
위상최적설계를 이용한 벌크 트레일러의 경량화 설계






Copyright Ⓒ 2017 KSAE
Abstract
There is a growing demand for commercial vehicles with a lightweight design due to fuel costs and environmental regulations. In this study, a bulk trailer is selected with the axle, suspension arm, and 5th wheel removed for simplification. Three extreme driving conditions when fully loaded are considered for the loading boundary conditions. Compliance minimization with a mass constraint is conducted in order to determine a lightweight design under these boundary conditions. Finally, based on the optimized design and consultation with field experts, a pilot model is determined and manufactured. This revised model can successfully achieve 14 % mass reduction in a bulk trailer compared with an original model.
Keywords:
Bulk trailer, Topology optimization, Finite element analysis, Lightweight design, CAD키워드:
벌크 트레일러, 위상 최적화, 유한요소해석, 경량화 설계, 캐드1. 서 론
최근 벌크 또는 평판 트레일러와 같은 대형 화물차의 연비 개선은 물류수송 분야에서 매우 중요한 문제로 대두되고 있다. 한국교통연구원의 연구에 의하면 국가 전체 물류비의 71 %는 수송비가 차지하고 있으며, 이 중 96.4 %는 화물차가 차지하고 있다.1,2) 또한, 유류비는 차주 지출액의 50 %를 차지하고 있다.1,2) 이러한 연비 개선은 경제적인 편익 뿐만 아니라, 세계적 환경 규제에 효과적으로 대응하기 위해서도 필수적이다. 차량 연비를 향상시킬 수 있는 대표적인 방안으로는 구동계 효율 향상과 차체 경량화를 들 수 있다. 이 중, 차체 경량화는 경량 료 적용, 경량화 최적 설계 등으로 구현 가능하다.
현재 국내 도로법과 동법 시행령 제28조 3항에 의거하여, 총 중량 40톤 이상의 화물차량에 대해 운행이 제한되고 있다. 이에 따라 대형 상용차에도 경량화 설계를 적용하는 연구가 시도되고 있다. 김진곤 등3)은 다구찌 방법을 이용하여 응력, 처짐량, 비틀림 강성에 대한 최적화를 수행하여, 평판 트레일러 하부프레임의 무게를 17 % 줄였다. 또한, 김진곤 등6)은 벌크 트레일러에 대한 정적 응력해석을 수행하여 대상 트레일러의 취약 영역을 찾은 후, 다구찌 방법으로 취약 부위의 강도를 보강하면서 다른 부위의 무게를 줄일 수 있는 설계 방안을 제시하였다. 다만, 해당 연구는 설계 영역의 두께만을 설계변수로 선정한 까닭에 레이아웃의 변경은 불가하였다.
위상최적설계는 주어진 설계 영역을 유한요소 단위로 이산화한 후, 개별 요소의 존재 여부와 관련된 설계변수로 부여하고 이에 대한 최적설계를 수행함으로써 최적의 설계안을 얻는 방법이다.7) 현재 자동차, 항공기, 건설기계, 선박 등 다양한 산업분야에서 성공적으로 적용되고 있다.8-12) 장강원 등4)은 위상최적설계를 이용하여 평판 트레일러의 무게를 29 % 줄이는 경량화 설계를 수행하였다. 또한, 김철 등5)은 위상최적설계를 이용하여 트레일러 제5차륜 연결부의 무게를 4.9 % 줄이는 경량화 설계를 수행하였다. 다만, 현재까지 수행된 트레일러 경량화 연구는 대부분 주요 구성품 혹은 조립품 단위에 초점이 맞추어져 있다.
본 연구에서 경량화하고자 하는 대상인 벌크 트레일러는 시멘트, 플라이 애쉬, 파우어 등의 분말류를 운송하기 위한 특수 화물차량이다. 벌크 트레일러의 경량화 설계를 위해서 벌크 용기와 프레임에 대해 설계영역을 선정하고, 주어진 하중조건과 질량 제한조건 하에서의 컴플라이언스를 최소화하도록 설정하였다. 이에 대한 위상최적설계의 결과를 바탕으로 현장 전문가와 협의하여 경량화 모델을 도출하고, 이를 제작하였다.
2. 유한요소 모델링
Fig. 1은 본 연구에서 경량화하고자 하는 벌크 트레일러에 대한 CAD 모델이다. 효과적인 유한요소해석을 위해서는 구조적 거동에 큰 영향을 미치지 않는 범위 내에서 CAD 모델을 단순화하는 것이 필요하다. 본 연구에서 제거된 부분은 차축, 서스펜션, 그리고 5th wheel 파트이다. 차축과 서스펜션은 지면으로부터의 반력 형태로 대체하였으며, 5th wheel은 트랙터에서 트레일러로 전달되는 하중의 형태로 단순화하였다. 트레일러의 차체 질량은 2,055 kg이며, 최대 용적량은 31.5 m3이다. 또한, 트레일러의 크기는 길이 10,550 mm, 너비 2,335 mm, 높이 2,828 mm이다. 구조 강판은 Table 1에 기술된 바와 같이 7가지 종류를 사용하였다.
유한요소모델링은 상용 소프트웨어인 Hyper-works를 이용하였다. 대상 유한요소모델은 3절점 삼각형 쉘요소와 4절점 사각형 쉘요소로 구성되어 있으며, 총 165,573개의 요소를 사용하였다. 제거된 부분(차축, 서스펜션, 5th wheel)에 대해서는 Fig. 2와 같이 경계조건을 부여하였다. 5th wheel은 킹핀 중심축에 대해 회전 자유도를 제외한 나머지 자유도를 구속하였고, 좌우측 경계부에서는 y축 방향의 자유도를 구속하였다. 서스펜션과의 연결부는 모든 자유도를 구속하였다.
본 연구에서는 최악 운행 조건으로써 벌크 용기에 시멘트를 최대 용적한 경우(Fig. 3)를 가정하고, 이 때 발생하는 벌크 용기의 내부 압력을 근사화하고자 한다. 우선 시멘트 분말 밀도 0.8×103kg/m3와 트레일러의 총 용적량 31.5m3을 고려하면, 용적 가능한 시멘트의 총 무게는 25.2ton이다. 벌크 용기에 사용된 전체 유한요소 중 용적부에 위치한 유한요소는 총 82,166개이며, 해당 유한요소에 대해 동일한 크기의 압력을 부여한다. 이 후, 벌크 용기 상단을 고정하였을 때, 식 (1)과 같이 자중(벌크 용기 및 시멘트)과 동일한 크기의 반력이 발생할 때의 압력을 구하면 920Pa이다.
(1) |
where
Fy : the resultant force in the y direction
: the resultant pressure in the y direction
mcement : the mass of cement
mbulkcontainer : the mass of bulk
g : the gravitational acceleration
위상최적설계에서 부여할 하중 조건으로 주행 중 발생할 수 있는 최악의 운전조건 3가지(Fig. 4)를 반영하였다.13) Ultimate vertical 모드는 주행 중 둔턱을 만나 지면으로부터 수직방향의 충격을 받는 상황을 가정한 것이다. 본 연구에서는 수직방향 가속도로 2.5 g를 부여하였다. Pot hole brake 모드는 주행 중 움푹 패인 노면에서 급제동하는 상황을 가정한 것이다. 이 경우, 수직방향 가속도는 2.5 g, 주행방향 가속도는 0.6 g를 부여하였다. Lateral Kerb Strike 모드는 둔턱으로 인해 타이어의 측면이 둔턱에 올라타는 상황을 가정한 것이다. 수직방향 가속도는 2.5 g, 측면방향 가속도는 0.3 g을 부여하였다. 트레일러 설계시, 추가적인 안전성 확보를 위해 개별 가속도에 안전율 1.6을 반영하였다. Fig. 5와 같이 전방/후방, 좌측/우측을 반영할 경우, 벌크 트레일러의 위상최적설계시 반영하여야할 하중조건은 총 8가지이며, 이를 Suspension과 5th wheel에 적용하였다.
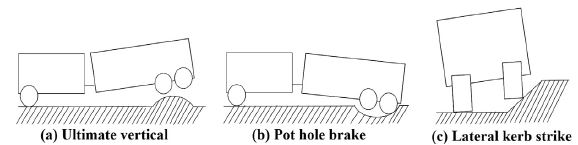
Three extreme condition during driving: (a) ultimate vertical, (b) pot hole brake, and (c) lateral kerb strike
3. 위상최적설계
위상최적화를 위한 수식은 식 (2)와 같다. 목적함수는 개별 하중조건을 반영한 벌크 트레일러의 변형 에너지를 최소화하는 것이다. 이 때, 개별 가중치는 동일한 값을 적용한다. 제한조건으로는 설계영역의 85 %에 대한 질량 제한조건을 사용한다.
(2) |
본 연구에서 선정한 설계영역은 Fig. 6과 같이 총 10개이다. 해당 설계영역은 트레일러 제조회사의 전문가들과 협의를 통해 선정하였다. 해당 영역 이외의 파트들은 비설계영역으로 설정되어 위상최적설계 과정 동안 고정된 값을 가지게 된다. 즉, 전체질량 2,055 kg 중 설계영역이 785 kg를 차지하며, 질량 제한조건 목표인 85 %를 달성할 경우, 118 kg의 경량화가 가능하다. 위상최적설계를 위해서 상용 프로그램인 Optistruct를 이용하였다.
위상최적설계 과정에서의 목적함수의 변화는 Fig. 8과 같으며, 최종 설계안은 Fig. 7과 같다.
Fig. 9는 위상최적설계 결과와 이를 반영하여 제작한 개선 모델을 3개 구역(전면부, 중간부, 후면부) 별로 비교한 결과이며, 세부적인 개선 방안은 하기와 같다.
∙ 전면부: 위상최적설계에서 주로 Bottom plate와 Cone support 파트에서 경량화가 이루어졌다. Fig. 9에서 파란색으로 표시된 부분은 상대 밀도값이 0에 가까운 부분이기 때문에, 개선 모델로 구현시 이를 구멍 형태로 대체하였다.
∙ 중간부: 위상최적화 과정에서 2번째와 6번째의 Internal ring이 다른 부위에 비해 많이 제거된 형태의 결과가 나왔다. 이를 반영하여 개선 모델 제작시 2번째와 6번째 링을 제거하였다. 본 연구에서는 벌크 용기를 비설계영역으로 설정한 까닭에 위상최적화 과정 동안 이에 대한 경량화가 수행되지 않았다. 다만, 최적화된 모델의 벌크 용기에 분포하는 등가응력이 SUS201의 항복강도보다 낮기때문(Fig. 10)에, 개선 모델에서는 벌크 용기의 재료를 SPFH590에서 SUS201로 변경하고, 기존 2.2 T였던 두께를 2.0 T로 변경하였다.
∙ 후면부: Rear cross member의 중앙 부분에 구멍을 뚫는 형태로 위상최적설계 결과가 나왔다. 이를 반영하여 개선 모델에서는 중앙 부분에 추가적인 타공을 하였다.
위상최적설계 과정을 통해 경량화한 질량은 총 118 kg이며, 벌크 용기의 두께를 2.0 T로 변경시 100 kg의 추가적인 경량화가 가능하다. 이를 반영하여 실제 제작한 개선 모델은 초기 모델 대비 총 290 kg 경량화를 달성하였는데, 이 중 구조 강성과 관련된 부분으로는 벌크 용기가 100 kg, 메인 프레임에서 110 kg을 감량하였다. 즉, 위상최적설계를 적용하여, 초기 모델 대비 14 %의 경량화를 성공적으로 달성하였다.
4. 결 론
본 연구에서는 유류비 절감 및 환경 규제에 대한 효과적인 대응을 목표로 대형 화물차인 벌크 트레일러에 대한 경량화 설계를 수행하였다. 이를 위해 대상 트레일러 모델에 대한 단순화를 수행한 후, 최악 운전조건에 부합하는 기하학적 경계조건과 하중 경계조건을 근사화하고 이를 유한요소해석에 반영하였다. 이 후, 질량제한조건 하에서의 컴플라이언스 최소화를 통해 전체 트레일러 모델에 대한 경량화 경향을 파악하고, 이를 개선 모델에 실제 적용하여 14 %의 차체 경량화를 성공적으로 달성할 수 있었다. 향후 후속연구의 일환으로서, 고유 진동수 최대화를 위한 위상최적설계와 피로 강도를 고려한 개선 설계를 수행할 예정이다. 본 연구에서 수행한 위상최적설계 방법을 다른 차량 종류에 확대 적용할 경우, 국내 자동차 및 운송 산업에 많은 기여를 할 수 있을 것으로 기대된다.
Acknowledgments
본 연구는 국토교통과학기술진흥원 “도로화물 운송 효율화를 위한 트레일러 경량화, 공기저항저감 및 운송용기 최적화 기술개발 연구단”의 연구비 지원에 의해 수행되었습니다(과제번호 14TLRP-B077327-01).
References
- H. Kwon, and S. Seo, Korean National Logistics Costs in 2011 and 2012, The Korea Transport Institute, p1-126, (2014).
- H. Roh, I. Jeong, Y. Min, S. Hur, S. Shin, B. Yu, and S. Jang, “Enhancement of Road Freight Vehicle Fuel Efficiency Using Lightweight Flat-Bed Trailers Made of High-Strength Steel Plates”, Journal of Transport Research, Vol.22(No.2), p65-82, (2015).
- J. G. Kim, and M. S. Yoon, “Optimal Design of Lightweight Frame for Heavy Flat-Bed Trailer by Using Taguchi Method”, Transactions of the KSME(A), Vol.34(No.3), p353-359, (2010).
-
G. W. Jang, M. Yoon, and J. H. Park, “Lightweight Flatbed Trailer Design by Using Topology and Thickness Optimization”, Struct Multidisc Optim, Vol.41(No.2), p295-307, (2010).
[https://doi.org/10.1007/s00158-009-0409-x]
- C. Kim, S. Lee, and Y. Lee, “New Weight-reduction Design of the Fifth Wheel Coupler with a Trailer by Using Topology Optimization and Durability Tests”, Transactions of KSAE, Vol.24(No.1), p137-143, (2016).
- J. G. Kim, and J. G. Lee, “Static and Dynamic Finite Element Analyses of a Bulk-Cement Trailer”, Transactions of the KSME(A), Vol.36(No.8), p945-951, (2012).
- M. P. Bendsoe, and O. Sigmund, Topology Optimization: Theory, Methods and Applications, Springer, Heidelberg, (2004).
-
I. G. Jang, K. Kim, and B. M. Kwak, “Conceptual and Basic Designs of the Mobile Harbor Crane based on Topology and Shape Optimization”, Struct Multidisc Optim, Vol.50(No.3), p505-515, (2014).
[https://doi.org/10.1007/s00158-014-1073-3]
- S. H. Yoon, and Y. K. Yoon, “Topology Optimization of Cylinder Block using Component Mode Synthesis”, Transactions of KSAE, Vol.11(No.3), p177-183, (2003).
-
I. G. Jang, Y. H. Sung, E. J. Yoo, and B. M. Kwak, “Pattern Design of a Non-pneumatic Tyre for Stiffness Using Topology Optimization”, Engineering Optimization, Vol.44(No.2), p119-131, (2012).
[https://doi.org/10.1080/0305215x.2011.569546]
-
R. J. Yang, and A. I. Chahande, “Automotive Applications of Topology Optimization”, Structural Optimization, Vol.9(Issue 3), p245-249, (1995).
[https://doi.org/10.1007/bf01743977]
-
J. J. Joo, G. W. Reich, and J. T. Westfall, “Flexible Skin Development for Morphing Aircraft Applications via Topology Optimization”, Journal of Intelligent Material Systems and Structures, Vol.20(Issue 16), p1969-1985, (2009).
[https://doi.org/10.1177/1045389x09343026]
- C. Choi, and K. I. Bae, “The Stress Analyses of Chassis Components in the Early Stage of Vehicle Development”, The Korean Society of Mechanical Engineers, Vol.36(No.9), p876-885, (1996).