
AMT 싱크로나이저 시스템의 윤활유 공급 및 주축 회전 속도에 의한 드래그 특성 연구
Copyright Ⓒ 2022 KSAE / 197-08
This is an Open-Access article distributed under the terms of the Creative Commons Attribution Non-Commercial License(http://creativecommons.org/licenses/by-nc/3.0) which permits unrestricted non-commercial use, distribution, and reproduction in any medium provided the original work is properly cited.
Abstract
The synchronizer slip mechanism in the slip ring and cone of the automated manual transmission(AMT) is investigated with respect to relative velocity, fluid gap magnitude and lubricant supply flow rate in order to find better design parameters for less drag torque and higher power transfer efficiency. Fluid spaces inside the gaps of the AMT synchronizer module are modeled in detail for CFD(FLUENT) analysis. Fluid flow behaviors through the gap space of AMT synchronizer module are calculated in terms of volume of fluid and dynamic pressure. This study focuses on the formation of fluid fraction of fluid space inside the synchronizer module and drag torque on the synchronizer friction surfaces, which are investigated according to the design and operational parameters of the synchronizer module. Computational results based on real design and operational parameters are compared to yield useful design guides on the less drag torque of the synchronizer system.
Keywords:
Synchronizer system, Flow behaviors, Drag torque, Volume of fluid, Automated manual transmission fluid(AMTF), Parameter study, Design parameter, Computational fluid dynamics키워드:
싱크로나이저 시스템, 유동, 드래그 토크, 유체 체적, 자동화수동변속기유, 파라미터 스터디, 설계 변수, 전산 유체 역학1. 서 론
자동차 시장의 고성능 및 고효율화를 위한 연구는 연비 및 내구성을 위한 제품 경쟁력 향상을 위해 동력원의 종류에 상관없이 필수적으로 필요하다. 파워트레인 구조 측면에서는 내연기관만을 사용하던 기존의 차량에서 전기 모터를 추가로 사용하는 하이브리드 차량이나 순수하게 전기모터로 구동하는 전기차 및 수소 연료 전지 차량으로 연구가 확대되고 있다.1)
그 중 대형 상용 차량의 경우 기존에 사용하던 파워트레인 시스템에서 보다 효과적으로 동력을 전달하기 위해 동력전달 효율이 높은 수동변속기에 제어 로직을 추가하여 편의성과 연비, 성능, 조작 난이도 등을 개선한 자동화 수동 변속기(Automated Manual Transmission, AMT)를 사용하고 있다.2) AMT의 경우는 기존의 수동 변속기와 마찬가지로 기어박스 안에 존재하는 여러 개의 기어들의 기어비를 통해 변속을 하며, 이 변속 과정에서 기어들의 속도 동기화는 싱크로나이저 시스템(Synchronizer system)을 통해 가능하게 한다. 싱크로나이저는 미끄럼 마찰에 의하여 상대 속도를 점진적으로 낮추면서 서로 다른 속도로 움직이는 상대 접촉물을 동기화시키는 운동을 한다. 이 과정에서 마찰열이 많이 발생하며, 마찰열이 제대로 냉각되지 못할 경우 접촉 부품의 손상 및 기능저하 등이 발생할 수 있기 때문에 윤활유를 통해 냉각 및 윤활을 원활하게 해야 한다. 그리고 이때 윤활유가 지나치게 많이 공급될 경우에는 드래그 토크뿐만 아니라 윤활유 공급을 위한 불필요한 동력소모가 발생하여 동력전달 효율이 감소하는 원인이 되어 이를 방지하기 위한 연구도 필요하다.3)
본 연구에서는 대형 12속 AMT 스플리터 모듈에서 싱크로나이저 시스템의 내구성과 전달 효율 향상을 위하여 회전 속도 및 공급 유량에 따른 윤활 성능과 드래그 토크 발생 크기에 대한 경향성을 규명하며, 싱크로나이저의 콘과 링에서 동기화 과정 중에 상대 접촉 속도에 따른 마찰열과 드래그 토크 발생에 대한 연구를 진행한다. 해석 수행은 상용 CFD 해석 프로그램인 Ansys Fluent를 이용하였다.
2. 연구 방법
2.1 AMT 구조와 Synchronizer System
Fig. 1은 본 연구의 대상인 대형 12속 AMT의 전체적인 구조다. AMT는 한 개의 주축(Mainshaft)에 두 개의 부축(Counter shaft)이 평행하게 설계되어 있다. 앞쪽부터 스플리터, 메인, 레인지 영역으로 나누어지며 이들의 조합을 통해 변속이 이루어진다. 싱크로나이저를 사용하는 부분은 스플리터와 레인지 영역이며, 이 중 변속에서 가장 자주 사용되는 부분은 스플리터 영역이기 때문에 이 부분을 본 연구의 대상으로 진행하였다. 또한 설계 및 작동 조건에 따른 싱크로나이저 내부 변속기유와 드래그 토크의 경향성 판단을 위해 고단(High단) 비체결 상태의 모델을 통해 해석을 연구를 진행하였다.
AMT의 윤활유 공급은 AMT 하부의 오일펌프를 통해 공급되며, 윤활 회로를 따라 변속기 전체를 순환하여 공급된다. 부축에는 각각의 윤활유 공급을 위한 파이프가 설계되어 있다. 주축과 싱크로나이저 시스템은 주축에 있는 오일 홀들을 통해 윤활유를 공급받으며 그 세부적인 수치는4) 2.4.2절의 해석조건에서 자세히 기재해 놓았다.
AMT 싱크로나이저는 스플리터와 레인지 영역에서 사용이 되며 각각 핀-타입과 키-타입이 사용된다. 연구 대상인 스플리터의 경우 중립 단계는 존재하지 않으며, 저단과 고단 두 가지 상태로만 작동된다. Fig. 1을 기준으로 왼쪽이 저단 기어 오른쪽이 고단 기어다. 즉, 본 연구는 왼쪽의 저단에 체결된 상태를 기준으로 한다.
일반적인 싱크로나이저의 설계 요소는 크게 3가지로 구성되며 자세한 모습은 아래 Fig. 2에서 확인할 수 있다. 첫번째는 콘이 기울어진 각도인 콘 각(Cone angle, θ)이다. 싱크로나이저 시스템의 전달 토크와 크게 관련된 수치이다. 두번째는 콘 반지름(Cone radius, RC)이며 이는 콘과 링이 체결되는 지점에서의 측정한 반지름이며 이는 싱크로나이저의 전체적인 크기를 결정한다. 마지막 설계 변수는 마모 간극(Wear gap)으로 체결된 상태에서의 콘 기어와 링 사이의 간격이다. 이 마모 간극의 수치는 싱크로나이저의 체결이 반복될수록 마모에 의하여 그 크기가 줄어든다. 이와 관련한 본 연구의 대상은 비체결 상태의 드래그 및 윤활 냉각 성능으로 마모 간극이 아닌 반대쪽의 유체 간극(Fluid gap)의 설계변수이다. 유체 간극은 반대쪽의 콘과 링이 완전히 체결된 상태에서의 콘 기어(Cone gear)와 링 사이의 간격이다. 즉, 반대쪽의 비체결된 콘과 링의 윤활 및 냉각 오일의 공급에 영향을 미치는 수치다. 그리고 유체 간극은 마모 간극이 작아질수록 커진다.
본 연구에서 사용한 싱크로나이저의 모델링의 설계 조건의 세부적인 수치는 아래의 Table 1에 기재되어 있다.
2.2 Fluent Synchronizer 해석 지배 방정식
싱크로나이저의 유체 흐름이 발생하는 부품 사이의 틈새에서 변속기유의 거동은 CFD 해석을 통하여 계산한다. 콘과 링의 틈새에서의 유체 거동을 틈새의 유체 부피 분율(Volume of fluid, 격자점 공간에서 유체의 비율), 동수압 크기 및 유체거동 속도를 계산하여 분석한다.
(1) |
(2) |
식 (1)은 CFD 해석 소프트웨어에서 다루고 있는 연속 방정식(Continuity Equation)이며, 식 (2)는 운동량 보존 방정식(Momentum Conservation Equations)이다. 싱크로나이저 틈새 내부에서 일어나는 유동 해석 결과는 유체요소의 압력과 속도이며, 이러한 해석결과 내용으로 유체요소의 유체 분율과 전단저항력을 통한 드래그 토크를 계산할 수 있다.
2.3 드래그 토크(Drag Torque)
드래그 토크는 좁은 틈에서 오일의 점성과 상대 회전속도에 의해 발생하는 전단 응력에 의해 발생하는 저항의 일종이다. 유한요소 해석에서는 각 격자에서 형성되는 전단 응력과 회전 중심까지의 거리를 곱한 수치를 면적분하여 계산할 수 있으며 아래의 식 (3)으로 나타낼 수 있다.
(3) |
2.4 해석 대상 모델링 및 해석 조건
싱크로나이저 모듈의 상대 운동하는 틈새에서의 유체 모델링뿐만 그 내부에 변속기유가 공급되는 주축의 오일 홀부터 유체가 싱크로나이저 모듈에서 나가는 출구(Outlet)까지 구현된 유체 모델(Fluid Model)이 필요하다.
위의 Fig. 3은 변속기유 공급이 발생하는 입구(Inlet)와 싱크로 모듈에서 출구(Outlet)의 위치를 표현한 자료다. 본 연구에서 배출되는 AMT의 변속기유 공급은 변속기 하부에 모인 오일을 펌프를 통해 변속기 윤활 회로를 따라 공급하는 방식을 사용한다.5) 스플리터 파트의 경우 주축에 있는 5개의 오일홀을 통해 변속기유를 공급받는다. Fig. 3에서 스플리터 파트 외부로 나가는 곳은 모두 출구(Outlet)로 지정하여 유체 모델을 완성하였다.
싱크로나이저의 드래그 토크에 가장 크게 영향을 주는 싱크로나이저의 링과 콘의 마찰 표면(Friction Surface)의 형상은 아래의 Fig. 4에 표시하였다.
싱크로나이저의 좁은 틈에서의 유체 거동은 층류 유동(Laminar flow)이 지배적이지만, 작은 틈새의 공간에서 고속의 상대 속도로 인한 난류가 발생할 가능성이 있다고 판단하여 정상 상태의 k-epsilon 해석 모델을 사용하였다. 또한, 실제의 변속기의 상황을 고려하여 내부에 윤활 냉각을 위한 변속기유와 공기가 공존하는 것을 구현하기 위해 VOF(Volume of Fluid) 해석 모델을 사용하였다. 해석에서 사용한 변속기유와 공기의 물성치는 아래의 Table 3에서 표시하였다.
자동화 수동변속기의 싱크로나이저 구동 해석은 기본적으로 유체 간극(Fluid gap) 5.03 mm를 기준 모델(Base model)로 하여 회전속도, 유량 그리고 유체 간극(Fluid gap)까지 총 3가지의 설계 및 작동 조건 영향 인자를 고려하여 해석을 진행하였다.
Fig. 6에서 싱크로나이저 모듈에서 변속기유 공급 유량과 유체 거동 해석을 위한 경계 조건(Boundary condition)을 표시하였으며, Table 4는 기준 모델의 해석에 사용된 싱크로나이저 모듈의 작동 및 윤활유 공급 조건을 표시하였다. Fig. 6에서 표시한 싱크로 모듈에서 각 부품의 회전은 모두 주축 중심을 기준으로 진행이 되며 비체결된 기어의 속도는 본 연구의 대상인 대형 12속 AMT작동 기어비를 계산하여 적용하였다. 또한, 위의 Fig. 3에서 표시한 바와 같이 입력부(Inlet)에 해당하는 오일홀은 총 5곳으로 선정하였으며, 각각의 오일홀에서 유량의 세부적인 수치는 선행 진행된 연구의 결과4)를 참조하였다. 선행 진행된 연구는 AMT 전체 윤활회로에서의 CFD해석을 통해 각각의 홀에서 유량 산출량이 얼마나 되는지, 또한 오일홀의 형상 변환을 통해 변화를 주었을 때 윤활유량 분배가 어떤 식으로 되는지 최적화에 관한 논문이다. 이 논문에서 형상 변화가 없는 기본 모델(Base model)에서의 윤활유 토출 데이터를 해석에 적용한다. 출구(Outlet)의 경우 변속기 내부에 공기와 변속기 오일이 공존하는 것을 반영하여 대기압 조건을 반영하였다.
기준 모델을 바탕으로 주축의 회전속도와 변속기유 공급 유량을 변화하여 다양한 해석을 진행하였으며, 보다 가혹한 작동 환경 일 수 있는 조건을 구현하여 비교 해석하였다. 변속기 주축 회전속도의 경우 2배, 3배로 증가 시켜 해석을 진행하였으며, 유량은 총 유량을 기준으로 0.25배 및 0.5배로 변경하여 해석을 진행하였다. 즉, 싱크로나이저 구성 부품의 상대 속도는 크게 하며, 윤활유 공급을 작게 하는 가혹한 운전조건을 모사 시킨다. 이때 모든 오일홀의 유량 비율은 일정하게 유지하여 해석을 진행하였다. 유체 간극(Fluid gap)은 5.03 mm에서 4.53 mm와 4.03 mm로 줄여가면서 해석을 진행하였다. 모든 해석은 이와 같이 변경되는 조건을 제외하고 나머지는 기준 모델의 조건을 유지하였다. 자세한 내용은 Table 5에 나타내었다.
3. 유동해석 결과
3.1 회전속도 변화에 따른 유동해석 결과
Figs. 7과 8은 Fig. 3에서 설정한 싱크로나이저 모듈의 틈새와 유체 모델(Fluid model) 단면(Cross section)의 Table 5에서 설정한 속도 크기에 따른 VOF와 동압력 결과값이다. 전체적으로 주축의 회전 속도가 증가함에 따라 스플리터 모듈 내부의 유체가 줄어드는 것을 확인할 수 있다. 이는 원심력에 의한 영향으로 판단된다. 이를 보다 세밀하게 분석하기 위하여 콘과 링의 표면에서 윤활유 막이 표면에 형성되는 분포를 콘과 링에서의 결과값을 분리하여 비교하였다. Fig. 9는 Fig. 4에서 확인한 콘과 링의 마찰 표면(Friction Surface)에서 변속기유의 양(Surface Fraction, 표면 분율)에 대한 결과값이다. 이전 Figs. 7과 8에서의 결과값과 마찬가지로 주축의 회전속도가 빨라질수록 표면 분율의 수치가 감소하는 것을 확인할 수 있다.
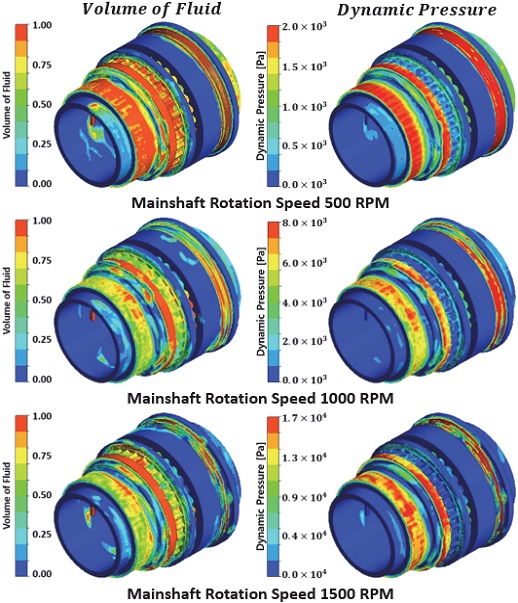
VOF and dynamic pressure in synchronizer module clearness according to rotational speeds in Table 5 (Total inlet 2.056 lpm, fluid gap 5.03 mm)
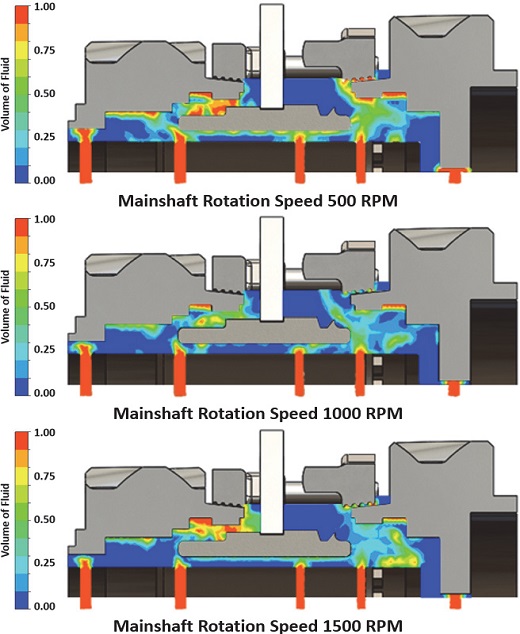
Section view VOF in synchronizer module according to rotational speed in Table 5 (Total inlet 2.056 lpm, fluid gap 5.03 mm)
Fig. 10은 Fig. 9의 콘과 링의 표면에 분포된 유체 분율의 수치 데이터다. Fig. 11은 콘과 링 표면에서 발생하는 드래그 토크(Drag Torque)의 수치이다. 표면 분율의 경우 위에서 속도가 빨라질수록 원심력의 영향으로 줄어드는 경향성을 보인다. 그러나 드래그 토크의 경우 유체의 표면 분율이 작지만 속도가 빨라질수록 그 크기가 커지는 경향성을 보이고 있다.
3.2 공급 유량 변화에 따른 유동해석 결과
Figs. 12와 13은 싱크로나이저 모듈에서 앞서 설명한 내용과 같은 방식으로 입력 유량에 따른 VOF, 동압력의 해석값이다. 예측할 수 있는 바와 같이 유량이 줄어듦에 따라 스플리터 모듈 내부의 유량이 줄어드는 것을 확인할 수 있다. VOF(Volume of Fluid)는 Fig. 14의 콘과 링의 마찰 표면에서의 표면 분율의 수치에서도 속도에 따른 해석 결과와 같이 같은 결과를 보여준다.
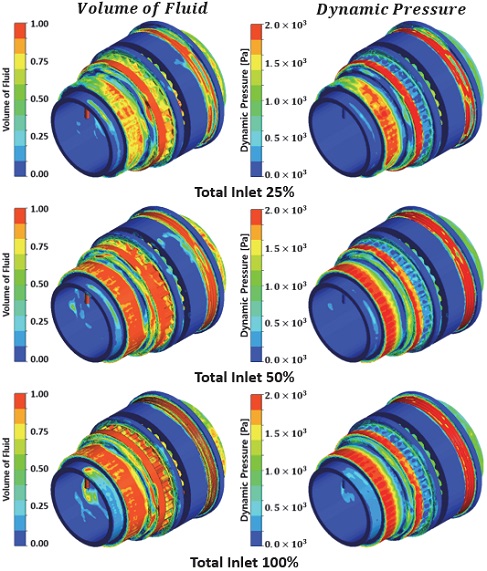
VOF and dynamic pressure in synchronizer module clearness according to inlet LPM in Table 5 (Mainshaft part 500.0 RPM, disengage gear 388.6 RPM, fluid gap 5.03 mm)
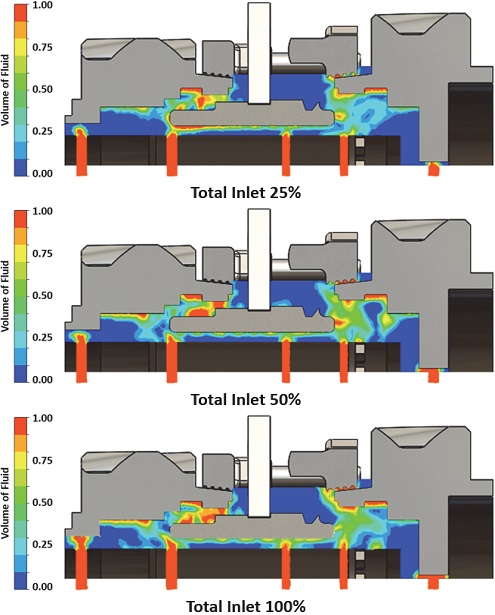
Section view VOF in synchronizer module according to inlet LPM in Table 5 (Mainshaft part 500.0 RPM, disengage gear 388.6 RPM, fluid gap 5.03 mm)
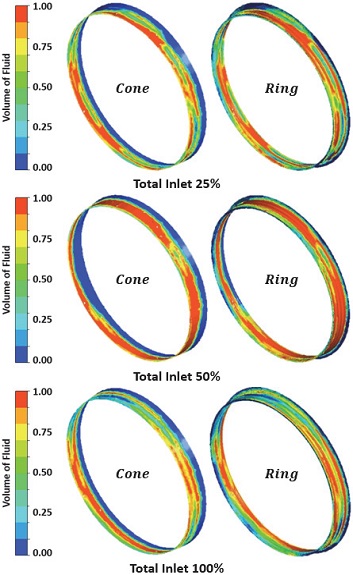
Cone and ring surface fraction of inlet LPM parameter study (Mainshaft part 500.0 RPM, disengage gear 388.6 RPM, fluid gap 5.03 mm)
Fig. 15는 Fig. 14에서 확인한 결과값을 수치화하여 그래프로 표현한 데이터이며, Fig. 16은 콘과 링 표면에서 발생하는 드래그 토크의 수치이다. 표면 분율의 경우 위에서 확인한 바와 같이 공급 유량이 줄어들면 감소하는 경향성을 보인다. 그러나 공급 유량이 25 % 또는 50 %가 된다고 해도 표면 분율이 똑같이 줄어들지는 않고 조금 둔감하게 영향을 받는 것을 확인할 수 있다. 드래그 토크도 마찬가지로 공급 유량이 줄어듦에 따라 둔감하게 작아진다.
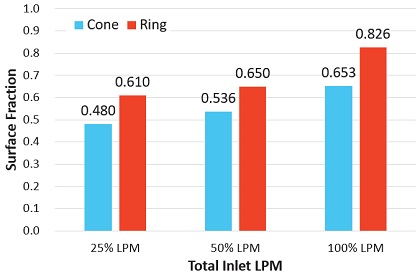
Surface fraction bar chart of inlet LPM parameter study (Mainshaft part 500.0 RPM, disengage gear 388.6 RPM, fluid gap 5.03 mm)
3.3 Fluid Gap 변화에 따른 유동해석 결과
아래의 Figs. 17과 18은 유체 간극에 따라 싱크로나이저 모듈과 단면에서 형성되는 유체 거동에 대한 VOF와 동압력의 결과값이다. 유체 간극이 줄어드는 것의 영향으로 스플리터 모듈 내부의 VOF 값이 변하는 것을 확인할 수 있으며, 유체 간극(Fluid gap)이 작아질수록 내부의 유체가 유입될 수 있는 공간이 작아지기 때문에 VOF가 줄어드는 경향성을 확인할 수 있다. 이는 간극의 변화로 내부의 공간과 그에 의한 압력 변화 등에 의한 결과로 판단된다.
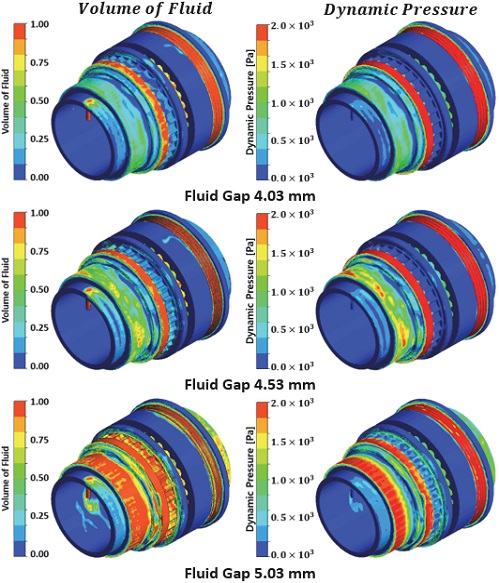
VOF and dynamic pressure in synchronizer module clearness according to fluid gap in Table 5 (Mainshaft part 500.0 RPM, disengage gear 388.6 RPM, total inlet 2.056 lpm)
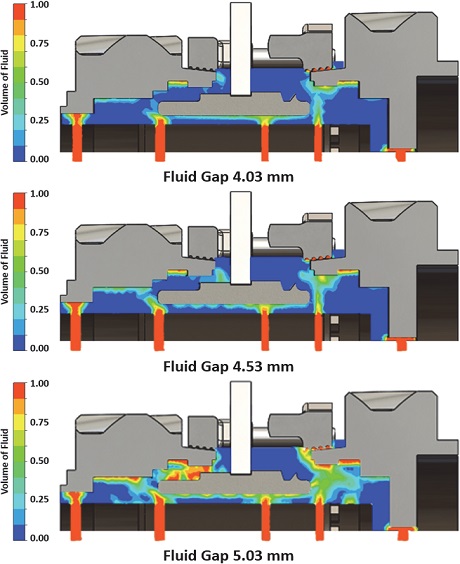
Section view VOF in synchronizer module according to fluid gap in Table 5 (Mainshaft part 500.0 RPM, disengage gear 388.6 RPM, total Inlet 2.056 lpm)
Fig. 19는 유체 간극의 변화에 따른 콘과 링의 마찰 표면의 표면 분율의 모습이며, Fig. 20은 이에 대해 수치화한 데이터다. 이전 해석 결과와 다르게 내부의 유체가 줄어드는 경향성과 일치하지 않는 것을 확인할 수 있다. 이는 간극이 줄어듦에 따라 유체가 통과할 수 있는 통로가 줄어들게 되고, 그에 의하여 콘과 링의 상대 회전속도의 영향을 크게 받아 내부에서 쉽게 빠져나가지 못하고 휩쓸리는 영향이 커지기 때문으로 판단된다. 싱크로나이저 모듈의 내부 틈새 공간이 상대적으로 더 큰 경우에는 원심력에 의해 바깥쪽인 링에 유체가 몰리며 상대 회전속도의 영향을 적게 받아 유체가 쉽게 빠져나가기 때문에 링에서의 오일이 더 많은 것을 확인할 수 있다. 그러나 틈이 좁아짐에 따라 원심력과는 상관없이 내부의 틈에 유체가 가득 차게 되어 콘의 수치가 역전한 것으로 판단된다.
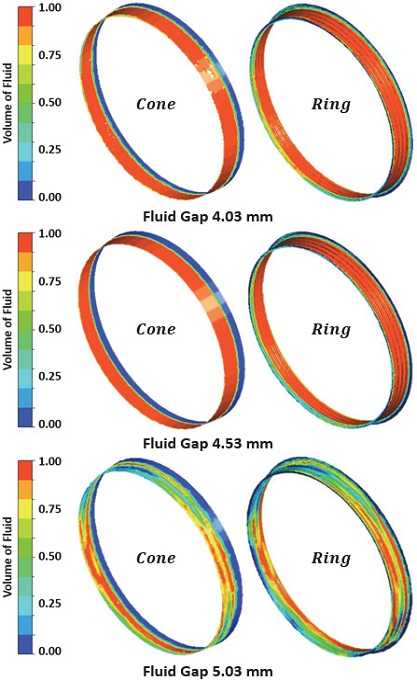
Cone and ring surface fraction of fluid gap parameter study (Mainshaft part 500.0 RPM, disengage gear 388.6 RPM, total inlet 2.056 lpm)
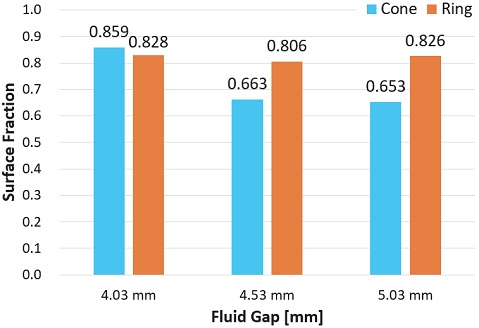
Surface fraction bar chart of fluid gap parameter study (Mainshaft part 500.0 RPM, disengage gear 388.6 RPM, total inlet 2.056 lpm)
Fig. 21은 유체 간극 변화에 따라 드래그 토크의 값을 도식화한 자료다. 드래그 토크의 경우와 마찬가지로 콘에서의 수치보다 링에서의 수치가 더 큰 것을 확인할 수 있다. 전체적인 수치는 간극이 줄어듦에 따라 커지는 것을 확인할 수 있으며, 표면 분율 값과 동일한 경향성을 가지는 것으로 보아 내부 유체에 의한 영향으로 판단된다.
4. 결 론
본 연구에서는 AMT의 스플리터 파트의 싱크로나이저를 사용하여 주축의 회전속도, 공급 유량 그리고 주요한 설계 조건인 유체 간극 3가지의 변화에 대한 콘과 링의 마찰 표면에서의 표면 분율 그리고 드래그 토크에 대한 경향성을 판단하기 위한 연구를 진행하였다.
- 1) 싱크로나이저 링의 경우 원심력의 영향으로 유체가 몰려 표면 분율이 커지게 되며, 그 영향으로 링에서 드래그 토크가 크게 발생한다.
- 2) 주축의 회전속도가 빨라지는 경우 콘과 링의 마찰 표면에서의 표면 분율은 감소하지만 그루브와 콘 각의 영향으로 드래그 토크는 증가하는 경향성을 확인하였다.
- 3) 유량이 감소하는 경우 표면 분율과 드래그 토크 모두 감소하지만, 유량 감소량보다 둔감하게 반응하는 것을 확인하였다.
- 4) 유체 간극이 작아지는 경우 내부의 유체가 빠져나가지 못해 콘과 링의 표면 분율 수치가 증가하며, 그 영향으로 드래그 토크 또한 커지는 경향성을 확인하였다.
Nomenclature
A : | area, m2 |
F : | force, N |
g : | gravitational acceleration, m/s2 |
p : | pressure, Pa |
RC : | cone radius, mm |
r : | radius, m |
TD : | drag torque, Nm |
t : | time, s |
u : | velocity, m/s |
μ : | coefficient of friction |
ρ : | density, kg/m3 |
τ : | shear stress |
θ : | cone angle, ° |
Acknowledgments
본 연구는 2021년도 정부(교육부)의 재원으로 한국연구재단의 BK21사업(5199990814084)지원, 한국연구재단(NRF #2018R1D1A1B07043950) 및 현대자동차 협력연구센터의 지원을 받아 수행한 연구입니다.
References
-
J. Y. Hwang, S. H. Jo, T. H. Wi and W. C. Son, “Development of Two Oil Pumping System for Automatic Transmission,” SAE 2014-01-1766, 2014.
[https://doi.org/10.4271/2014-01-1766]
-
H. D. Lee, S. K. Sul, H. S. Cho and J. M. Lee, “Advanced Gear-shifting and Clutching Strategy for a Parallel-hybrid Vehicle,” IEEE Industry Applications Magazine, Vol.6, No.6, pp.26-32, 2000.
[https://doi.org/10.1109/2943.877837]
- S. H. Lee, S. Y. Jang, W. J. Kim and S. Cho, “Study of Flow Behaviors in the Groove Patterns of Wet Clutch Pad,” Journal of the Korean Society of Tribologists and Lubrication Engineers, pp.108-109, 2013.
-
J. H. Ko, D. W. Kim, G. S. Lee and S. Y. Jang, “A Study on the Optimized Oil Distribution by Oil Hole Shape Design of the Main Shaft in the Automated Manual Transmission Oil Circuit,” Transactions of KSAE, Vol.29, No.9, pp.831-838, 2021.
[https://doi.org/10.7467/KSAE.2021.29.9.831]
- J. H. Ko, S. H. Kim and S. Y. Jang, “A Study on the Optimization of Oil Distribution by the Oil Circuit of an Automated Manual Transmission,” KSAE Fall Conference Proceedings, p.115, 2020.