
시험과 해석 모델을 이용한 피스톤 슬랩음 개발
Copyright Ⓒ 2023 KSAE / 213-07
This is an Open-Access article distributed under the terms of the Creative Commons Attribution Non-Commercial License(http://creativecommons.org/licenses/by-nc/3.0) which permits unrestricted non-commercial use, distribution, and reproduction in any medium provided the original work is properly cited.
Abstract
Piston slap noise from the dynamic motion of a piston depends on the clearance between the piston and the cylinder liner of an engine. Clearance would change based on the distortion from the thermal variations of the cylinder block and the piston. An integrated thermal management module helps improve fuel consumption rate by reducing time durations to heat the engine. However, rapid thermal changes could make piston slap noise much louder because of a wider clearance. This paper presents an analytic model and corresponding experiments to demonstrate piston slap noise. Data such as gas pressure, temperature, and acceleration are measured through experiments to set the boundary conditions and validate the analytic model. Test conditions are based on the logged data in vehicle tests when piston slap noise is audible. The accuracy of the analytic model is then validated with correlations to the measured data from the experiments. Through simulations, thermo-structural distortion and NVH response are modelled, and distortions of the cylinder liner and the piston from a cold start to fully warmed-up states are estimated. Using the analytic model, the mechanism to emit piston slap noise is analyzed, and the effects on NVH and durability performance are verified based on the variations of the design parameters.
Keywords:
Piston slap noise, Thermal distortion, Piston secondary motion, Elasto hydrodynamic키워드:
피스톤 슬랩음, 열 변형, 피스톤 이차 운동, 탄성 유체1. 서 론
환경 문제에 대한 관심과 우려가 지속되고 있는 가운데 자동차 산업 분야에서는 이산화탄소 저감을 위하여 다양한 형태의 신기술 개발과 적용을 위해 노력하고 있으며, 상품성 측면으로는 차량의 소음 및 진동 개선에 대한 증가된 고객의 요구를 만족시키기 위하여 지속적으로 연구개발을 수행하고 있다. 이를 위하여 차량개발 과정에서 특정한 성능을 향상시키기 위한 시스템이 도입될 경우, 타 성능에 대한 부작용 발생의 확인 및 검증 과정은 반드시 필요하다. 냉각수 유량 제어를 통하여 마찰력을 저감하고 효율을 향상시키는 통합 열관리 모듈(ITM)이 적용된 엔진이 탑재된 차량에서 피스톤 슬랩음(이하 슬랩음)이 발생하여 개선이 필요하였다. 본 연구에서는 슬랩음 개선을 위하여 피스톤 이차 운동 해석 모델을 구현하고 슬랩음 발생 현상의 분석과 개선안 적용에 따른 부작용을 검토하였다. 해석 모델 구축 및 검증을 위하여 엔진 대상시험으로 소음 발생을 재현하고 유량, 연소실 압력, 그리고 다양한 위치에서 온도를 측정하여 해석 모델의 경계 조건과 입력 값으로 사용하였다. 측정 값과 해석 모델에서 계산한 가속도의 비교를 통하여 모델의 유효성을 검증하였고, 해석 모델 기반 계산된 가속도 변화를 기준으로 슬랩음 크기의 변화를 판단하였다. 그리고 설계 인자 변경에 의한 슬랩음과 타 성능의 변화를 해석 모델을 통하여 확인하였다.
2. 시험 평가
피스톤의 이차 운동은 피스톤의 주 운동 방향인 실린더의 세로축 방향에서 벗어나는 운동으로 이러한 이차 운동으로 피스톤과 라이너의 접촉에 의한 슬랩음이 다양한 운전 조건에서 발생할 수 있다.1) 이번 연구에서는 슬랩음이 워밍업 구간에서 발생하는 것을 확인하고 냉각수 순환 제어에 의한 온도 변화에 영향을 받았을 것으로 판단하였다.2) 정확한 원인 분석과 해결 방안 마련을 위하여 Fig. 1에 나타낸 과정을 수행하여 해석 모델을 구축하였다. 문제 차량에서 소음 평가를 통하여 문제 소음이 발생하는 운전 조건과 수준을 확인하고 문제 차량에서 엔진을 탈거하여 무향실에 설치한다. 설치한 엔진에 해석 모델 입력 및 검증에 필요한 데이터 취득에 필요한 센서를 장착한 후 슬랩음 발생 운전 조건에서 시험을 실시하며 취득한 데이터를 사용하여 해석 모델 최적화를 수행한다. 이렇게 구축된 해석 모델을 사용하면 문제 소음 발생의 정확한 원인 분석과 해결 방안 수립이 가능하다.
2.1 차량 시험 평가
슬랩음의 발생 조건을 셀에서 재현하기 위해서는 보다 명확한 발생 조건의 정의가 필요하다.3) 이를 위하여 문제 발생 차량을 선정하고 다양한 외기온과 운전 조건에서 청음 평가를 진행한 결과, 영하의 외기온에서 장시간 방치, 시동 후 정차 상태에서 가속 페달로 엔진의 가감속 반복시 슬랩음이 크게 발생됨을 청음 평가로 확인하였다. 이 운전조건에서는 엔 진 온도를 빠르게 상승시키기 위하여 냉각수의 흐름을 정지시켜 불필요한 냉각이 발생하지 않도록, 그리고 목표 온도에 도달 시 냉각수를 순환시켜 냉각이 발생하도록 냉각수 제어 밸브(이하 밸브)가 제어된다. 슬랩음의 발생 주파수 대역 확인을 위하여 차량 실내소음을 측정하였다. 슬랩음이 발생하는 워밍업 구간에서 슬랩음은 Fig. 2의 왼쪽 그림과 같이 1 kHz 이상 주파수 대역에서 타음성으로 발생한다. 일정 시간이 지나면 오른쪽 그림과 같이 슬랩음이 작아지며 음압의 크기가 4 dB 이상 낮아진다. 슬랩음이 발생하는 조건에서는 냉각 제어에 의한 엔진의 온도 변화가 열 변형에 의한 간극 변화에 영향을 끼쳐 슬랩음이 악화되는 것으로 판단된다. 따라서 열변형 발생의 원인인 냉각수 온도 변화 예측을 위하여 냉각수 온도 모델 구현이 필요하다. 통합 열관 리 모듈은 밸브를 통하여 냉각수의 유동을 제어하며, 이로 인해 엔진 헤드와 실린더 블록(이하 블록) 온도가 변한다. 차량의 레이아웃을 기반으로 냉각수 유로를 해석 모델로 구현하고 슬랩음 발생 조건에서 밸브 후단 2곳에서 유량을, 워터펌프 입구 측 3곳에서 온도를 측정하여 모델 계산 값과 비교를 통한 검증을 수행하였다.
2.2 대상 시험 평가
피스톤 이차 운동 해석 모델 구축 및 검증에 사용할 데이터 측정을 위해 영하의 온도로 기온 조절이 가능한 무향실에 문제 엔진을 장착하였다. 설정한 영하의 외기온에서 8시간 이상 방치한 후 시험을 진행하였다. 냉각수의 온도 변화에 따라 슬랩음의 크기가 변화하기 때문에 차량 상태의 냉각수 유로가 셀에 최대한 모사되어야 하며 이를 위해 차량에서 탈거된 냉각수 유로 부품으로 대상 시험 냉각수 유로를 구성하였다. 슬랩음의 발생을 확인하기 위하여 마이크로폰을 이용하여 소음을 측정하고 차량 실내소음 분석결과와 동일하게 1 kHz 이상 주파수 대역에서 타음성 소리가 발생함을 확인하였다. 슬랩음 발생 시 피스톤의 거동에 의해 실린더라이너(이하 라이너) 측에 충격이 가해지고 이때 발생하는 블록 면의 진동 크기는 슬랩음의 크기와 비례하므로 진동을 통해 슬랩음 변화를 추정할 수 있다.4) 피스톤 운동 해석 모델의 검증에 활용하고자 Fig. 3과 같이 폭발 행정 시 피스톤이 아래로 운동할 때 횡력이 작용하는 블록 면의 스러스트 (Thrust)와 그 반대 면인 안티스러스트(Anti-thrust) 측 상/하단에 각 4개씩 총 16개의 단축 가속도계를 장착하고 가속도를 측정하였다.
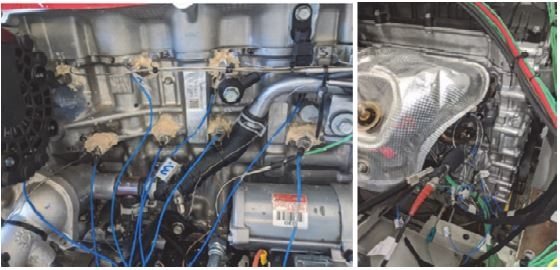
Accelerometers attached on each side of the engine block for estimating variations of piston slap noise
슬랩음 발생에 지배적인 영향을 주는 피스톤과 라이너 사이의 간극 크기는 운전 조건과 외기온 변화에 의한 변형의 영향을 받으므로 온도 변화에 따른 열 변형 예측해석 모델의 구성이 필요하다. 모델 구성에 필요한 온도 데이터를 확보하기 위하여 라이너와 피스톤 측의 온도를 측정하였다. 센서는 Fig. 4에 나타낸 것처럼 블록 라이너의 스러스트/안티스러스트 측 실린더의 블록과 라이너 사이에 열전대 온도 센서를 장착하였다. 왕복 운동을 하는피스톤은 텔레메트리(Telemetry) 타입의 온도 센 서를 장착하였다. 이 온도 센서의 신호 송수신 안테나에 피스톤 운동에 의한 간섭이 발생하지 않도록 엔진을 가공한 후 직렬 4기통 엔진의 바깥쪽을 대표하는 1번 실린더와 안쪽을 대표하는 2번 실린더에 장착하였다. 각 피스톤 온도 센서 위치는 Fig. 5와 같이 피스톤의 스러스트/안티스러스트와 중심부, 그리고 안쪽 위치에 총 6 개를 장착하여 온도를 측정하였고, 1번 실린더에는 스파크 플러그 일체형 압력 센서를 장착, 연소실 압력을 측정하고 연소 압력의 변화를 사용하여 연소실 내 온도 변화를 계산하였다. 시험을 통하여 취득한 데이터는 48 kHz의 샘플링 주파수로 함께 동시에 측정하였다.
3. 해석 모델
슬랩음 발생에 지배적인 영향을 주는 피스톤과 라이너 간 간극의 변화는 열 관성이 상대적으로 작은 라이너와 블록의 재료가 온도 변화에 의해 발생하는 변형에 영향을 받으므로 이를 예측하는 과도열전달해석(TTA)을 수행하였다. 과도열전달해석은 정상상태에서 열전달해석을 통하여 경계조건 온도 분포와 열전달계수(HTC)를 계산하고 이를 사용하여 온도 변화에 따른 과도상태의 열 변형을 계산한다. 해석을 통하여 슬랩음 유무에 따라 변형 정도를 예측한 후 변형 형상을 피스톤 운동 해석 모델에 적용하여 슬랩음 발생 현상을 분석하였다.
3.1 열 변형 모델
과도열전달해석을 위해서는 정상상태에서의 경계 조건 온도 및 열전달계수 값의 계산이 필요하다. 정상상태는 슬랩음 발생 시 연속된 사이클 중 블록 가속도의 크기가 가장 큰 조건으로 선정하여 화염 온도를 계산하였다. 계산된 온도를 사용하여 실린더 보어와 피스톤 크라운을 통한 열전달, 피스톤 링과 스커트를 통과하여 라이너로 유입되는 피스톤 크라운 하단의 오일 분사(PCJ)에 의한 냉각, 그리고 밸브 시트와 가이드를 통하여 밸브로 전달되는 온도 분포의 경계조건 값을 열전달 메커니즘 데이터를 기반으로 계산하였다. 슬랩음의 유무에 따라 화염 면과 실린더 보어의 온도 경계 조건을 반영하여 정상상태에서의 온도와 열전달계수의 분포를 Fig. 6에 나타내었다. 슬랩음이 인지되지 않는 조건의 연소실 내 온도 분포와 열전달계수의 계산을 위하여 냉각수 유로 모델에서 얻어지는 워터펌프 입구 측 온도를 사용하고 연소실 압력은 슬랩음 유무에 따라 추출하여 사 용하였다. 흡배기 포트, 오일 갤러리, 오일 분사 그리고 외기와 오일이 접촉하는 면의 열 유속 부하(HFL)는 상수 값을 적용하였으며 열전달계수는 데이터 베이스를 이용하였다. 열 유속 부하의 상승은 측정된 연소실 압력 값을 사용하여 슬랩음 발생 시와 동일하게 계산하였다. 과도열전달해석을 수행하기 위해서 Fig. 7과 같이 라이너를 10개의 영역으로 구분하고 운전 시간과 피스톤 위치에 대한 온도 계산 인자를 슬랩 음 유무에 따라 다르게 적용하였다.
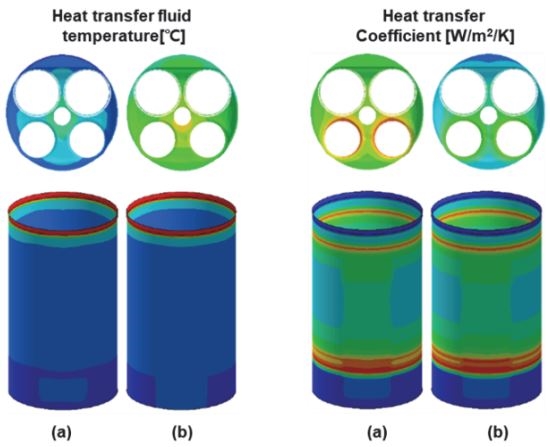
Gas side boundary conditions including temperature of the flame face and cylinder bore when piston slap noise are (a) audible, and (b) inaudible
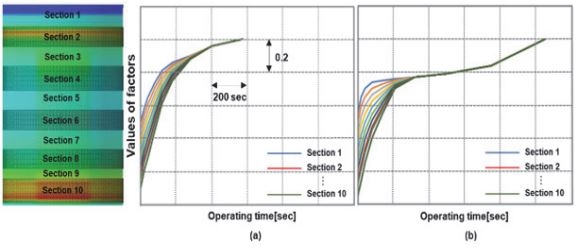
Factors for calculating temperatures for divided sections of block liner when there are cases in (a) no flow, and (b) flows of coolant water through heater core
운전 초기에는 라이너 상단 영역의 인자 값이 하단 대비 크지만, 일정 시간 운전 후 그 차이가 사라지는 것을 확인할 수 있었다. 피스톤의 온도는 Fig. 8과 같이 링과 스커트, 그리고 오일 영역으로 구분하여 영역에 따라 링과 스커트에는 Fig. 8의 인자를, 오일 접촉 면은 Fig. 7의 인자를 적용하여 온도를 계산하였다. 블록, 헤드, 그리고 라이너 사이는 볼트 체결로 인하여 열 변형의 확장이 제한되는 것으로 하였으며, 볼트 체결 부하에 의한 변형은 측정한 값을, 그리고 헤드와 블록 사이의 가스킷은 아바쿠스(Abaqus) 프로그램의 가스킷-블록 모델 데이터를 사용하였다. 과도열전달해석을 사용하여 슬랩음이 유무에 따른 계산된 블록과 피스톤의 온도 분포를 Fig. 9에 나타내었다. 슬랩음 발생 조건에선 엔진 온도 상승을 위해 냉각수 유동을 제한하기 때문에 (a)와 같이 블록과 피스톤의 상단과 하단의 온도 차이가 미발생 조건인 (b) 대비해 크게 나타났다.
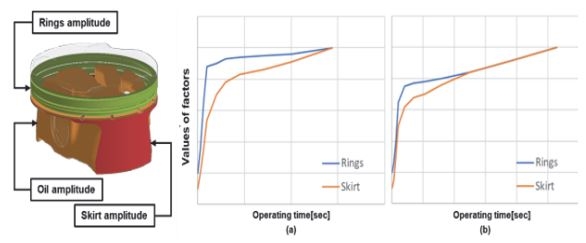
Divided areas of a piston to apply different values and variations of factors according to operating time when there are cases in (a) no flow, and (b) flows of coolant water through heater core
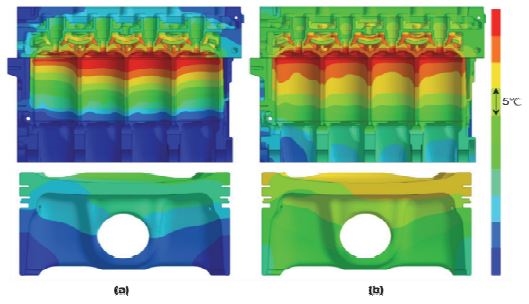
Temperature distributions of cylinder block and piston calculated by the model when piston slap noise are (a) audible, and (b) inaudible
과도열전달해석 모델로부터 계산된 온도 분포 값의 신뢰도 확인을 위하여 특정 위치에서 시험을 통해 측정된 온도와 비교한 결과를 Fig. 10에 나타냈다. 온도는 블록과 라이너 사이 상/하단에 15개, 그리고 1, 2번 실린더의 피스톤에 장착한 6개의 온도 센서장착 위치에서 시험 측정 값과 모델 계산 값을 슬랩음 유무에 따라 비교하였다. (a)와 (b)는 라이너, (c)와 (d)는 피스 톤의 온도를 나타내며 (a), (c)는 슬랩음 발생, (b)는 슬랩음 미발생 조건이다. 과도열전달해석 모델을 통하여 얻어진 온도와 측정 값 사이의 일반적인 허용 가능 오차는 라이너 측 10 oC, 피스톤 측 5 oC 이하이며 모델에서 계산된 온도는 이를 만족하여 신뢰할 수 있는 수준으로 판단된다.5) Fig. 11은 슬랩음 발생 조건에서 모델 온도 분포와 체결에 의한 경계 조건이 반영된 모델에서 계산된 실린더의 열 변형 크기를 나타낸 것이다. 변형의 크기는 온도가 급격히 상승한 라이너 상단에서 팽창이 크게 나타났으며 1번과 4번, 그리고 2번과 3번 실린더의 경향이 유사하게 나타났다. 이러한 경향은 라이너의 온도 변화와도 일치한다.
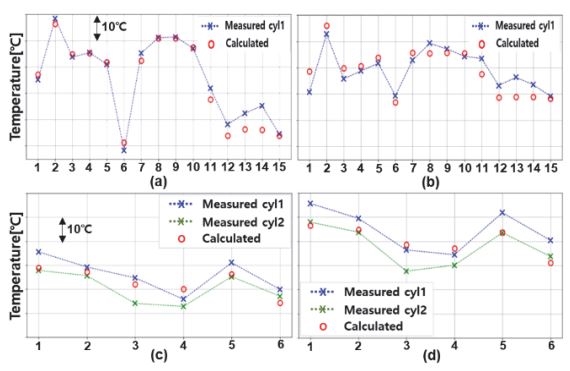
Comparing measured temperatures in tests with calculated temperatures by the model on specified positions: at liners when piston slap noise are (a) audible and (b) inaudible, at pistons (c) audible and (d) inaudible
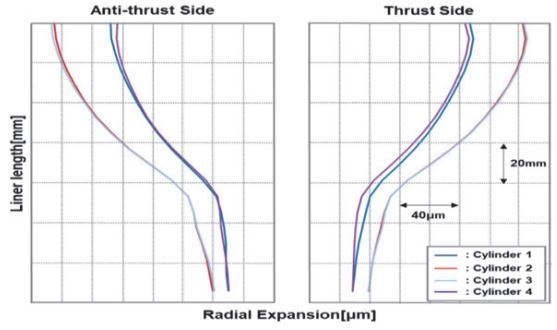
Radial expansion lengths to thrust and anti-thrust sides calculated by the analysis model when piston slap noise is audibleFig. 12 Accelerations measured in tests on thrust and anti-thrust sides of liners of cylinder 1 and 2 when piston slap noise is audible
Fig. 10에서도 2, 3번 실린더 라이너 상단 온도 분포가 더 높게 나타나는 것이 확인되며 슬랩음은 피스톤과 라이너 간 간극에 비례하므로 2, 3번 실린더가 더 클 것으로 판단된다. 실린더 간 슬랩음 차이를 확인하기 위하여, 엔진 시험에서 측정된 블록 표면 가속도를 크랭크 각도에 대해서 Fig. 12와 같이 분석하였다. 상단 그림은 1번, 하단 그림은 2번 라이너와 평행한 스러스트/안티스러스트 측 위/아래에서 측정된 가속도 값이다. 두 그림 모두 첫번째 가속도 피크는 2번 실린더 연소 상사점 기준 약 30도 이전 위치, 두번째 피크는 1번 실린더의 연소 상사점 기준 동일 한 위치에서 발생한다. 라이너 평행선 상의 가속도는 2번 실린더의 최대값이 1번 실린더 대비 약 2.5 m/s2 크다. 상단 그림의 1 번 실린더 진동은 1번 실린더 피스톤 거동이 지배적이지만 2번 피스톤에 의한 진동의 크기도 거의 동일하게 크게 나타나며, 2번 피스톤 운동에 의한 슬랩음의 크기가 더 큰 것으로 예상할 수 있다. 슬랩음 발생 매커니즘 분석을 위한 2차 운동 모델 시뮬레이션은 많은 시간이 소요되기 때문에 이를 최소화하기 위하여 가장 큰 슬랩음이 발생될 것으로 예상되는 2번 실린더에 대해서 모델을 구현하였다.
3.2 피스톤 운동 모델
피스톤의 운동 모델 구현 시 피스톤 핀 베어링, 피스톤 스커트(이하 스커트)와 라이너 사이의 유체역학 및 경계 윤활은 이차원 레이놀즈 방정식에 대한 유한 체적(FV) 솔루션으로 계산하고 피스톤과 라이너 사이의 부하는 생성된 윤활 분할 데이터를 사용하여 유막 및 경계 접점 압력 분포를 계산하여 예측하였다. 스커트와 블록의 탄성은 윤활 분할과 강성 분할 사이의 상관성을 유한요소(FE) 모델에 의한 분석에 포함하여 탄성 유체(EHD) 윤활을 사용하여 계산하였다.6) 열, 관성력, 그리고 압력 부하에 의한 피스톤 변형을 모델에 포함하였으며 라이너의 변형은 열 변형 유한요소 모델 결과를 반영하였다. 해석 모델의 계산 부하 최적화를 위하여 Fig. 13과 같이 윤활 메쉬(Mesh) 수를 최소화하였고 연소에 의한 온도 변화 및 변형은 실린더 헤드와 블록 모델에 포함되었다.
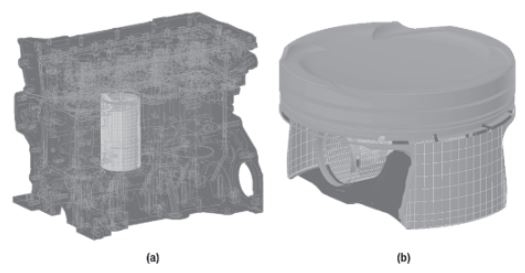
Models of (a) block liner, and (b) the piston of cylinder 2: The total number of nodes are optimized with coarsening the total number of lubrication mesh to reduce simulation load
피스톤 운동 모델의 검증은 블록 표면 가속도의 시험을 통하여 측정한 데이터와 모델에서 계산된 데이터를 비교하여 검증하였다. 검증에 사용된 블록 표면 가속도 데이터를 슬랩음 인지 여부에 따라 크랭크 각도에 대하여 Fig. 14에 나타내었다.
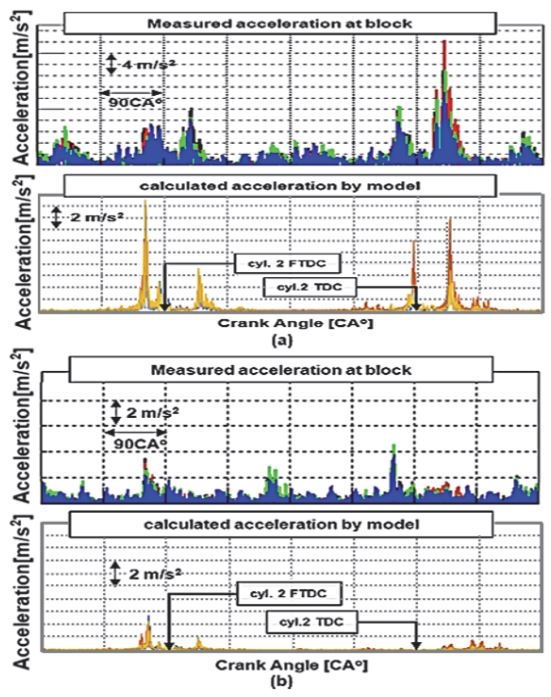
Accelerations at engine block measured in tests and calculated by the model when piston slap noise are (a) audible, and (b) inaudible
슬랩음 인지 조건은 그림 (a)에 나타낸 것처럼 계산 값과 측정 값 사이에 오차가 존재한다. 그러나 이 오차 발생 원인은 피스톤 운동 모델의 경우 2번 실린더 가진력만 반영되지만 측정된 값은 모든 실린더의 가진력이 반영되기 때문인 것으로 판단된다. 따라서 모델의 유효성은 가속도 절대값의 피크 발생 위치와 경향을 기준으로 판단되어야 한다. 슬랩음 미인지 조건은 워밍업 후 연소 가진력이 감소한 상태이므로 그림 (b)에 나타낸 것처럼 연소 상사점 부근의 가속도 크기가 상대적으로 작으며 모델에서는 2번 실린더의 가진만 반영되므로 2번 연소 상사점에서만 가속도 피크가 발생한다. 측정 값과 계산 값의 연소 상사점 부근 피크의 발생 위치가 일치하며 그 크기의 변화로 슬랩음의 변화 예측이 가능하다. 보다 객관적인 슬랩음 변화를 판단하기 위하여 Fig. 15와 같이 피스톤 운동 모델에서 일반적으로 사용하는 스러스트에서 안티스러스트 측으로 발생하는 운동의 강도를 나타내는 이차 동적 에너지(SKE)를 사용하였다. 슬랩음 인지조건에서 슬랩음 발생에 영향 을 주는 피스톤 핀의 횡력에 의한 횡방향, 그리고 모멘트 균형에 따라 결정되는 회전방향 이차 동적 에너지를 계산하였다.6) 두 값 모두 피스톤과 보어의 상호 구속에 의하여 결정되는 값이며 피스톤 핀 옵셋(Pin offset), 라이너와 피스톤 간 간극의 변화, 그리고 스커트의 형상 등에 영향을 받는다. 이차 동적에너지의 피크 값도 블록 표면 가속도와 유사하게연소 상사점 30도 이전 위치에서 발생하는 것을 확인할 수 있다.
4. 모델 기반 개선안 검토
슬랩음 개선을 위하여 피스톤과 라이너 접촉에 의한 면압 발생에 영향을 주는 스커트 프로파일(Profile) 변경의 영향을 검토하였다.7) 슬랩음 인지 조건에서 연소 상사점 전후 60도 영역에서 스커트 끝단의 면압은 Fig. 16과 같이 국부적으로 높게 분포됨을 확인할 수 있다. 이러한 접촉에 의한 압력은 피스톤의 빠른 운동에 의하여 큰 진동을 발생시킬 수 있으며 압력 분포를 축소하는 방향으로 스커트 프로파일, 핀 옵셋, 그리고 두 인자를 함께 변경하는 경우의 블록 가속도의 변화를 피스톤 운동 모델을 사용하여 확인하였다.8)
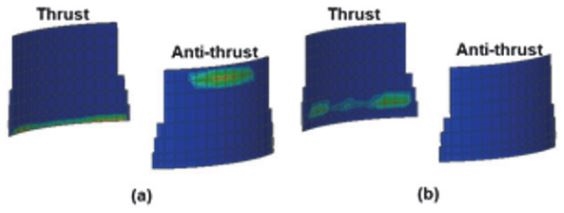
Pressure distribution calculated by the model on the piston skirt at (a) pre at firing TDC, and (b) post at firing TDC
Fig. 17은 연소 상사점 전후 60도 구간에서 인자변경에 의한 블록 표면 가속도의 최대값을 나타낸 것이다. 핀 옵셋 증대시 안티스러스트 측 최대 가속도가 증가하여 슬랩음은 커지며, 스커트 프로파일 변경은 안티 스러스트 측과 연소 상사점 이후 최대 가속도 는 감소하며 슬랩음이 개선될 것으로 판단된다. 두 설계 인자를 동시에 변경하면 안티스러스트 측 연소 상사점 이전과 스러스트 측 연소 상사점 이후의 최대 가속도는 감소되나 그 외 영역에서 미세하게 증가하는 경향을 나타낸다. 슬랩음 개선을 위해 이러한 설계 인자를 변경하면 슬랩음 이외에도 연비, 내구와 같은 타 성능이 영향을 받는다. 따라서 Fig. 18과 같이 마찰력 손실 및 최대 마모 부하(MWL)의 변화량으로 내구 성능에 대한 영향을 검토하였다.
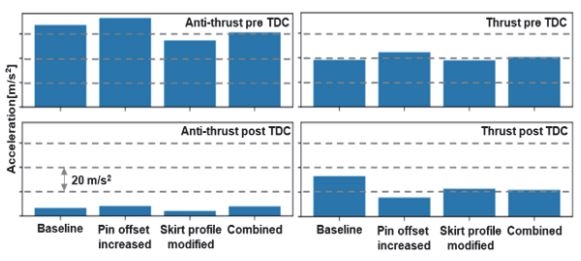
Maximum accelerations at anti-thrust and thrust sides during 60CAo pre and post from firing TDC when variations of design parameters to reduce piston slap noise in the model are applied
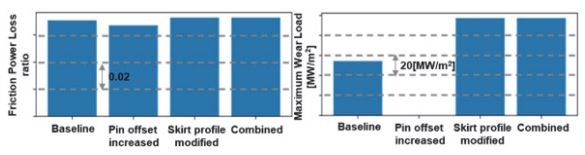
Friction power loss and maximum wear load during 60CAo pre and post from firing TDC when variation of design parameters to reduce piston slap noise are applied
핀 옵셋 증가 시 마찰력 손실과 안티스러스트 측 최대 마모 부하는 감소하지만 Fig. 17에 나타낸 것처럼 안티스러스트 측 최대 가속도는 증가한다. 스커트 프로파일과 함께 변경 시에는 안티스러스트 측 최대 가속도는 감소하지만 Fig. 18과 같이 마찰력 손실과 최대 마모 부하가 증가됨을 확인할 수 있다. 이와 같이 피스톤 운동 모델을 구현하면 설계 인자 변경이 다른 성능에 미치는 영향을 고려하는 것이 가능하며 이를 기반으로 시험을 통한 최종 검증에 필요한 샘플 수를 최소화하여 시간과 비용을 절약할 수 있다.
5. 결 론
워밍업 조건에서 발생한 슬랩음 예측을 위하여 냉각수 온도 변화에 따른 구조 열 변형을 포함한 피스톤 운동 모델의 구성이 필요하며, 피스톤 운동 모델 유효성은 시험에서 측정된 블록 가속도 데이터를 사용하여 검증하였다. 슬랩음의 변화는 모델로부터 계산된 블록 표면 가속도, 이차 운동에너지 그리고 피스톤 면압을 통하여 확인하였고 마찰 손실과 최대 마모 부하를 통하여 내구 성능의 영향도 예측하였다. 이와 같이 피스톤 운동 모델을 구현하면 슬랩음 개선을 위한 설계 인자 변경 시 타 성능의 영향을 함께 예측할 수 있다. 엔진 개발 시 시험과 해석을 통하여 피스톤 운동 모델을 구현하면 다양한 성능의 영향을 고려한 효율적인 개선안 수립을 통하여 업무 효율을 향상 시킬 수 있다.
Subscripts
ITM : | integrated thermal management module |
HTC : | heat transfer coefficient |
FE : | finite element |
TTA : | transient thermal analysis |
PCJ : | piston cooling jet |
HFL : | heat flux load |
FTDC : | firing top dead center |
FV : | finite volume |
EHD : | elasto hydrodynamic |
SKE : | the secondary kinetic energy |
MWL : | maximum wear load |
References
-
T. Kobayashi, Y. Takahashi and D. J. Bell, “How to Predict the Piston Slap-Noise Using 3D Piston Motion Simulation,” SAE 2007-01-1245, 2007.
[https://doi.org/10.4271/2007-01-1245]
-
P. Bonkoski, A. Y. Karnik and A. Fuxman, “Calibration and Demonstration of Vehicle Powertrain Thermal Management Using Model Predictive Control,” SAE International Journal of Engines, Vol.10, No.2, pp.173-180, 2017.
[https://doi.org/10.4271/2017-01-0130]
-
T. Resch, O. Knaus, S. Thomann, and S. Brandl, “Performance Attributes for Root Cause Detection of Piston Induced Noise,” SAE 2016-01-1775, 2016.
[https://doi.org/10.4271/2016-01-1775]
- S. H. Cho, S. T. Ahn, Y. H. Kim and D. S. Lee, “Estimation and Analysis of the Piston Slap Induced Vibration,” KSAE Spring Conference Proceedings, pp.483-488, 1999.
-
T. Kobayashi, Y. Takahashi and D. J. Bell, “How to Predict the Piston Slap-Noise Using 3D Piston Motion Simulation,” SAE 2007-01-1245, 2007.
[https://doi.org/10.4271/2007-01-1245]
-
M. Duyar, D. Bell and M. Perchanok, “A Comprehensive Piston Skirt Lubrication Model Using a Mass Conserving EHL Algorithm,” SAE 2005-01-1640, 2005.
[https://doi.org/10.4271/2005-01-1640]
-
A. Jay, T. Deighan, N. Kato and K. Sato, “Piston Design for Optimizing Trade-off of Friction and NVH,” SAE International Journal of Passenger Cars-Mechanical Systems, Vol.9, pp.1125-1135, 2016.
[https://doi.org/10.4271/2016-01-1855]
-
T. Kim, “Dynamic Behavior Analysis of Reciprocating Compressor Pistons,” Transactions of the Korean Society for Noise and Vibration Engineering, Vol.12, No.9, pp.717-724, 2002.
[https://doi.org/10.5050/KSNVN.2002.12.9.717]