
타이어 저압감지를 위한 타이어 공진 주파수 추정


Copyright Ⓒ 2019 KSAE / 168-03
This is an Open-Access article distributed under the terms of the Creative Commons Attribution Non-Commercial License(http://creativecommons.org/licenses/by-nc/3.0) which permits unrestricted non-commercial use, distribution, and reproduction in any medium provided the original work is properly cited.
Abstract
Indirect tire pressure monitoring system(i-TPMS) monitors the inflation pressures in pneumatic tires by using wheel speed signals acquired from the anti-lock braking system(ABS). Frequency analysis and wheel radius analysis are performed at the same time in order to monitor the tire pressures indirectly. The resonance frequency of the tire torsional vibration decreases as the tire pressure decreases. It is necessary to estimate the resonance frequency in order to detect a reduction in tire pressure. This paper discusses the method of estimating the resonance frequency with the rotational wheel speed signal. First, the toothed wheel error of the wheel speed sensor and the wheel speed corrected with the toothed wheel error are calculated from the wheel speed signals. The engine noise caused by the explosion in the four-stroke of engine is eliminated by the notch filter, which is designed by using the engine rotational speed. Finally, the resonance frequency is evaluated via model parameter estimation based on the autoregressive(AR) model. Vehicle tests have been conducted in order to evaluate the proposed estimation method of resonance frequency. The findings of the vehicle test have shown that the proposed method provides satisfactory performance for the warning indication of tire pressure loss.
Keywords:
Resonance frequency estimation, Indirect tire pressure monitoring system키워드:
공진주파수 추정, 간접식 TPMS1. 서 론
차량 주행 시 적정 수준 이하의 타이어 공기압은 타이어 수명 및 연비뿐 만 아니라 차량의 핸들링 성능을 저하시킨다. 따라서, 타이어 공기압을 적정 수준으로 유지하는 것은 경제적인 측면뿐만 아니라 운전자의 안전 측면에서도 매우 중요하다. 하지만, 적정 공기압 대비 30~40 % 수준의 공기압 감소가 발생한 경우 육안으로 저압 여부를 분별하는데 어려움이 있다. TPMS는 실시간으로 타이어의 공기압 상태를 모니터링 하여 운전자에게 타이어의 저압여부를 알려주는 시스템이며, Table 1과 같이 미국, 유럽, 중국 및 한국 등 세계 주요 국가에서는 TPMS의 장착이 의무화되고 있다.1)
TPMS는 감지 방식에 따라 크게 직접식 TPMS와 간접식 TPMS 두 개로 분류된다. 직접식 TPMS는 타이어 내에 센서를 장착하여 온도 및 공기압을 직접 측정하는 방식으로, 측정 공기압이 임계값 이내인 경우 저압으로 판단하여 운전자에게 타이어 저압 경보를 제공한다. 반면에, 간접식 TPMS는 ABS가 탑재된 차량 기준으로 별도의 센서 추가 없이 4개의 휠속 센서로부터 측정한 신호를 이용하여, 다음과 같은 2가지 방법으로 타이어의 저압 여부를 판단한다.
일반적으로 타이어 공기압의 감소가 발생하면, 해당 타이어의 회전반경의 감소하며 정상 공기압인 휠 대비 회전속도가 증가된다. 따라서 차량의 4개 휠속 간의 상대비교를 통해 각 타이어의 회전반경 분석을 할 수 있으며, 이는 1~3개 타이어에 공기압 감소가 발생한 경우 저압여부를 감지하는데 유효하게 사용된다.2) 하지만 4개의 타이어가 모두 동일하게 공기압이 감소한 경우 회전반경의 상대 분석을 통해 타이어의 저압을 감지할 수 없으며, 이 때 저압감지를 위해서는 다른 방안이 필요하다. 타이어의 공기압이 감소하게 되면 타이어의 회전방향 강성이 감소하며, 이는 타이어의 회전방향 공진 주파수 감소를 야기한다. 따라서 측정된 휠속을 이용하여 타이어의 회전방향 공진 주파수를 추정하여 정상압 상황에서의 공진 주파수와 비교를 통해 저압여부를 판별할 수 있으며, 이를 통해 4개 타이어의 저압여부를 판별할 수 있다.
2. 본 론
본 논문은 간접식 TPMS의 4휠저압 감지를 위한 타이어 공진 주파수 추정기법에 대해 서술하였다. 타이어 공진 주파수는 Fig. 1과 같이 총 6단계를 걸쳐 추정할 수 있다. 또한, 정확한 공진 주파수 추정을 위해 차량의 정차시, 급가속시, 제동시, 기어단수 변화 시 그리고 임계값 이상의 가속도 및 요속도를 발생하는 가속 및 선회주행 시 주파수 추정은 예외처리 하였다.
2.1 톤휠 오차 연산
Fig. 2는 Anti-lock Braking System(ABS)의 전형적인 휠속 센서를 나타낸다. 이 휠속 센서는 일정시간 동안 측정된 Rising 혹은 Falling 펄스 개수와 각각의 펄스간 발생시간(펄스카운터)를 측정한다. 이상적인 경우, 휠속 센서의 모든 톤휠의 각도는 동일하지만, 실제 차량에서는 Fig. 2와 같이 제조산포에 의한 각 톤휠의 오차각(δi)이 존재한다. 이 오차각을 보정하지 않고 연산한 휠속을 이용하여 공진 주파수를 추정할 경우, 톤휠 오차에 의한 주기적인 노이즈가 발생한다.3)
각 톤휠의 회전속도(ωi)는 휠속 센서로부터 측정한 펄스카운터(Δti)를 이용하여 식 (1)과 같이 연산할 수 있다.
(1) |
식 (1)에서 α는 톤휠각, δ는 톤휠오차, i는 톤휠 인덱스, 그리고 N은 총 톤휠 개수를 나타낸다. 또한, 1회전 평균 휠속()은 식 (2)와 같이 연산할 수 있다.
(2) |
식 (2)에서 는 1회전 평균 펄스카운터를 나타낸다. 각 톤휠의 오차는 타이어 1회전동안 모든 톤휠의 속도는 동일하다는 가정하에 식 (1)과 식 (2)로부터 식 (3)과 같이 연산하였다.
(3) |
2.2 보정 휠속 연산
평균 톤휠오차()는 앞서 연산한 톤휠오차에 식 (4)와 같은 평균 필터를 적용하여 연산할 수 있다. 각 톤휠의 오차 보정 휠속은 평균 톤휠오차를 이용하여 식 (5)와 같이 연산하였다.
(4) |
(5) |
Fig. 3(a)는 실차시험 시 측정한 펄스카운터를 나타낸다. 본 연구에서 펄스카운터 및 펄스 개수는 5 ms 마다 측정하였다. Fig. 3(b)~(c)는 첫번째 및 열번째의 톤휠의 톤휠오차와 평균 톤휠오차를 나타낸다. 공진 주파수 연산이 예외처리 되는 경우, 평균 톤휠오차는 초기화 하였다. Fig. 3(b)~(c)으로부터 평균 톤휠오차가 일정값으로 수렴되는 것을 확인할 수 있다. Fig. 3(d)는 톤휠오차가 보정된 톤휠별 휠속을 나타낸다.
2.3 선형보간 휠속
앞의 두 단계를 거쳐 휠속 센서에서 펄스카운터가 측정될 때마다 휠속을 연산하였다. 이 휠속은 펄스카운터가 측정될 때마다 연산하기 때문에 일정한 샘플링 시간을 갖지 않는다(이벤트 도메인). 하지만, 다양한 필터 및 파라미터 추정기법을 적용하기 위해서는 일정한 샘플링 시간을 갖는 휠속이 요구된다(타임 도메인). 이를 위해 Fig. 4와 같은 선형보간법을 적용하였다.
일정한 샘플링 시간(Ts)을 갖는 휠속(ω(k))은 각 톤휠의 휠속(ωi)으로부터 식 (6)과 같이 연산할 수 있다. 본 연구에서 샘플링 시간은 2 ms으로 선정하여 선형보간 휠속을 연산하였다.
(6) |
식 (6)에서, Δti=Ti―Ti―1은 펄스카운터를 나타내며, R(k)=t(k)-Ti는 현재 톤휠 휠속의 선형보간 완료까지 남은 시간을 나타낸다. Fig. 5는 선형보간 휠속 연산의 순서도를 나타낸다.
2.4 Band-Pass 필터링
Table 2는 차량동역학 별로 발생되는 주파수 범위를 나타낸다.3) 타이어의 회전 진동은 40~50 Hz 범위에서 발생되기 때문에, 30~60 Hz의 Band-Pass 필터를 적용한 휠속 신호를 이용하여 타이어 공진 주파수를 추정하였다. 본 연구에서 Band Pass 필터는 Butterworth 방식으로 12차로 설계하였다.4)
2.5 엔진 노이즈 제거
엔진 4행정 중(흡입-압축-폭발-배기) 폭발에 의해 차체 진동이 발생한다. 4기통 엔진의 경우, 엔진 크랭크축 2회전 시 4번의 폭발행정이 발생하므로 엔진 RPM(ωe)으로부터 폭발행정에 의한 엔진 주파수(fe)를 식 (7)과 같이 연산할 수 있다.
(7) |
이 엔진 주파수가 30~60 Hz에 존재하는 경우, 타이어 회전방향 진동에 영향을 미쳐 Band-Pass 필터링된 휠속으로부터 정확한 공진 주파수를 추정하는 것이 불가능하다. 본 연구에서는 Fig. 6과 같은 방법으로 엔진 폭발에 의한 노이즈를 제거하였다.5)
우선 식 (7)의 엔진 주파수에서의 노이즈 제거를 위한 노치 필터를 식 (8)과 같이 설계하였다. 엔진 주파수가 30~60 Hz 내에 존재하는 경우, 이 노치 필터를 Band-Pass 필터링 된 휠속에 적용하였다.
(8) |
식 (8)에서 w0=2π⋅Ts⋅fe 는 노치 주파수, 그리고 ρ는 노치필터의 Rejection Width 설계 파라미터를 나타낸다. 타이어 공진 주파수 추정을 위한 필터링 휠속(y)은 식 (9)와 같이 노치 필터의 입력과 출력의 가중치 합으로 연산하였다.
(9) |
식 (9)에서 ωband는 Band-Pass 필터 적용 휠속, ωNotch는 노치 필터 적용 휠속, 그리고 γ는 가중치를 나타낸다. γ는 차량의 변속기 타입에 따라 발생되는 엔진 노이즈 크기에 비례하여 설계하였다.
Fig. 7과 Fig. 8은 엔진 RPM에 따른 Band Pass 필터와 노치 필터가 적용된 휠속 및 필터가 적용된 휠속들의 Fast Fourier Transform(FFT) 분석 결과를 나타낸다. FFT 분석을 통해 Band Pass 필터링 휠속에서 엔진 주파수 영역에서 노이즈 개입을 확인할 수 있으며, 제안한 노이즈 제거 방안을 적용함으로써 엔진 노이즈가 제거됨을 확인할 수 있다. 노치 필터는 정적 노치필터를 적용하였기 때문에, 일정시간 동안에 엔진 RPM이 임계값 이상의 변동이 있는 경우 예외처리하였다.
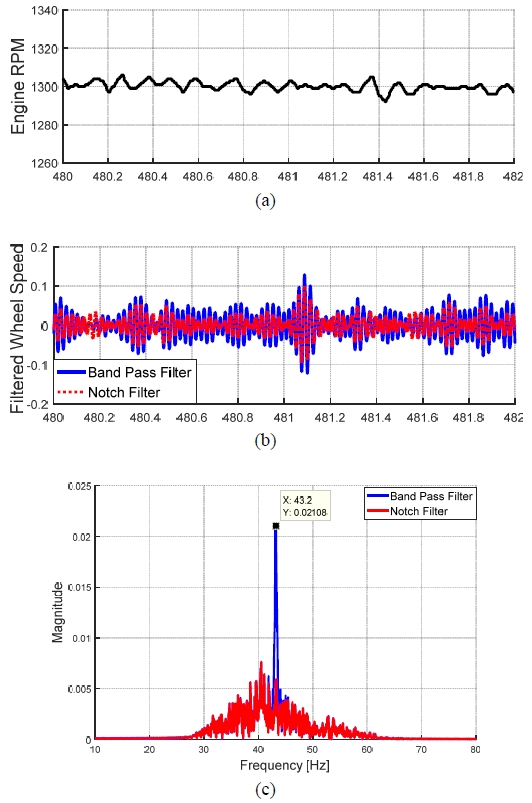
Frequency Analysis with Engine RPM = 1300 (a) Engine RPM (b) Filtered wheel speed [radian/sec] (c) FFT Analysis
2.6 공진 주파수 추정
본 연구에서는 공진 주파수 추정을 위해 식 (10)과 같은 2차 Auto-Regressive 모델 (AR 모델)을 기반으로 하여 모델 파라미터를 추정하였다.6)
(10) |
식 (10)에서 φ=[―y(k―1) ―y(k―2)]T는 필터링 휠속을 이용하여 결정할 수 있고, θ=[θ1 θ2]는 모델 파라미터 그리고 e는 White Gaussian 노이즈를 나타낸다.
파라미터 추정을 위한 Loss Function은 식 (11)과 같이 정의하였으며, 식 (11)를 최소화하기 위한 모델 파라미터는 식 (12)를 만족하도록 결정하였다.
(11) |
(12) |
식 (12)에 φ의 정의를 대입하여 식을 전개하면, 식 (13)과 같은 모델 파라미터 추정을 위한 솔루션을 얻을 수 있다.7)
(13) |
(14) |
식 (13)에서 R(i)는 식 (14)와 같은 필터링 휠속의 공분산을 나타낸다. 식 (13)으로부터 추정한 모델 파라미터를 이용하여 식 (15)와 같이 공진 주파수를 연산할 수 있다.8)
(15) |
본 논문에서 n = 1500로 선정하여 3 sec 동안 누적한 필터링 휠속을 이용하여 모델 파라미터를 추정하였다. 또한, 3sec에 한번 연산되는 공진 주파수를 식 (4)와 같은 평균 필터를 적용하여 타이어의 공진 주파수를 연산하였다.
3. 실차 시험 결과
본 논문을 통해 제안한 타이어 공진 주파수 추정 로직의 성능은 아래와 같이 실차시험을 통해 검증하였다. Fig. 9는 동일 공기압 상황에서 엔진 노이즈 제거 여부에 따른 차속 별 공진주파수 추정 결과를 나타낸다. Fig. 9로부터 엔진 노이즈 제거를 하지 않은 경우, 일정속도 이하에서 추정 주파수의 크기가 속도에 따라 크게 변동되는 것을 확인할 수 있다. 이는 엔진 RPM에 비례하여 엔진 주파수가 증가하여 엔진 노이즈가 발생하는 주파수가 증가하고, 이 노이즈에 의해 타이어 공진 주파수가 오추정되는 것을 확인할 수 있다. 반면에, 본 논문에서 제안한 엔진 노이즈 제거 방안을 적용할 경우, 동일 공기압에서 속도변동에 따른 추정 공진주파수 변동이 작은 것을 확인할 수 있다.
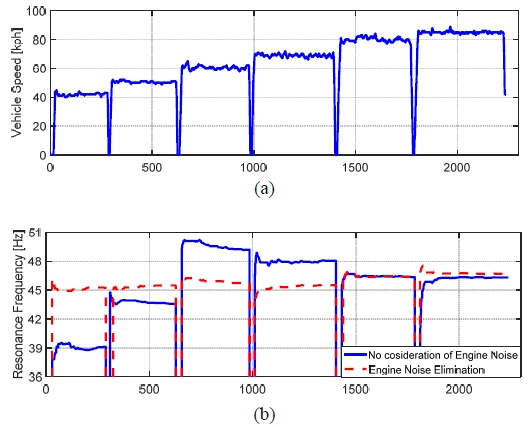
Estimated resonance frequency according to the vehicle speed (a) Vehicle speed (b) Estimated resonance frequency
추정 공진주파수를 이용한 저압감지 성능을 확인하기 위해 다양한 공기압 상태에서 실차시험을 수행하였다. Fig. 10은 타이어 공기압 별 추정 주파수를 나타낸다. Fig. 10(a)로부터 엔진 노이즈 제거를 하지 않은 경우, 일정속도 이하에서 추정 주파수를 이용하여 타이어의 저압 여부를 판별이 불가능함을 확인할 수 있다. 반면에, Fig. 10(b)로부터 본 논문에서 제안한 엔진 노이즈 제거 방안을 적용할 경우, 공기압 크기에 비례하게 공진 주파수가 추정됨을 확인할 수 있다.
4. 결 론
본 논문에서는 간접식 TPMS의 4휠 저압 감지를 위한 타이어 공진 주파수 추정 방안에 대해 서술하였다. 타이어의 회전방향 공진 주파수는 휠속 센서에서 측정된 펄스카운터를 이용하여 추정하였다. 휠속 연산 시, 각 톤휠의 오차를 보정함으로써 주기적인 노이즈 발생을 방지하였으며, 엔진 RPM을 이용하여 엔진 폭발에 의한 휠 회전방향 진동에 영향을 미치는 노이즈를 제거하였다. 마지막으로 모델 기반 파라미터 추정 기법을 이용하여 타이어의 회전방향 공진 주파수를 추정하였다. 공진 주파수 추정성능은 실차 시험을 통해 검증하였다. 실차 시험 결과로부터 추정된 공진주파수를 이용하여 타이어의 저압여부를 판정할 수 있음을 확인하였다.
References
- M. S. Lee and J. H. Lim, “A Consideration on the Safety Standard of the Motor Vehicle Equipped with Tire Pressure Monitoring System,” KSAE Spring Conference Proceedings, pp.25-31, 2010.
- F. Gustafsson, M. Drevö and N. Persson, Tire Pressure Estimation, US Patent 7, 240, 542, 2007.
- N. Persson, Event Based Sampling with Application to Spectral Estimation, Linkoping Studies in Science and Technology, 2002.
- J. G. Proakis and D. G. Manolakis, Digital Signal Processing, 4th Edn., Pearson Education, New Delhi, pp.2-6, 2007.
- R. K. Thenua and S. K. Agarwal, “Simulation and Performance Analysis of Adaptive Filter in Noise Cancellation,” International Journal of Engineering Science and Technology, Vol.2, No.9, pp.4373-4378, 2010.
- N. Persson, Event based Sampling with Application to Spectral Estimation, Technical Report, Department of Electrical Engineering, Linkoping University, Thesis No.981, Sweden, 2002.
- L. Ljung, System Identification Theory for the User, 2nd Edn., Prentice Hall, Upper Saddle River, 1999.
-
A. H. El Husseini, E. P. Simon and L. Ros, “Optimization of the Second Order Autoregressive Model AR(2) for Rayleigh-Jakes Flat Fading Channel Estimation with Kalman Filter,” 22nd International Conference on Digital Signal Processing (DSP), London, United Kingdom, 2017.
[https://doi.org/10.1109/ICDSP.2017.8096103]