고 있고, 35 dB(A) 이상의 노이즈도 해당 대역에서 주로 나타나고 있다. 부트 안착부 홀 치수가 축소됨에 따라 기본 사양(ØA)에서는 가진 20초 부근에서 발생하기 시작하는 래틀노이즈의 발생 시점이 지연되는 경향을 보이며, ØC 이하의 사양으로 제작되는 경우에는 신품 패드와 마모 패드 모두 35 dB(A) 이상의 노이즈 발생 대역이 크게 줄어들어 500 Hz 이하의 일부 대역을 제외하고는 나타나지 않았다.
이러한 래틀노이즈 개선 경향은 각 사양 별로 상단에 표시한 가속도 차이를 통해 설명할 수 있다. 해당 값은 앞서 언급했듯이 20 Hz 진동수에 근접하는 가진 29.0 ~ 30.0 s 사이에서 캘리퍼바디와 토크멤버 가속도 차이의 평균이다. 부트 안착부 치수가 축소될수록 단품 간의 가속도 차이가 줄어드는 경향을 확인할 수 있는데, 부트 긴박력이 증대되어 캘리퍼의 단일화된 진동 특성이 강화됨에 따라 가이드핀과 토크멤버 홀 사이에서 발생하는 래틀노이즈가 개선되는 것이다.
기본 사양(ØA)에서는 가이드핀 부트의 긴박력이 상대적으로 부족하여 가이드핀 위치에 따른 영향이 주요하게 나타났다. 가이드핀 위치가 8.5 mm 만큼 차이나는 신품 패드와 마모 패드 장착 상태에서 캘리퍼바디와 토크멤버의 가속도 차이는 각각 3.57 m/s2, 1.75 m/s2으로 패드가 마모됨에 따라 1.82 m/s2 만큼 차이가 줄어들었다. 반면, 부트 안착부 직경이 축소됨에 따라 마모 상태에 따른 가속도 차이는 ØB, ØC, ØD 사양에서 각각 1.32 m/s2, 0.40 m/s2, 0.27 m/s2으로 점차 줄어드는 추세를 보였다. 부트 안착부 직경이 줄어들수록 가이드핀과 캘리퍼바디의 위치 변화에 따른 영향이 줄어들고, 가이드핀 부트 긴박력의 영향이 래틀노이즈 측면에서 주요해지는 것이다. 이러한 결과를 통해 래틀노이즈 개선과 더불어 패드의 마모 상태에 따른 영향성이 축소된 캘리퍼 개발이 가능함을 확인할 수 있었다.
3.2 래틀노이즈 분석
Fig. 12에는 가진 29.0 ~ 30.0 s 시점에서의 1/3 Octave band diagram이 제시되어 있다. 부트 안착부 직경이 축소될수록 캘리퍼바디와 토크멤버의 가속도 차이가 줄어드는 것에 대응되어 전반적인 주파수 대역에서 래틀노이즈 저감이 확인되며, 특히 신품 패드 사양의 경우 2 kHz 이후 대역의 래틀노이즈 저감이 두드러진다. 마모 패드 사양에서는 기본 사양 대비 오히려 래틀노이즈가 증대되는 대역이 있는데, ØB와 ØC 사양에서 5 kHz 이후의 대역이다.
Table 2에는 Sound loudness와 Sharpness 값이 제시되어 있다.9) 기본 사양(ØA)에서는 신품 패드와 마모 패드 장착 상태에서 각각 6.60 sone, 4.50 sone인 Loudness값이 점차 감소하여 ØD 사양에서는 2.20 sone, 2.42 sone으로 줄어들었다. 패드 마모 상태에 따른 Loudness 차이가 점차 줄어들면서 ØD 사양에서는 신품패드와 마모패드 장착 결과가 유사한 수준으로 측정되었는데, 이는 앞서 서술했듯이 가이드핀 부트의 긴박력이 증대되면서 패드 마모에 따른 차이가 줄어든 것이다. Sharpness 값과 관련해서는 신품 패드 장착 상태일 때, 2 kHz 이후의 대역에서 부트 안착부 축소에 따라 래틀노이즈가 저감되기 때문에 기본 사양 0.95 acum에서 ØD 사양 0.62 acum으로 저감 추세를 보였다. 반면, 마모 패드 장착 상태에서는 5 kHz 이후 대역에서 오히려 기본 사양 대비 래틀노이즈가 증대되는 사양들이 있어서 Sharpness 저감 폭이 신품 패드 대비 적고, ØC 사양에서는 오히려 기본 사양 대비 sharpness 값이 증가하였다.
3.3 캘리퍼 접동저항 분석
핀부트의 긴박력이 증대되면, 가이드핀의 진퇴운동에 대한 마찰력이 증대되어 드래그와 패드 마모 특성에 불리하게 작용할 수 있다. 이에 대한 영향을 검토하기 위해 우리는 다음과 같은 조건에서 캘리퍼 접동 저항을 평가하였다. 지그에 캘리퍼 샘플을 장착하고, 하중 센서와 스트로크 센서가 부착된 디스크를 삽입하였다. 1.8 ~ 2.0 mm/s의 속도로 디스크를 차량 내측 방향으로 이동시키며 하중을 확인하고, 그 이후 디스크를 반대 방향으로 이동시키며 하중을 확인하였다. 총 3회 측정한 캘리퍼 평균 접동 저항은 Fig. 13에 정리되어 있다.
기본 사양(ØA)의 캘리퍼 접동 저항은 9.38 kgf이고, 부트 안착부 치수가 ØB, ØC, ØD으로 축소될수록 저항 값이 10.88 kgf, 12.19 kgf, 15.27 kgf으로 점진적으로 증대되는 경향을 보였다. 캘리퍼 접동 저항 증대 폭은 기본 사양 대비 15.9 %, 30.0 %, 62.8 % 증대되어 특히 ØD 사양에서의 급격한 접동 저항 증대가 발생하였다.
이러한 접동 저항 측정 결과를 Loudness 값과 함께 상관관계 분석에 활용하여 최적의 래틀노이즈 개선 범위를 도출할 수 있었다. 부트 안착부 치수를 축소할수록 래틀노이즈는 개선되고, 접동 저항이 불리해지는 상관관계가 ØD 사양부터는 경향에 변화가 생기는 것이다. 기본 사양 대비 ØC 사양에서는 Loudness 값이 -54.7 %(신품 패드), -50.7 %(마모 패드) 저감 되었지만, ØD 사양에서는 -66.7 %(신품 패드), -46.2 %(마모 패드) 저감 되어 래틀노이즈 수준은 크게 차이 나지 않았다. 반면, 캘리퍼 접동 저항은 ØD 사양에서 크게 증대되어 드래그와 패드 마모에 불리하게 작용할 수 있다. 이러한 결과를 종합하여 우리는 토크멤버 가이드핀 부트 안착부 치수로 ØB ~ ØC 사이 개선안을 적용하는 것이 적절하다고 판단하였다.
4. 결 론
2-Piston 캘리퍼의 래틀노이즈 발생 원인을 파악하고 개선하는 연구를 진행하였다. 단품 장착 조건 별 비교 분석을 통해 래틀노이즈 발생 위치가 가이드핀 부근인 것을 확인하였고, 캘리퍼 개발에 래틀 노이즈 이슈가 발생했을 시 즉각적인 개선을 적용할 수 있도록 토크멤버의 부트 안착부 가공 치수를 축소하여 가이드핀 부트 긴박력을 증대하는 방안을 적용하였다. 부트 안착부 치수가 축소됨에 따라 래틀노이즈 수준이 줄어들고, 노이즈 발생 시점이 지연되는 경향을 확인하였다. 이는 캘리퍼바디와 토크멤버 측면에 부착한 가속도계 측정 결과와 대응하여 분석할 수 있었다. 부트 안착부 치수가 축소될수록 캘리퍼바디와 토크멤버 사이의 가속도 차이가 줄어들어 일체화된 진동 경향이 강화됨에 따라 래틀노이즈가 개선되었다.
핀부트의 긴박력이 증대되게 되면 캘리퍼 접동 저항도 증대되어 드래그 및 마모 특성에 불리하게 작용할 수 있다. ØC 사양은 기본 사양 대비 Loudness 값이 -54.7 %(신품 패드), -50.7 %(마모 패드) 저감되었고, 캘리퍼 접동 저항은 30.0 % 상승하였다. 반면 ØD 사양에서는 Loudness 값이 -66.7 %(신품 패드), -46.2 %(마모 패드) 저감되었고, 캘리퍼 접동 저항은 62.8 % 상승하였다. ØD 사양부터는 래틀노이즈 개선 효과에 비해 캘리퍼 접동 저항이 과다하게 상승하는 시점으로 우리는 핀부트 안착부의 적정 개선 범위를 ØB ~ ØC으로 제안하였다. 캘리퍼의 사양 따라 최적의 부트 안착부 치수 범위가 달라질 수 있지만, 본 논문과 유사한 접근 방법으로 래틀노이즈 설계 개선 범위를 설정할 수 있을 것이다.
Acknowledgments
A part of this paper was presented at the KSAE 2022 Fall Conference and Exhibition
References
-
B. J. Seo, J. E. Jeon, G. D. Park, H. G. Kim, S. D. Park and J. E. Oh, “Evaluation of Vehicle Seat Rattle Noise Using Coherence Function Technique,” Transactions of the Korean Society for Noise and Vibration Engineering, Vol.21, No.8, pp.774-780, 2011.
[https://doi.org/10.5050/KSNVE.2011.21.8.774]
- J. M. Yang, C. H. Yi, S. I. Lee, H. C. Do and Y. H. Kim, “An Experimental Approach for Rattle Noise Improvement of Package Tray Child Anchor Cover Ass’y,” KSAE Fall Conference Proceedings, pp.1326-1329, 2019.
-
K. H. Baek, S. B. Choi, H. R. Hong, N. T. Jeong, H. U. Moon, E. S. Lee, H. M. Kim, S. U. Choi and M. W. Suh, “Optimal Design for the Rear-glass Joint of an Automobile for Squeak and Rattle Noise Reduction,” Int. J. Automotive Technology, Vol.19, pp.859-868, 2018.
[https://doi.org/10.1007/s12239-018-0083-3]
-
J. C. Lee, Y. S. Kwak and J. H. Park, “Signal Processing for MoC Brake Rattle Noise of Moving Vehicles Using Prony Analysis,” Journal of Korean Society for Nondestructive Testing, Vol.35, No.4, pp.245-250, 2015.
[https://doi.org/10.7779/JKSNT.2015.35.4.245]
-
S. Hamdi, S. Moore, A. Papinniemi and D. Stanef, “Quantification of Brake Pad Rattle Noise–Correlating Accelerometer Measurements with Subjective Ratings,” SAE 2007-01-3962, 2007.
[https://doi.org/10.4271/2007-01-3962]
-
L. Liang, P. Li and S. Chen, “Further Study of the Vehicle Rattle Noise with Consideration of the Impact Rates and Loudness,” SAE International Journal of Advances and Current Practices in Mobility, 2(2020-01-1261), pp.2285-2296, 2020.
[https://doi.org/10.4271/2020-01-1261]
-
G. Lee, K. Kim and J. Kim, “Development of an Algorithm to Automatically Detect and Distinguish Squeak and Rattle Noises,” SAE 2015-01-2258, 2015.
[https://doi.org/10.4271/2015-01-2258]
- B. R. Yoon, K. H. Jeon, Y. H. Kim and M. H. Byoun, “Pin-Boot Influence Analysis for Caliper Rattle Noise Improvement,” KSAE Fall Conference Proceedings, p.313, 2022.
-
E. Zwicker and H. Fastl, Psychoacoustics: Facts and Models, Springer Verlag, New York, 1999.
[https://doi.org/10.1007/978-3-662-09562-1]