
벌크헤드 나사산 응력의 민감도 해석
Copyright Ⓒ 2021 KSAE / 182-08
This is an Open-Access article distributed under the terms of the Creative Commons Attribution Non-Commercial License(http://creativecommons.org/licenses/by-nc/3.0) which permits unrestricted non-commercial use, distribution, and reproduction in any medium provided the original work is properly cited.
Abstract
In this study, finite element analyses were planned to understand the sensitivity regarding the stress behavior of the thread regions of the bulkhead. A detailed sub-model representing the thread region of the bulkhead was generated automatically in CATIA. Variations of main bearing load direction and main bolt preload are selected as the sensitivity analysis variables(SAV). The variations of main bolt preload showed higher sensitivity than the main bearing load direction in the thread region of the bulkhead. In addition, the stress sensitivity in the thread region is increased when a low preload was applied to the main bolt. High sensitivity occurs with low preload because during the loading steps, the prevailing plastic deformations in hot-assembly and fire load after the dominant elastic deformation in cold-assembly amplify the stress difference among the loading steps. Therefore, main bolt preload should be applied high enough to reach the state of plastic deformation even in the cold-assembly step in order to reduce sensitivity.
Keywords:
Engine assembly, Finite element analysis, bulkhead, Submodel, Sensitivity, Thread stress키워드:
엔진 조립, 유한요소해석, 벌크헤드, 부 모델, 민감도, 나사산 응력1. 서 론
최근 개발되는 고출력, 고효율 엔진의 조립 과정에서 필수적으로 사용되는 볼트에 대한 적절한 선택 및 설계는 엔진 성능 및 내구성에 큰 영향을 미친다.1) 엔진 조립에 사용되는 주요 볼트는 실린더 헤드와 블록을 체결하는 헤드볼트, 커넥팅로드와 캡을 연결하는 볼트, 그리고 메인베어링 캡과 실린더블록을 체결하는 메인볼트로 구분할 수 있다. 고출력, 고효율을 필요로 하는 엔진 설계 과정은 엔진의 가혹한 작동환경과 이에 따른 취약부에서의 응력 집중에 의한 미세균열의 발생과 균열에 따른 파손방지를 목표로 진행되어야 한다.2)
엔진 조립에 사용되는 볼트의 초기체결하중(Preload)은 엔진 성능 및 내구성에 영향을 미친다. 그러므로 적절한 볼트 선택에 의한 초기 체결 하중의 설정과 엔진에 가해지는 하중들을 고려한 최적 조건을 만족시키는 것은 엔진 내구성 설계의 첫 단계라 할 수 있다.3) 충분한 초기체결하중을 지닌 연결부에서는 미끄러짐, 분리 그리고 피로파괴의 발생을 억제 할 수 있지만 지속적인 진동, 열, 피로에 노출이 되면 기계적 풀림이 발생하여 축력 손실이 발생한다. 불충분한 볼트의 체결하중은 엔진요소의 고장과 파손과 같은 치명적인 결과를 야기한다.4)
작은 볼트를 사용하여 무게를 줄이는 것은 엔진 연비 측면에서 유리하나 체결 후에 체결부의 기능과 내구성을 유지해야 한다. 그러기 위해서는 적절한 체결하중의 유지가 필요하며 소성역 체결(Plastic region tightening) 방법이 보편적으로 채택되고 있다.5) 체결된 볼트 이음부에 외력이 작용하면 체결 과정에서 볼트에 생성된 비틀림 응력은 감소하며, 그 결과로 소성역 상태의 체결볼트도 탄성변형을 하면서 외력을 지탱한다.6) 탄성역 상태의 체결이음부에 비해 소성역 상태 체결 이음부는 외력에 대한 저항이나 피로 강도 측면에서 장점을 지니고 있으나 외력이 작용할 때 이음부의 나사산과 같은 부분에 대한 연구가 부족한 현실이다.5)
따라서 본 연구에서는 메인 볼트와 체결되는 이음부인 엔진 벌크헤드의 나사산부분에서의 엔진 작동 하중의 변화에 따른 응력 변화와 볼트 초기체결 하중과 메인베어링 하중의 방향 변화에 따른 응력 변화 및 민감도에 대한 연구를 유한요소 해석을 사용하여 진행하였다. 해석에는 상용유한요소 프로그램인 ABAQUS7)를 사용하였으며 복잡한 형상을 지닌 나사산 부분의 정확한 응력 구현을 위하여 부 모델 기법(Submodel technique)을 사용하였다.
2. 엔진 벌크헤드 구조해석
엔진 벌크헤드(Bulkhead)는 크랭크축을 지지하는 엔진크랭크케이스 내부 구조체이다. 메인 베어링으로부터 반복적인 엔진 폭발하중이 전달되는 경로인 벌크헤드 부분은 피로에 의한 파손이 발생할 수 있는 부분 중의 한 곳이다. 하중의 반복에 의한 피로 손상의 누적은 특히 응력 집중이 발생할 수 있는 벌크헤드 노치 부분, 볼트나선부와 체결되는 벌크헤드 나선부에 파손을 발생시킬 수 있다.8)
2.1 유한요소 모델
본 연구에 벌크헤드 글로벌 모델(Global model)로 사용된 솔리드 모델은 Fig. 1과 같다. 메인 볼트는 그림과 같이 벌크헤드와 캡을 체결하는 역할을 한다. Fig. 2에는 메인베어링캡(Main bearing cap)과 볼트의 결합 모델과 벌크헤드 볼트 나선부와 볼트, 메인베어링캡 일부로 구성된 부 모델(Submodel)을 나타내었다. 글로벌 모델의 경우 열하중, 폭발하중, 조립하중이 복합적으로 작용하며 여러 파트가 조립되어 있는 복잡한 형상을 지니고 있다. 유한요소 모델링의 용이성과 접촉 해석을 고려하여 자동메시가 가능한 8절점 사면체 요소인 C3D10M요소를 사용하여 유한요소모델을 구축하였다.
부 모델의 경우는 글로벌 모델로부터 벌크헤드와 메인 베어링 캡의 일부분을 잘라서 생성하였다. 생성된 모델은 메인 볼트의 나사 산(Bolt thread)과 체결되는 벌크헤드의 나사산 부분, 메인 볼트, 그리고 메인베어링캡의 일부분을 포함한다(Fig. 2).
메인 볼트는 상용 설계프로그램인 CATIA를 이용하여 모델링 하였다.4) CATIA에서 제공하는 Formula기능을 사용하여 나사헤드 직경, 헤드높이, 나사바디 반경, 나사의 길이, 나사 산의 피치(Pitch), 나사 산의 높이, 나사 산의 리드(Lead), 나사하단부의 필렛(Fillet), 나사 산의 길이 등 9개의 치수를 패라미터로 설정하여 치수에 맞게 자동으로 모델이 생성되게 하였다(Fig. 3). 부 모델에 사용한 메인 볼트는 M10 규격을 적용하여 구축하였다.
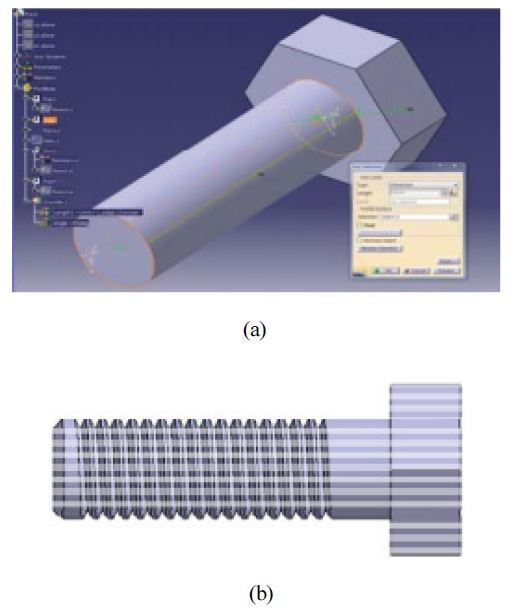
Description of automatic bolt solid model generation. (a) Parameter definition for automatic bolt solid model generation in CATIA (b) Generated bolt solid model4)
글로벌 모델과 부 모델에 대한 유한 요소 모델은전처리프로그램인 HYPERMESH를 이용하여 생성하였다. 글로벌 모델은 약 42만개의 요소와 70만개의 절점으로 구성 하였다. 부 모델에 사용된 요소는 8절점 육면체요소 (C3D8)이고 약 35만개의 요소와 39만개의 절점으로 구성하였다. 부 모델의 나사 산 부분은 응력이 집중되는 부분으로 조밀한 유한 요소로 구성하였다. Fig. 4에는 부 모델로 사용된 볼트와 벌크헤드의 나사산 부분의 조밀한 유한요소를 나타내었다.
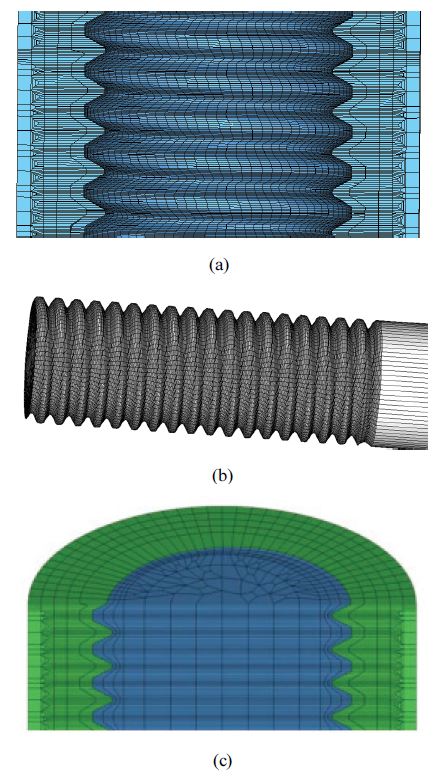
Detailed view of meshed submodel. (a) Thread area of bulkhead (b) Thread area of bolt (c) Engaged thread area between bulkhead and bolt4)
글로벌 모델 및 부 모델의 유한요소해석에 사용된 재료와 기계적 물성치는 Table 1에 정리하였으며, 소성 변형이 발생하는 벌크헤드 나사선부의 비선형성을 고려한 유한요소해석을 위해 Fig. 5와 같은 비선형 응력-변형률 곡선의 데이터를 사용하였다.9)
2.2 경계조건 및 하중
엔진 전체 모델의 거동과 응력 해석의 결과를 바탕으로 벌크헤드의 경계 조건을 다음과 같이 적용하였다.10) 벌크헤드의 후면은 면 수직방향으로 고정하였으며, 벌크헤드의 상부면은 폭발 하중 작용 시에 면 수직방향으로 고정하였다. 또한, 강체 운동(Rigid body motion)을 제거하기 위하여 벌크헤드 상부 2위치에서 2 절점을 수평 방향으로 고정하고, 1절점은 수직방향으로 고정하였다(Fig. 6). 부 모델은 벌크헤드 글로벌 모델과의 경계에서의 변위결과를 경계 조건으로 사용하였다.
글로벌 모델에서의 접촉 조건은 블록과 메인베어링캡 접촉면, 저널 베어링과 메인 보어사이의 접촉면에 적용하였으며 미세한 미끄러짐을 고려하여 Small sliding 접촉 조건을 사용하였다. 부 모델의 접촉조건도 Small sliding 접촉을 적용하였으며 접촉면은 체결되는 볼트 나사산과 벌크헤드 나사산 사이에 설정하였다.
하중조건은 조립하중, 열하중, 메인 베어링에 작용하는 폭발 하중으로 구성된다. 체결 시 발생하는 조립하중은 다음과 같이 분류된다.
- ① 벌크헤드와 메인베어링캡 측면 억지 맞춤 하중 (Press-fit)
- ② 메인보어 베어링 크러쉬 (Bearing crush) 하중
- ③ 메인볼트 체결하중
조립 하중 후에는 엔진 작동에 의한 열 하중과 엔진 폭발 하중에 의한 동적 하중이 적용된다. 유한요소 해석에 사용된 하중 순서는 Table 2에 나타내었다.
2.3 응력 해석 결과
글로벌 모델에 나타나는 조립하중, 열하중, 폭발하중의 응력 분포는 Fig. 7과 같다. 이 때 적용되는 하중은 중첩 상태이다. 조립 하중이 가해진 후 이미 벌크헤드와 메인베어링캡에는 소성변형이 발생함을 보여준다. 열하중이 가해진 후에는 응력분포 형상이 조립하중 상태와 유사하게 나타난다. 이는 소성변형이 발생 후 열하중에 의하여 응력 재분포가 발생하지만 그 정도가 크지 않음을 나타낸다. 마지막으로 폭발하중에 의해 메인 베어링부에 가해진 하중은 메인보어 주위의 응력 값을 증가하게 함을 알 수 있다.
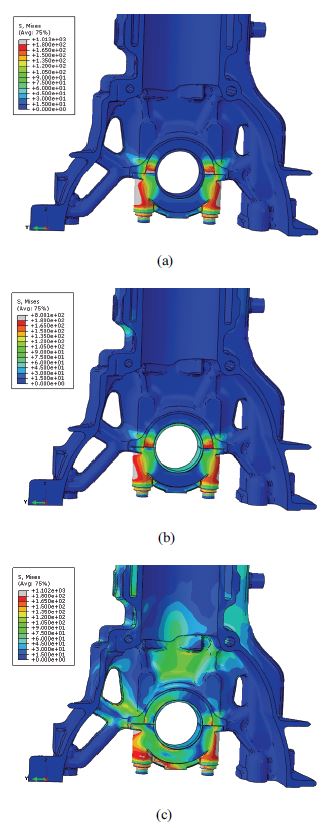
Contour plot of Von-Mises stress with 35000 N bolt preload and 326 degrees of main bearing angle. (a) Cold-assembly (b) Hot-assembly, (c) Fire load
글로벌 모델에서는 Fig. 7과 같이 전체적인 변형양상이나 응력이 집중되는 부분을 확인할 수는 있지만 주요 파손 예상 부위에서의 상세 응력은 예측이 힘들다. 그러므로 벌크헤드의 주요 예상 파손 부위인 벌크헤드 나사산 부분에서의 응력 분포 및 상세 응력값을 확인할 수 있는 부 모델의 생성이 필요하다.
Fig. 8에서는 부 모델에서 사용한 메인볼트의 응력 분포를 나타내었다. 35000 (N)의 초기 체결하중이 가해진 경우에는 볼트 조립만으로 이미 메인 볼트의 응력 값은 항복에 가깝게 증가하며 열하중, 폭발하중에서도 비슷한 응력 분포를 나타낸다. 볼트 나사산에서 발생하는 응력분포를 관찰하면 대부분의 하중은 나사산 시작 부분에서 지탱이 되며 그 부분에서 높은 응력이 발생함을 알 수 있다. 반면에 10000 (N)의 초기 체결하중이 가해진 경우에는 소성 변형이 거의 발생하지 않으며 마지막 하중 단계인 폭발하중의 경우에 나사산 시작 부분에서 소성 변형이 관찰되었다.
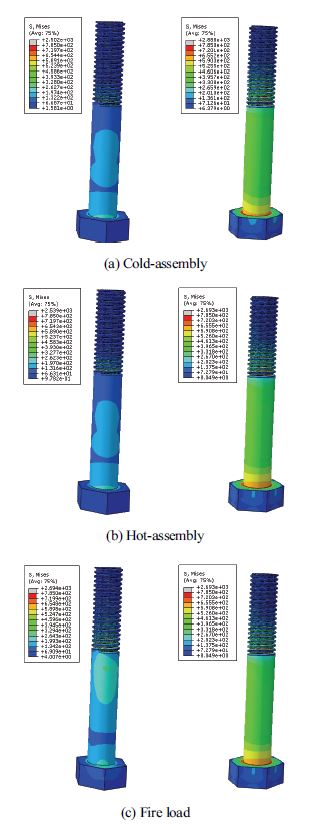
Contour plot of Von-Mises stress of main bolt. (Left: 10000 N bolt preload, 326 degrees of main bearing angle, Right: 35000 N bolt load, 326 degrees of main bearing angle) (a) Cold-assembly (b) Hot-assembly (c) Fire load
Fig. 9에서는 볼트와 체결된 벌크헤드 나사산 부 모델에서의 응력 분포를 나타내었다. 조립 하중이 가해진 후 이미 나사산 부분의 응력 값은 항복강도를 넘어 소성변형이 나사산 시작 부분에서 나타나며 열하중, 폭발하중에서도 비슷한 응력 분포를 나타낸다. 열하중이 가해지면 소성 영역은 확장하며 폭발하중이 작용하면 다시 조립하중 작용 시와 유사한 응력 분포를 나타낸다.
3. 민감도 해석
3.1 해석 변수 설정
벌크헤드 나사산의 노치 부분에서는 기하학적 형상으로 인하여 응력 집중이 발생하기 용이하며 볼트 나사산 부분과 접촉이 발생한다. 또한 볼트에 비해 상대적으로 강도가 낮으므로 균열 발생과 파손이 발생하기 쉬운 위치이지만 여러 제한으로 인해 수치적인 응력 계산이 상당히 까다로운 부분이다. 또한 여러 가지 제약에 의하여 실험적으로 응력 값을 얻는 것도 용이한 일은 아니다.
본 연구에서는 이러한 한계를 극복하고자 부 모델을 이용한 방법을 사용하여 나사산 부분에서의 자세한 응력 값을 계산하고자 하였다. 또한 2종류의 민감도 해석 변수(SAV, sensitivity analysis variables)를 설정하여 벌크헤드 나사산 부분에서의 응력 민감도에 대한 해석 및 분석을 하고자 하였다. 볼트에 작용하는 초기체결하중은 체결 방법 및 크기에 따라서 볼트의 피로파손 및 체결부의 피로 파손에 영향을 미친다.11) 또한 벌크헤드 나사산 부분의 응력은 계산된 메인베어링 하중의 방향의 변화에 대한 영향을 받을 것으로 예측이 된다. SAV는 위에서 언급한 볼트 초기체결하중과 메인베어링 하중 방향을 선택하였고 각각의 변수의 수준은 4수준, 3수준을 설정하였다(Table 3).
3.2 해석 변수 수준 배열표
설정한 SAV와 수준을 고려하여 Table 4와 같이 총 12번의 해석을 설정하였다. 민감도 해석은 SAV의 수준 변화에 따른 벌크헤드 나사산 부분에서의 응력 변화 민감도를 측정하여 반응 값에 대한 SAV의 영향을 파악하고자 하는 것이 주요 목적이다. 볼트 초기체결하중의 수준은 볼트의 탄성 변형이 예측되는 10,000 (N), 소성 변형이 예측되는 35,000, 40,000, 45,000 (N)으로 설정하였고 메인베어링 하중 방향은 기준 방향인 326°를 기준으로 4도씩 증감하여 322°, 330°로 3 수준을 설정하였다. 메인베어링 하중의 크기는 모든 해석에 25,400 (N)을 적용하였다.
3.3 민감도 해석결과
Figs. 11, 12에는 볼트 초기체결하중 변화에 따른 벌크헤드 나사산부분에서의 응력 분포를 나타내었다.
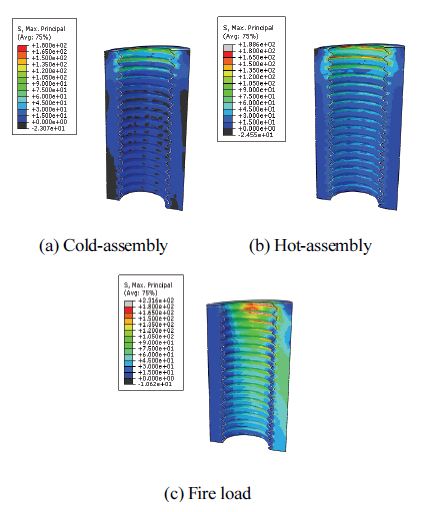
Contour plot of max principal stress of bulkhead thread with 10000 N bolt preload and 326 degrees of main bearing angle
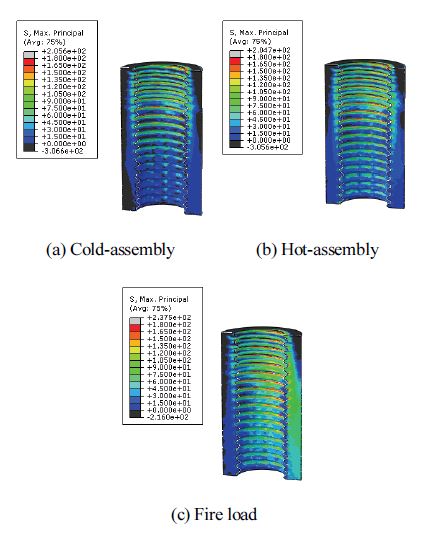
Contour plot of max principal stress of bulkhead thread with 45000 N bolt preload and 326 degrees of main bearing angle
10,000 (N), 45,000 (N)의 볼트 초기체결하중이 적용된 경우를 비교하면 조립하중(Cold-assembly)에서는 응력 분포의 형상이 상이하게 나타난다. 10,000 (N)의 경우는 탄성 변형이 주를 이루고 45,000 (N)의 경우는 소성 변형이 주를 이룬다. 열하중(Hot-assembly)과 폭발하중(Fire load)이 적용되면 모든 볼트 초기체결하중에서 소성 영역이 확산된다. 응력분포는 45,000 (N)인 경우에 나사산 전체에 대해서 점진적인 확산 양상을 보이나 10,000 (N)의 경우에는 부분적인 응력 피크가 나타남을 보인다.
Figs. 13~16에서는 메인베어링 하중 방향 변화에 따른 벌크헤드 나사산 부분에서의 응력 분포를 나타내었다. 먼저 Figs. 13, 14 에서는 탄성 변형이 예측되는 볼트 초기체결하중 10,000 (N)이 적용된 상태에서 메인베어링 하중 방향을 322°, 330° 로 변화를 주었을 때의 결과를 나타내었다.
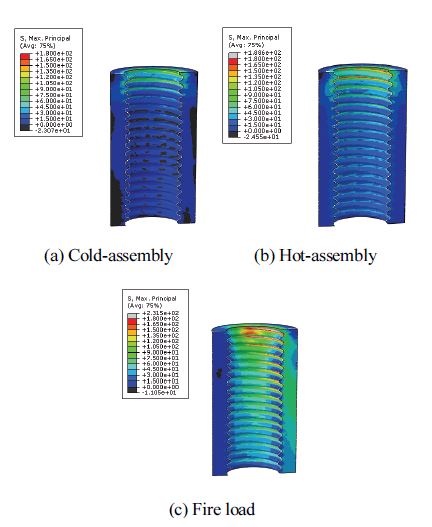
Contour plot of max principal stress of bulkhead thread with 10000 N bolt preload and 322 degrees of main bearing angle
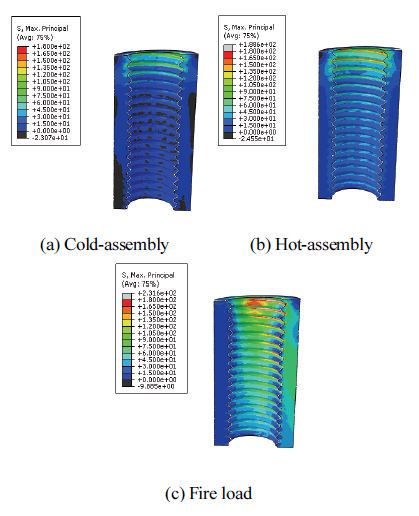
Contour plot of max principal stress of bulkhead thread with 10000 N bolt preload and 330 degrees of main bearing angle
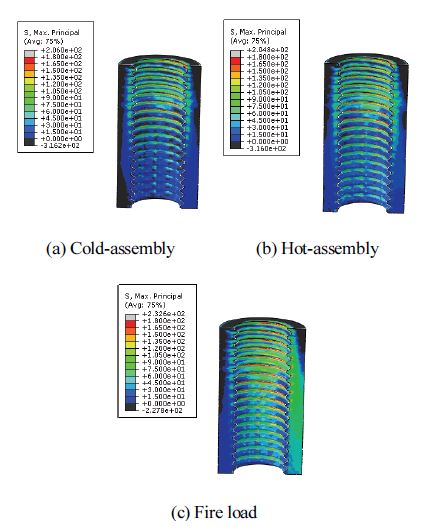
Contour plot of max principal stress of bulkhead thread with 45000 N bolt preload and 322 degrees of main bearing angle
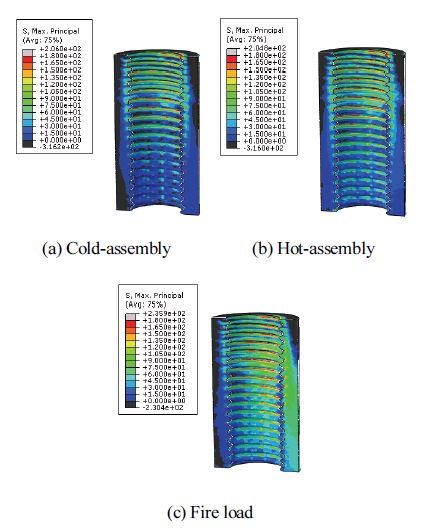
Contour plot of max principal stress of bulkhead thread with 45000 N bolt preload and 330 degrees of main bearing angle
모든 하중 단계에서의 벌크헤드 나사산 부분에서의 응력 분포는 유사한 형태를 나타낸다. 그러므로 메인베어링 하중 방향 변화에 따른 응력 민감도는 낮은 수준이 예측된다.
Figs. 15, 16에서는 소성 변형이 예측되는 볼트초기체결하중 45,000 (N)이 적용된 상태에서 메인베어링 하중 방향을 322°, 330°로 변화를 주었을 때의 결과를 나타내었다. 모든 하중 단계에서의 응력 분포를 비교하면 거의 유사한 형태를 나타내어 메인베어링 하중 방향 변화에 따른 벌크헤드 나사산 부분에서의 응력의 민감도는 높지 않음을 예측할 수 있다.
Fig. 17의 선도에서는 폭발하중 단계에서 최대 주응력 값을 나타내는 절점을 선정하여 조립하중, 열하중, 폭발하중 단계에서의 최대 주응력 값의 변화를 도시하였다. 45,000 (N)의 볼트 초기체결하중을 적용하고 메인베어링 하중 방향 방향을 변화시켰을 때의 최대 주응력 값은 거의 변화가 없어 메인베어링 하중 방향 방향에 대한 응력 민감도는 매우 낮게 나타난다(Table 6).
Fig. 18의 선도에서는 326°의 메인베어링 하중 방향을 유지하고 볼트 초기체결하중을 변화시켰을 경우의 각각의 하중 단계에 대한 최대 주응력 값의 변화를 도시하였다.
조립하중 단계에서 가장 큰 응력 민감도를 나타내고 그 다음은 열하중 그리고 폭발하중 순으로 민감도가 감소하였다. 벌크헤드 나사산 부분의 응력은 볼트 초기체결하중의 크기 변화에 상당히 민감함을 알 수 있었고 다른 메인베어링 하중 방향 (322°, 330°)도 같은 경향을 나타내었다.
마지막으로 Figs. 17, 18 생성 시에 사용한 응력 값을 이용하여 민감도 값을 계산하였다. 민감도를 계산할 때 기준값은 Fig. 17의 경우는 326°를 사용하였고 Fig. 18의 경우는 35,000 (N)을 사용하여 계산하였다. 민감도는 기준값에 대한 각 경우의 변화량의 비(Ratio)로 정의하였다.
4. 결 론
본 연구에서는 유한 요소 해석을 이용하여 메인 볼트와 체결되는 벌크헤드 나사산부분의 응력 분포 및 SAV 변화에 따른 민감도 해석을 수행하였다.
벌크헤드 나사산 부분은 주요 파손 위치이지만 일반적으로 사용되는 벌크헤드 모델의 나사산은 원기둥 형태로 볼트와 절점을 공유하므로 나사산에서 발생하는 응력 집중과 접촉조건을 나타낼 수 없어서 실제 발생하는 응력과 유사한 값을 구현하는 것은 어려움이 있었다.
이에 본 연구에서는 실제 나사산 형상, 탄소성 물성치, 접촉 조건을 적용한 부 모델을 개발하여 나사산 부위의 기계적 거동을 실제와 가깝게 구현하고자 하였다. 유한 요소 해석을 바탕으로 민감도 해석을 수행하여 아래의 결론을 도출하였다.
- 1) SAV로 설정된 볼트 초기체결하중의 크기와 메인베어링 하중 방향 중에 벌크헤드 나사산 부분의 응력은 볼트 초기체결하중의 크기 변화에만 민감함을 나타내었다.
- 2) 상온 조립과정(Cold-assembly), 열 하중 (Hot-assembly), 폭발 하중 (Fire load))에서의 민감도는 탄성 변형이 예측되는 낮은 볼트 초기체결하중(10000 (N))의 경우가 소성 변형이 예측되는 높은 볼트 초기체결하중(35000 (N), 40000 (N), 45000 (N)) 경우들보다 훨씬 높은 값을 나타내었다.
- 3) 낮은 볼트 초기체결하중을 가한 벌크헤드의 경우에도 열하중, 폭발하중이 작용하면 응력 분포 양상이 탄성영역에서 소성영역으로 변화함을 알 수 있었다.
- 4) 낮은 볼트 초기체결하중에 의한 체결은 응력의 민감도를 증가시킨다. 이는 조립하중과 열하중, 조립하중과 폭발하중 간의 응력 차이가 높은 볼트 초기체결하중에 의한 체결에서보다 크기 때문이라고 판단된다.
- 5) 피로파손 방지 측면에서는 민감도가 낮은 것이 유리하므로 적절한 볼트 초기체결하중을 적용하여 벌크헤드 나사산 부분에 소성변형을 유지하는 것이 피로파손에 유리할 것이다.
- 6) 개발된 해석 평가 방법은 향후 피로해석을 진행하여 실제 엔진 파손을 방지할 수 있는 방안에 사용될 수 있을 것이다.
References
- B. H. Lee, B. K. Kang and C. H. Chung, “A Study on Fatigue Bolt Joint using Finite Element Analysis,” KSAE Spring Conference Proceedings, pp.205-209, 2012.
- N. H. Cho, S. U. Lee, S. K. Lee and S. H. Lee, “Finite Element Analysis of Thermal Fatigue Safety for a Heavy-Duty Diesel Engine,” Transactions of KSAE, Vol.12, No.1, pp.122-129, 2004.
- S. S. Cho, H. Chang and K. W. Lee, “Procedure for Computer-Aided Preload Selection of Engine Connecting Rod Bolts,” Int. J. Automotive Technology, Vol.8, No.3, pp.319-325, 2007.
- T. H. Lee, J. J. Park and C. Yang, “A Study on the Bolt-thread Using Sub-modeling,” KSAE Annual Conference Proceedings, pp.1055-1056, 2019.
- S. S. Cho and C. S. Shin, “Finite Element Analysis of Mechanical Behavior of Bolt Tightened in Plastic Region,” Transactions of KSAE, Vol.18, No.3, pp.37-42, 2010.
-
J. Newnham and L. Curley, “Bolted Joints Under Tensile Service Loads: The Effect of Torsion in the Bolt on In-Service Clamping Loads,” Journal of Mechanical Design, Vol.115, No.1, pp.36-40, 1993.
[https://doi.org/10.1115/1.2919321]
- ABAQUS Users Manual, Ver.6.13, HKS, 2013.
- C. Yang and M. Han, “Durability Improvement of Engine Bulkhead by Adjusting Design Parameters,” Transactions of KSAE, Vol.19, No.2, pp.111-116, 2011.
- C. Yang, Cyclone V6 3.5L Bulkhead & Main Bearing Cap Design Analysis, Ford Internal Report, 1999BED-D090, 2000.
- C. Yang and M. Han, “Finite Element Analysis of Engine Cylinder Block and Main Bore for Reliable Design,” Transactions of KSAE, Vol.13, No.4, pp.39-48, 2005.
- R. Juvinall and K. Marshek, Fundamentals of Machine Component Design 3rd Edn., John Wiely & Sons, Inc., New York, 1999.