
디젤-천연가스 이종연료 예혼합압축착화 엔진에서 디젤 2단 분사를 통한 연소 개선
Copyright Ⓒ 2021 KSAE / 186-08
This is an Open-Access article distributed under the terms of the Creative Commons Attribution Non-Commercial License(http://creativecommons.org/licenses/by-nc/3.0) which permits unrestricted non-commercial use, distribution, and reproduction in any medium provided the original work is properly cited.
Abstract
A two-stage diesel injection strategy in a diesel-natural gas dual-fuel premixed charge compression ignition (DF-PCCI) engine was investigated under a low load condition. Under this condition, the combustion efficiency becomes low because of the low equivalent ratio. This problem can be solved by supplying more diesel with low natural gas substitution rate(NGSR); however, thermal efficiency deteriorates as a result. As such, the two-stage diesel injection strategy was applied in order to delay the combustion phase at low NGSR of DF-PCCI. The two-stage injection timing was selected based on the thermal efficiency and combustion efficiency of single diesel injection at DF-PCCI combustion. By applying the two-stage diesel injection strategy, despite a slight decline of thermal efficiency, unburned hydrocarbon(UHC) and carbon monoxide(CO) were significantly reduced as compared with the single diesel injection strategy DF-PCCI.
Keywords:
Dual-Fuel premixed charge compression ignition, Natural gas, Diesel, Combusution efficiency, Two-stage injection키워드:
이종연료 예혼합압축착화, 천연가스, 디젤, 연소효율, 2단 분사1. 서 론
19세기 후반부터 시작된 환경 문제에 대한 관심은 최근 들어 그 심각성을 더하여 급격히 강화되는 수송부문의 배기 배출 규제로 이어지고 있다. 이러한 배기 규제에는 주요 온실가스(Global House Gas, GHG)로 지목되는 이산화탄소(Carbon Dioxide, CO2) 규제 뿐만 아니라 입자상물질(Particulate Matter, PM) 및 질소산화물(Nitrogen Oxide, NOx) 등의 유해물질에 대한 규제도 존재한다.1)
기존의 디젤엔진의 연소는 이러한 배기 규제들을 만족시키기 어려운 특성을 가진다. 먼저 디젤은 연료-공기의 확산에 의하여 국소적으로 농후한 영역과 고온의 영역에서 연소를 하기 때문에 입자상물질과 질소산화물의 배출이 많다.2)
기존디젤연소(Conventional Diesel Combustion, CDC)의 이러한 문제점을 해결하고자 새로운 엔진 연소기술에 관한 연구가 진행되어왔다. 초기 규제 대응 단계에서 엔진 제작사들은 주로 디젤 미립자 필터(Diesel Particulate Filter, DPF)나 선택적 환원 촉매(Selective Catalytic Reduction, SCR) 등의 후처리장치를 다는 방식으로 대응하였다. 그러나 규제가 강화되면서 이러한 후처리장치를 고도화시키는데 드는 비용이 매우 커지게 되었고 따라서 새로운 연소기술에 대한 수요가 급격히 늘어나 활발히 연구가 진행되었다.
그러한 연구의 일환으로 균일 예혼합압축착화(Homogeneous Charge Compression Ignition, HCCI), 부분 예혼합압축착화(Premixed Charge Compression Ignition, PCCI) 등의 디젤 단일연료 신연소 기술이 있다.3) 이러한 신연소 기술들의 핵심은 엔진의 연소실 내부에서 연료와 공기가 충분히 섞일 수 있도록 분사시기를 조정하는 것이다. 따라서 연료와 공기의 예혼합을 통해 연료가 희박한 조건에서 저온의 연소를 구현할 수 있어 입자상물질과 질소산화물을 크게 저감할 수 있다.4)
그러나 이러한 디젤 단일연료 신연소기술은 몇가지 치명적인 단점이 있다.3) 첫째는 연소상 제어가 어렵다는 것이다. 단일연료 신연소기술에서 연소현상은 복잡한 화학반응속도론(Chemical kinetics)에 의해 결정되나 연료와 공기의 당량비만으로 이러한 복잡한 기구(Mechanism)를 제어하는 것이 어렵게 된다. 두 번째 문제는 고부하조건에서 높은 최대압력상승률(Maximum Pressure Rise Rate, MPRR)로 운전을 할 수 없다는 것이다. 이는 디젤의 높은 반응성에 따른 현상으로, 고부하조건에서 디젤의 양이 늘어나게 되면 연소가 다발적으로 급격하게 일어나기 때문이다.
이러한 디젤 단일연료 신연소기술의 문제점을 개선하고자 나온 연소 기술이 이종연료 예혼합압축착화(Dual Fuel Premixed Charge Compression Ignition, DF-PCCI) 기술이다. 본 기술에서는 반응성이 크게 다른 두 연료를 연소실에서 예혼합시켜 압축착화를 구현함으로써 앞서 서술한 문제들을 개선한다. 이 때 저반응성 연료는 흡기 행정 중 분사되어 연소실 안에서 균질한 혼합기를 이루게 되며 고반응성 연료는 압축행정 중 연소실 내로 직접 분사되어 성층화된 혼합기를 형성한다. 이 때 고반응성 연료의 분사시기에 따른 성층화 정도에 따라 반응성제어 압축착화(Reactivity Contorolled Compression Ignition, RCCI)와 파일럿 분사 이종연료(Pilot Dual Fuel, Pilot-DF) 연소로 나뉜다. Fig. 1은 기존디젤연소 및 다양한 신연소 전략의 개념을 설명하는 개념도이다.5) 앞서 언급된 HCCI, PCCI뿐만 아니라 DF-PCCI의 두가지 전략도 나타나있다. 위의 문헌에서는 저반응성 연료로 압축천연가스(Compressed Natural Gas, CNG)를 사용하였고, 고반응성 연료로 디젤을 사용한다. DF-PCCI의 두가지 연소전략 중 상사점(Top Dead Center, TDC) 근처에서 디젤을 분사하여 디젤을 파일럿 연료, 즉 천연가스-공기 예혼합기의 착화제로서 사용하는 기술이 Pilot-DF 전략이다.6) 상사점은 연소실 내 혼합기가 최대한 압축되는 점이므로, 디젤이 분사될 때의 온도가 높다. 따라서 분사된 디젤은 짧은 착화 지연을 겪은 뒤 착화되고 주변의 천연가스-공기 혼합기로 화염이 전파되어 연소가 일어나게 된다. 반면 디젤을 -70∼ -40CAD aTDC에서 즉, 상사점보다 크게 진각된 시기에 분사함으로서 디젤을 성층화시켜 연소하는 전략이 RCCI이다.7) 디젤 분사시기인 -70∼-40CAD aTDC에서는 압축이 완전히 일어나지 않아 디젤이 착화될 수 있는 온도에 도달하지 못한다. 따라서 분사된 디젤은 착화되지 않고 천연가스-공기 혼합기와 섞이게 된다. 이후, 압축이 더 진행되어 연료-공기 혼합기에서 자발화가 일어날 수 있는 온도가 되면, 디젤이 많이 분포하여 당량비가 높은 부분에서부터 착화가 시작되어 연소가 일어나게 된다. 이 때, 디젤의 분사시기가 더 지각될수록 디젤이 섞이는 시간이 길어지게 되어 균질도가 상승하여 착화가 일어나는 고당량비 영역의 당량비가 낮아지게 된다. 즉, 디젤의 분사시기에 따라 연료-공기 혼합기의 공간적인 당량비 성층화 정도가 결정이 되고 저반응성 연료와 고반응성연료의 비율에 따라 반응성 성층화 정도도 결정된다. DF-PCCI에서는 이러한 반응성과 당량비의 성층화를 통해 제어 성능을 향상시킬 수 있다. 또한 고부하 조건에서도 고반응성 연료의 비율을 낮추고 저반응성 연료의 비율을 높임으로서 최대압력상승률을 낮춰 운전가능한 부하의 범위도 확장할 수 있다.
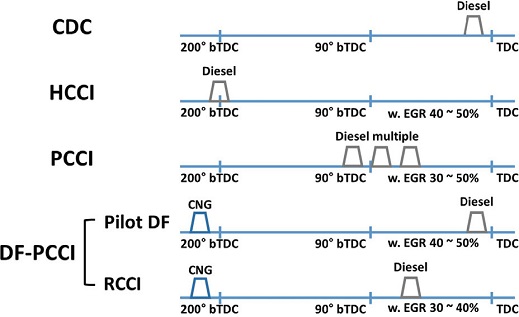
Combustion concepts of conventional diesel combustion and various advanced combustion technologies according to the fuel supply5)
그러나 DF-PCCI는 저부하조건에서 미연탄화수소(Unburned hydrocarbon, UHC)와 일산화탄소(Carbon monoxide, CO)의 배출이 증가하는 문제점이 있다.8) 이러한 연소효율의 하락문제는 저부하조건에서는 절대적인 연료의 양이 부족하여 전체 당량비가 감소하여 연소가 완전히 일어나지 못하고 소염되기 때문에 발생한다.7,8) 이러한 문제를 해결하기 위하여 흡기제어를 통해서 흡입되는 공기를 줄여서 당량비를 상승시키는 연구가 진행되었으나 흡기 제어는 펌핑 손실을 증가시켜 열효율을 악화시킨다는 한계점이 존재하였다.9)
저부하 조건에서 낮아진 당량비를 보상하기 위해서 디젤의 공급을 늘려 전체적인 반응성을 높일 경우, 반응성이 증가하여 연소효율은 향상시킬 수 있으나 연소상이 과도하게 진각되어 음의 일(Negative work)이 증가하여 전체 열효율을 하락시키게 된다.10) 이렇듯, 고반응성 연료인 디젤의 비율을 증가시킬 경우에 발생하는 과도한 연소상 진각 문제를 해결하기 위해 본 연구에서는 디젤 2단 분사 전략을 적용하였다. 먼저 디젤의 분사시기를 크게 두가지로 실험을 수행하였다. 저부하조건에서 기존의 단일 분사시기에 모든 디젤연료를 분사하던 방식을 1차 분사시기에 분사할 연료량을 줄여 2차 분사시기에 나눠 분사함으로서 연소상 진각을 방지하고자 하였다. 이를 통해 전체 혼합기의 반응성을 향상시켜 기존 이종연료 예혼합압축착화의 단점으로 지목된 미연탄화수소 및 일산화탄소 배출을 저감하는 것을 목표로 하였다.
2. 실험 장치 및 조건
2. 1 실험 장치
본 연구에서 사용된 엔진은 6L급 6기통 디젤 엔진을 실험 목적에 맞게 단기통으로 개조한 엔진이다. 자세한 제원은 Table 1에 나와 있으며 실험장치 구성은 Fig. 2와 같다. 디젤 연료는 저압, 고압 펌프를 지나 가압되어 커먼레일시스템을 통해 연소실 내로 직접 분사되며 이 때, 분사량은 연비계(733s, AVL)를 통하여 측정하였다. 천연가스는 가스 유량 제어장치(F-202AV, Bronkhorst)에 의해 제어되며 일정한 유량으로 흡기포트로 공급된다. 실린더 내로 들어오는 공기량은 가스 질량 유량계(F-106AI, Bronkhorst)를 통해 측정하였다. 디젤/천연가스 예혼합압축착화 연소 시의 실린더 내부 압력은 엔진 헤드에 설치된 엔진용 압력센서(6052C Kistler)를 통하여 측정하였다. 연소의 결과로 배기포트를 통해 나오는 연소생성물들 중 탄화수소, 일산화탄소, 질소산화물, 이산화탄소, 질소 및 산소는 배기가스 분석장치(7100D-EGR, HORIBA)로 측정하였고, 입자상물질은 스모크 미터(415s, AVL)로 측정하였다. 또한 데이터 수집 시스템(CompactRIO 9024, NI)을 이용하여 디젤 분사기를 제어하고 각종 성능 데이터와 연소 데이터를 취득하였다.
2. 2 실험 조건
본 연구에서 행한 실험 조건을 Table 2에 나타내었다. 먼저 엔진 속도는 1200 rpm으로 고정하여 실험하였다. 에너지 공급 총량(Total energy supply quantity)을 909 J/cycle로 고정하고, 천연가스 대체율(Natural gas substitution rate, NGSR)을 40, 60, 70, 80 %로 높여가며 실험하였다. 본 논문에서 천연가스 대체율은 식 (1)과 같이 열량을 기준으로 계산하였다.
(1) |
위 조건의 에너지 공급 총량은 동일한 발열량을 가지는 디젤 21.4 mg/cycle를 -10 CAD aTDC에 분사할 경우 0.4 MPa IMEP(Indicated mean effective pressure)의 부하가 나오는 양으로, 저부하 조건의 공급연료량 조건이다. 디젤의 분사압력은 기 엔진의 단일 디젤 연소 적용 시 가장 낮은 부하에서의 분사압력 조건인 60 MPa로 고정하였다. 실험은 2단계로 구성하여 진행하였다. 먼저 첫 번째로 디젤-천연가스 예혼합압축착화 연소에서 디젤의 2단 분사를 적용하기에 앞서 디젤의 1단 분사를 적용하여 천연가스 대체율을 40 %에서 80 %까지 변경하고 디젤 분사시기를 -10 CAD aTDC부터 -50 CAD aTDC까지 변경하며 RCCI(Reactivitiy Controlled Compression Ignition)와 Pilot DF(Pilot Dual Fuel) 연소 구현을 위한 대표적인 분사시기를 구해주었다. 두 번째 단계로서는 1차 분사시기를 RCCI 분사시기로 고정하고 2차 분사시기는 Pilot DF 분사시기로 분사 비율을 변경하며 실험을 진행하였다. 분사비율의 지표로서 2차 분사를 기준으로 2차 분사 비율(Ratio of sencond injection of diesel, R2nd)을 식 (2)로 정의한다.
(2) |
2차분사 비율을 0에서부터 0.1간격으로 1까지 변경하며 실험을 수행하였다.
3. 실험 결과
3. 1 디젤/천연가스 예혼합압축착화 디젤 1단 분사 실험을 통한 최대 열효율 및 최대 연소효율 운전점 파악
2단 분사 실험을 하기 전 디젤 분사를 2단 분사가 아닌 1단 분사전략을 적용하여 디젤/천연가스 예혼합압축착화 연소 실험을 수행하였다. Fig. 3과 Fig. 4는 천연가스 대체율과 디젤 분사시기(Start of injection, SOI)를 변경하며 열효율과 연소효율을 측정한 결과이다. 이 때, COV_imep limit는 연소 안정성의 지표인 Imep 변동계수(Coefficienct of variation)가 높아져 연소가 안정적으로 일어나지 못하는 것이다. 천연가스 대체율이 높아지고 디젤의 분사시기가 진각되면 저반응성 연료의 비율이 많아지고 디젤의 착화지연이 늘어나 연소가 안정적으로 일어나지 못하게 된다.7,8) 천연가스 대체율은 40 %, 50 %, 70 %, 80 %에서, 디젤 분사시기는 5CAD 간격으로 하여 실험을 수행하였다. 실험에서 최고 열효율 운전점은 천연가스 대체율 70 %, 디젤분사시기 35CAD aTDC으로 도시 열효율(Indicated Thermal Efficiency, ITE) 기준, 42.5 %의 효율을 보였다. 그러나 동일한 운전점에서 연소효율은 89.0 %로 매우 낮은 값을 보임을 확인할 수 있다. 이러한 낮은 연소효율은 저부하 운전 조건에서 연료의 절대적인 양이 부족하여 연소가 일어나지 못하고 소염되는 현상에 기인한다.7,8) 이러한 연소효율을 향상시키기 위한 전략으로는 고반응성 연료인 디젤의 비율을 증가시키는 방법이 있다.10) Fig. 4에서 연소효율의 최고점은 천연가스 대체율 40 %, 디젤 분사시기 -40CAD aTDC에서 96.5 %로 나타난다. 이 조건에서는 38.2 %로 낮은 도시 열효율이 나타나는데 이는 높은 디젤의 비율로 인해 연료-공기 혼합기의 반응성이 높아져 연소상(Combution phase)이 진각되어 음의 일이 증가하기 때문이다. Fig. 5는 천연가스 대체율과 디젤분사시기에 따른 연소상을 CA50(Crank Angle 50 %)으로 나타낸 것이다. 이 때, 연소 매개변수인 CA50은 각각의 연소로 발생된 총 열방출의 50 %에 도달하는 크랭크 각도를 말한다. 최고 연소효율점에서는 CA50이 상사점(Top Dead Center, TDC) 이전에 나타나기 때문에 대부분의 연료가 압축행정에 연소하여 음의 일을 많이 하게 되는 것이다. 반면 최고 열효율 점인 천연가스 대체율 70 %, 디젤 분사시기 -35CAD aTDC에서는 CA50이 2CAD aTDC로 나타나 음의 일을 덜하게 된다. 결과적으로 최대 열효율 점에서는 낮은 당량비에 의한 소염현상으로 인해 낮은 연소 효율(Combustion efficiency, ηcomb.)을 보이는 문제가 있고, 이러한 문제를 해결하기 위해 디젤의 비율을 증가시키면 음의 일이 증가하여 열효율이 하락하는 문제가 생기게 된다.10)
Fig. 6은 천연가스 대체율 40 % 조건으로 연료의 공급량을 고정시키고 디젤의 분사시기를 -10CAD aTDC에서 5CAD 간격으로 진각시키며 취득한 성능 및 배기 데이터이다. 열효율은 디젤 분사시기 -15CAD aTDC에서 최대(39.0 %)로 나타나며, 연소효율은 디젤 분사시기-40CAD aTDC에서 최대값(96.5 %)을 보인다. 이 운전점에서 CA50은 -8CAD aTDC로 매우 지각된 시기에 나타나는데 따라서 높은 연소효율에도 낮은 열효율을 보이게 된다.
RCCI에서는 고반응성 연료인 디젤의 성층화 정도에 따라 CA50이 변화하는데 이는 디젤의 성층화 정도가 낮고 혼합기 균질도가 높은 경우에, 국소적인 당량비와 반응성이 낮아져 더 높은 온도와 압력에서 착화가 일어나기 때문이다.7,8) 따라서 RCCI 연소에서는 디젤의 분사시기가 진각되어 디젤이 천연가스-공기 예혼합기와 섞일 시간이 늘어나면 성층화 정도가 낮아지고 연료가 균질하게 분포하여 CA50이 지각되게 된다. 이러한 CA50 지각 현상은 -35CAD aTDC부터 디젤 분사시기를 진각시킴에 따라 나타난다. 질소산화물의 배출은 디젤 분사시기 지각에 따라 -25CAD까지 증가하다가 이후 감소하며, -40CAD aTDC부터 매우 낮은 분포를 보인다. 따라서 RCCI에 의한 저온연소는 디젤 분사를 -40CAD aTDC보다 진각시켰을 때 나타난다. 입자상물질의 배출은 전반적으로 낮은 분포를 보였다. 이러한 낮은 입자상물질 배출 특성은 천연가스의 친환경적인 특성에 기인하는 것으로, 분자 구조가 단일 탄소와 4개의 수소로 이루어진 메탄이 천연가스의 주성분이기 때문이다. 탄화수소계 연료의 연소 시 Soot이라 부르는 탄소 덩어리가 형성되게 되는데 분자에 하나의 탄소만을 포함하는 메탄이 연소할 때는 이러한 탄소 간의 결합이 생성되지 않는다. 따라서 메탄을 주성분으로 하는 천연가스의 연소에서도 입자상물질의 배출이 줄어들게 된다.11)
3. 2 연소상 지각을 위한 디젤 2단 분사 적용
본 절에서는 디젤의 2단 분사를 적용하여 디젤/천연가스 이종연료 예혼합압축착화 실험을 수행하였다.12) 2단 분사의 목적은 저부하 조건에서 연소효율을 상승시키기 위해 디젤의 분율을 높였을 때, 연소상이 과도하게 지각되어 열효율이 떨어지는 문제를 해결하는 것이다. 단일 분사실험에서 최고 연소효율이 나오는 운전점은 NGSR 40 %, 디젤 분사시기 -40CAD aTDC였다. 따라서 2단 분사 실험의 NGSR 조건을 40 %로, 1차 디젤 분사시기를 -40CAD aTDC로 선정하였다. 또한 2차 분사시기는 열효율의 향상을 위하여 디젤 1단 분사실험에서 NGSR이 40 % 일 때, Pilot-DF의 최고 열효율이 나왔던 -15CAD aTDC로 선정하였다. 두 분사시기에 분사하는 디젤의 총량을 고정하고 분사의 비율을 변경하였다.
Fig. 7은 디젤의 분사비율 변경에 따른 성능 및 배기 지표의 변화를 보여준다. 2차 분사 비율을 0에서부터 1까지 0.1씩 증가시키며 데이터를 수집하였다. 그 결과 2차 분사 비율을 0에서 0.6까지 증가시키는 동안 도시 열효율은 꾸준히 증가하지만 이후 감소하는 거동을 보인다. 연소효율은 2차 분사 비율을 증가시키면 0.5까지는 94 % 이상의 높은 수준을 유지하지만 2차 분사 비율 0.6을 넘김에 따라 급격히 감소한다. 반면 2차 분사 비율을 증가시킬수록 연소상은 꾸준히 지각되는 결과를 보여준다. 연소상은 모두 상사점 이전에서 나타나므로 연소상의 지각은 음의 일을 감소시켜 열효율의 향상에 기여한다. 2차 분사 비율을 0.5까지 증가시킬 경우 연소효율이 거의 일정한 수준을 유지하는 동시에 연소상이 지각되므로 열효율이 향상되는 결과를 보인다. 2차 분사 비율이 0.6인 조건에서는 연소효율이 눈에 띄게 하락하지만 연소상 지각의 영향이 더욱 크기 때문에 열효율이 증가한다. 그러나 2차 분사 비율 0.7 이상의 영역에서는 연소효율이 매우 급격하게 하락하면서 열효율까지 크게 감소한다.
2차 분사에 의한 연소는 Pilot DF로, 이는 파일럿 연료로서 작용하는 디젤에 의한 착화를 통해 나머지 천연가스-공기 예혼합기가 화염전파를 통해 연소하는 형태의 전략이다.5,6) 따라서 당량비가 낮은 천연가스-공기 혼합기에서는 불완전연소가 발생하여 연소효율이 크게 하락한다. 2단 분사 적용 시, 2차 분사 비율이 0.6을 넘게 되면 Pilot-DF의 연소가 지배적인 기구가 되고 따라서 2차 분사 비율을 높일수록 연소효율이 하락하게 된다. 또한 Pilot-DF에서는 착화제로 쓰이는 디젤이 상사점 근처에서 고온의 연소를 하므로 질소산화물의 배출이 높다. 따라서 Pilot-DF의 연소를 일으키는 2차 분사의 비율을 높일수록 질소산화물의 배출이 증가한다. 입자상물질은 저부하조건의 절대적인 연료량 부족과 친환경연료인 천연가스의 사용으로 인하여 0.01 g/kWh 이하의 매우 낮은 배출량을 보였다.
연소효율과 열효율을 종합적으로 고려해보면 열효율이 가장 높은 2단 분사 조건은 2차 분사 비율이 0.6인 조건이나 이 경우에 다른 조건보다 눈에 띄게 낮은 93.9 %의 연소효율을 보인다. 따라서 낮은 천연가스 대체율을 통해 연소효율을 높이는 동시에 디젤 2단 분사 전략을 통해 진각된 연소상을 지각시켜 열효율의 향상을 도모하는 최적의 운전점은 2차 분사 비율이 0.5인 점인 것으로 결론 낼 수 있다.
3. 3 디젤/천연가스 이종연료 예혼합압축착화에서 디젤 2단 분사 전략 적용의 효과 분석
본 절에서는 디젤의 2단 분사를 적용한 디젤/천연가스 이종연료 예혼합압축착화 실험 결과와 디젤 1단 분사 전략과의 비교를 통해 2단 분사적용 전략 적용 시의 효과에 대하여 분석한다. 이 때 비교할 운전 조건은 1단 분사 전략의 최고 열효율 운전점과 동일 전략의 최고 연소효율 운전점, 그리고 2단 분사 전략의 열효율 향상을 위한 최적 운전점으로 총 3가지이다.
Table 3은 이 세가지 운전점의 운전조건과 성능 및 배기 데이터를 정리한 표이다. 그리고 Fig. 8은 이 세 운전점의 도시 열효율과 연소효율을 가시적으로 나타낸 그래프이다. 디젤 1단 분사 최고 열효율은 NGSR 70 %, 디젤 분사시기 -35CAD aTDC에서, 최고 연소효율은 NGSR 40 %, 디젤 분사시기 -40CAD aTDC에서 나타났다. 열효율과 연소효율을 동시에 고려하여 선정한 2단 분사 최적 운전점은 NGSR 40 %조건에서 디젤 분사시기 -40CAD aTDC, -15CAD aTDC의 비율을 5:5로 하는, 2차 분사비율이 0.5인 운전점으로 선정하였다.
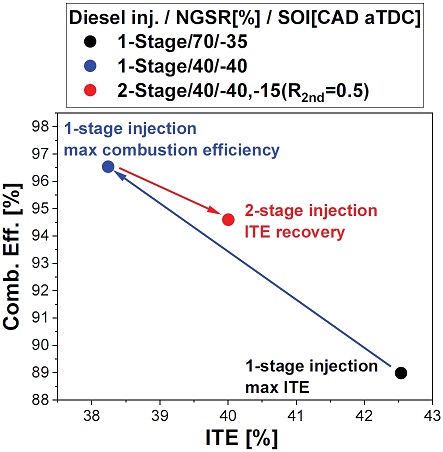
Indicated thermal efficiency and combustion efficiency of tthe main operating points of 1-stage injection and 2-stage injection for DF-PCCI
Fig. 8에서 검은색으로 나타난 점은 1단 분사 최고 열효율 운전점으로, 저부하조건으로 인해 연료가 희박한 연소를 하여 연소효율이 떨어지는 문제가 발생하였다. 이를 해결하기 위해서 디젤의 비율을 높여 연소효율을 상승시킬 수 있으나 연소상의 진각으로 열효율이 악화된다. 이러한 열효율과 연소효율의 상충관계(Trade-off)는 그래프에서 가장 높은 연소효율의 파란색 운전점에서 열효율이 매우 낮은 것을 통해 드러난다. 본 연구에서는 디젤의 2단 분사 적용을 통해 이러한 문제를 부분적으로 해결할 수 있었다. 빨간색으로 나타난 점은 디젤 2단 분사의 최적점으로 최종적으로 2단 분사를 적용하였을 때 열효율의 큰 하락 없이 연소효율을 높일 수 있었다.
Fig. 9는 이러한 세가지 운전점의 실린더 압력과 열방출율을 나타낸 그래프이다. 이를 통해 디젤 2단분사 전략에서 동일 NGSR조건의 단일 분사에 비해 연소 시점과 연소상이 지각되었음을 알 수 있다. 디젤 2단 분사 전략을 적용하였을 때의 열방출율을 살펴보게 되면 동일 NGSR의 단일 분사조건에 비해 -20CAD aTDC 근방에서 작은 열방출을 보이는 저온연소의 비율이 두드러지게 줄었음을 확인할 수 있다. 이는 디젤 연료가 나눠져 2단으로 분사되기 때문에 1차 분사시기(-40CAD aTDC)에 분사된 디젤의 양이 반으로 줄어들었기 때문이다. 2단 분사의 실린더 압과 열방출율 그래프 공통적으로 약 -10CAD aTDC에서 -5CAD aTDC사이에서 급격한 기울기의 변화가 나타나는데 이는 2차 분사에 따른 Pilot-DF연소에 의한 것으로 볼 수 있다. 따라서 디젤 2단 분사에 의해 RCCI와 Pilot-DF라는 두가지 연소 모드가 동시에 나타나는 것으로 볼 수 있다.
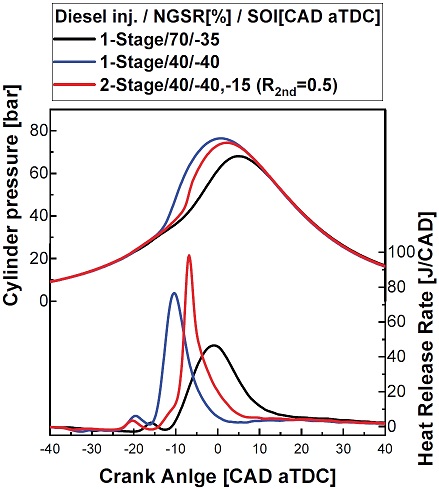
Cylinder pressure and heat release rate of the main operating points of 1-stage injection and 2-stage injection for DF-PCCI
최종적으로 Table 3에서 1단 분사 최고 열효율 운전점과 2단분사 최적 운전점을 비교해 보면, 일산화탄소의 배출은 13.7 g/kWh에서 12.7 g/kWh로 7.2 % 감소하며 미연탄화수소의 배출은 17.1 g/kWh에서 8.0 g/kWh로 약 53.2 % 감소한다. 그러나 Pilot-DF 모드에 가까워진 연소로 인하여 질소산화물은 1.5 g/kWh에서 21.3 g/kWh로 약 14 배 증가하고 입자상물질은 0.002 g/kWh에서 0.007 g/kWh로 약 3.5 배 증가한다. 이 때 입자상물질의 경우 증가한 배출량도 EURO VI 배기규제(0.01 g/kWh 미만)를 만족하지만 질소산화물의 경우 배기규제치(0.4 g/kWh 미만)를 한참 넘기는 결과를 나타내어 치명적인 문제로 작용한다. 배기가스 재순환 등의 기술을 적용하여 연소 온도를 낮추는 방식의 향후 연구가 필요할 것으로 보인다.13) 특히나 냉각된 배기가스 재순환(Cooled exhaust gas recirculation)을 적용할 경우, 연소온도를 낮추어 질소산화물의 배출을 줄일 수 있으므로 2단분사와의 동시 적용을 높은 질소산화물 배출 문제를 해결할 수 있을 것으로 예상된다.
4. 결 론
본 연구에서는 저부하 운전영역에서 디젤/천연가스 이종연료 예혼합압축착화를 구현하고 디젤 2단분사를 적용함으로서 디젤/천연가스 이종연료 예혼합압축착화의 문제점으로 지적된 미연탄화수소 및 일산화탄소 배출의 저감을 목표로 하였다.
- 1) 디젤 1단 분사 전략의 최고 열효율 운전점은 천연가스 대체율 70 %, 디젤 단일 분사시기 -35CAD aTDC로 열효율은 43.1 %였으나 89.4 %의 낮은 연소효율을 보였다. 1단 분사 전략의 연소효율을 향상시키기 위해 고반응성 연료인 디젤의 비율을 증가시키면 연소상이 진각되어 열효율이 하락하는 문제가 있다.
- 2) 열효율 하락의 원인인 진각된 연소상을 지각시켜 열효율을 향상시키기 위한 목적으로 디젤 2단 분사 전략을 적용하여 실험을 수행하였다. 이 때, 천연가스 대체율 40 %로 디젤의 비율을 높인 상태로 수행하였고 디젤의 분사시기는 1단 분사 실험 결과를 토대로 -40CAD aTDC, -15CAD aTDC로 선정하여 분사비율을 변경시켜가며 실험을 수행하였다. 수행결과, 최적 운전점은 디젤 1차 분사와 2차분사 비율이 5:5인 경우에서 나타났다.
- 3) 디젤/천연가스 예혼합압축착화 연소에서 디젤 2단 분사를 적용하면 1단 분사에 비해 열효율에 약간의 손해를 보지만 연소 효율을 약 5.6 % 포인트 상승시킬 수 있다. 그러나 질소산화물의 배출이 약 14 배 증가하는 문제가 있다.
Nomenclature
GHG : | global house gas |
PM : | particulate matter |
NOx : | nitrogen oxides |
CDC : | conventional diesel combustion |
HCCI : | homogeneous charge compression ignition |
PCCI : | premixed charge compression ignition |
MPRR : | maximum pressure rise rate |
DF-PCCI : | dual fuel premixed charge compression ignition |
RCCI : | reactivity control compression ignition |
Pilot-DF : | pilot dual fuel |
TDC : | top dead center |
CAD : | crank angle degree |
NGSR : | natural gas substitustion rate |
IMEP : | indicated mean effective pressure |
ITE : | indicated thermal efficiency |
CAD aTDC : | crank angle degree after top dead center |
SOI : | start of injection |
Subscripts
2nd : | second injection |
Acknowledgments
A part of this paper was presented at the KSAE 2020 Spring Conference
본 연구는 환경부 Global-Top Project(글로벌탑 저배기/저탄소 자동차 신연소 원천기술 개발, 2016002070001) 친환경자동차기술개발사업단의 지원에 의해 수행되었으며 이에 감사드립니다.
References
- EUR-Lex, Document 32016R0646, https://eur-lex.europa.eu/eli/reg/2016/646/oj, , 2020.
- J. E. Dec, “A Conceptual Model of DL Diesel Combustion Based on Laser-Sheet Imaging,” SAE Transactions, Vol.106, pp.1319-1348, 1997.
-
M. Krishnamoorthi, R. Malayalamurthi, Z. He and S. Kandasamy, “A Review on Low Temperature Combustion Engines: Performance, Combustion and Emission Characteristics,” Renewable and Sustainable Energy Reviews, Vol.116, Paper No.109404, 2019.
[https://doi.org/10.1016/j.rser.2019.109404]
-
H. Park, E. Shim, Y. Hwang and C. Bae, “Diesel Injection Strategy in a Premixed Charge Compression Ignition Engine Under a Low Load,” Transactions of KSAE, No.26, Vol.3, pp.295-303, 2018.
[https://doi.org/10.7467/KSAE.2018.26.3.295]
-
E. Shim, H. Park and C. Bae, “Comparisons of Advanced Combustion Technologies (HCCI, PCCI, and Dual-Fuel PCCI) on Engine Performance and Emission Characteristics in a Heavy-Duty Diesel Engine,” Fuel, Vol.262, Paper No.116436, 2020.
[https://doi.org/10.1016/j.fuel.2019.116436]
-
A. Cozzolini, D. Littera, R. Ryskamp, J. Smallwood, M. Besch, M. Velardi, H. Kappanna, D. Carder and M. Gautam, “Characteristics of Exhaust Emissions from a Heavy-Duty Diesel Engine Retrofitted to Operate in Methane/Diesel Dual-Fuel Mode,” SAE 2013-24-0181, 2013.
[https://doi.org/10.4271/2013-24-0181]
-
S. L. Kokjohn, R. M. Hanson, D. A. Splitter and R. D. Reitz, “Fuel Reactivity Controlled Compression Ignition (RCCI): A Pathway to Controlled High-Efficiency Clean Combustion,” International Journal of Engine Research, No.12, Vol.3, pp.209-226, 2011.
[https://doi.org/10.1177/1468087411401548]
-
R. Hanson, S. Kokjohn, D. Splitter and R. Reitz, “Fuel Effects on Reactivity Controlled Compression Ignition (RCCI) Combustion at Low Load,” SAE International Journal of Engines, Vol.4, No.1, pp.394-411, 2011.
[https://doi.org/10.4271/2011-01-0361]
-
E. Shim, H. Park and C. Bae, “Intake Air Strategy for Low HC and CO Emissions in Dual-Fuel (CNG-Diesel) Premixed Charge Compression Ignition Engine,” Applied Energy, Vol.225, pp.1068-1077, 2018.
[https://doi.org/10.1016/j.apenergy.2018.05.060]
-
J. Benajes, S. Molina, A. García, and J. Monsalve-Serrano, “Effects of Low Reactivity Fuel Characteristics and Blending Ratio on Low Load RCCI (Reactivity Controlled Compression Ignition) Performance and Emissions in a Heavy-Duty Diesel Engine,” Energy, Vol.90, pp.1261-1271, 2015.
[https://doi.org/10.1016/j.energy.2015.06.088]
- G. H. Choi and O. T. Lim, “The Engine Performance and Emission Characteristics of CNG/Diesel Dual-fuel Engine by CNG Mixing Ratio,” Transactions of KSAE, Vol.19, No.3, pp.38-43, 2011.
- H. Kim, W. Kim and C. Bae, “Improvement of Combustion in a Diesel-Natural Gas PCCI Engine by Diesel Split-Injection,” KSAE Spring Conference Proceedings, pp.122-123, 2020.
-
H. Park, E. Shim and C. Bae, “Expansion of Low-Load Operating Range by Mixture Stratification in a Natural Gas-Diesel Dual-Fuel Premixed Charge Compression Ignition Engine,” Energy Conversion and Management, Vol.194, pp.186-198, 2019.
[https://doi.org/10.1016/j.enconman.2019.04.085]