
현가장치 소음 발생인자 평가를 통한 부품소음 검증시험 최적화
Copyright Ⓒ 2017 KSAE / 148-09
Abstract
Suspension noise from under a passenger car is one of the important factors that impact the perceptual quality for drivers. However, it is difficult to validate this by component level testing in the early stage of development, because suspension noise caused by interaction of the related parts has been found at saleable vehicles late during development or at the manufacturing stage, when many customers have already filed for claims. This study proposed a validation testing under research by the DFSS process that enables reproduction of vehicle level noise by component level testing using a shock absorber with the related parts, such as urethane bumper and top mount. This study also developed a compromised test matrix while analyzing the noise factors through experimental design and analysis of variance to determine what factors can affect noise. Based on this study, we expect that the vehicle level and customer claim can be validated during initial development timing by a more reliable component noise validation test.
Keywords:
Suspension noise, Urethane bumper, Control factor, Design of experiments, Orthogonal array test matrix키워드:
현가장치소음, 우레탄범퍼, 제어인자, 실험계획법, 직교배열표1. 서 론
상대 부품간의 조합 및 간섭 등으로 발생하는 차량 하부 현가장치 소음의 경우, 부품 개발 단계보다 주변 상대 부품들이 조립되고, 다양한 도로 조건의 하중과 움직임이 차량에 부가되면서 현가장치 부품들이 상대 거동하는 완성차량단계에서 유효한 검증들이 가능해 왔다. 하지만 차량 개발 후반 또는 양산시점 이후 차량의 생산대수가 늘어남에 따라 발견되는 차량 출시 직전의 소음 문제들은 많은 비용과 노력이 요구되어야만 해결할 수 있는 상황이다. 또한 신차 출시 초기 소비자의 소음 불만 사항은 차량판매 및 브랜드 이미지에 부정적인 영향을 미친다. 이에 신차 개발 초기 시점 부품 및 시스템 레벨에서도 소음 발생 여부를 검증할 수 있는 신뢰할 만한 시험평가 방법의 필요성이 꾸준히 제기되고 있는 실정이다.1-3)
현재까지 자동차 부품 및 완성차 업계에서 진행되어 왔던 현가부품 소음 관련 부품시험은 부품 자체만으로 진행하거나, 여러 소음 발생 인자들을 나열하여 조합된 매트릭스를 이용하여 모든 조건 별로 시험이 실시되어, 비교적 장시간을 소요하며 실시 되어왔다. 또한, 부품 소음 시험을 통과한 제품이라도 실차 검증 시 또는 출시 이후 필드에서 소비자 불만 사항으로 발생하여 브랜드 이미지에 부정적인 영향과 문제 해결을 위한 많은 시간과 비용을 소요하게 만들어, 부품 소음시험의 신뢰성에 대해 의구심이 존재해 왔으며, 현가장치 시스템 상에서 소음을 확인하고자 하는 연구가 진행되어 오고 있다.4-6)
본 연구에서는 현가장치 소음을 양산차량 또는 초도 시작 차량 생산 이전에 선행적으로 검증하고 확인할 수 있는 관련 부품을 사용한 소음 검증 시험방법과 발생 인자별 주요 영향 인자를 파악하여 최적화된 시험조건 매트릭스를 제안하여 시험에 적용하고자 하였다.
2. 본 론
본 논문은 DFSS(Design For Six Sigma) 기법으로 연구를 진행했으며, IDV(Identify / Define Requirement / Verify) 방법론의 순서에 따라 진행이 되었다.
Identify 단계에서 현재의 부품 소음시험 조건을 검토하고 문제점을 확인하였으며, Define requirement 단계에서 실차 조건의 소음 발생 인자들을 정의하여 시험 조건에 반영하였다. 또한 특정 도로 조건에서의 차량 거동을 분석하여 반영하였으며, 시험 측정 방법을 확정하였다. 전체 시험 인자들을 반영한 테스트 매트릭스를 L18직교 배열표를 이용하여 시험순서 및 횟수를 확정하였고, Verify 단계에서 쇽 업쇼버 현가장치 관련 상대 부품들을 장착한 부품 레벨에서 실험계획법을 이용한 소음 시험을 실시하고, 결과에 대해 분산 분석을 진행하였다. 소음발생인자의 영향도와 교호작용을 분석하여, 소음을 발생시키는 데 영향을 미치는 유의한 제어 인자를 확인하고, 부품 소음 검증 시험 조건을 최적화하고자 하였다.7-9)
2.1 실험조건과 소음인자
본 연구에서 시료로 사용된 주요 현가장치부품은 쇽 업쇼바 상단 마운트 부에 부착된 급속한 압축 시 부품 간의 충격 완충 부품인 우레탄 범퍼(Urethane bumper)로, 고정 방식에 따라 로드 고정 타입과 마운트 컵 고정 타입으로 구분하여 두 종류 시험편에 대해 소음 부품시험을 비교 진행하였다.
Identify 단계에서 기존의 부품 소음시험의 문제점으로 확인된 부품 자체만의 시험법이 아닌 상대부품을 사용한 조합시험을 실시하기 위해 Fig. 1과 같이 탑 마운트와 스트라이크 캡 등의 관련된 쇽 업쇼바 주변 부품을 장착하여 사용하였고, 실차 상태조립 조건을 반영하여 로드와 실린더를 실차 조건과 같이 기울여 시험 조건을 설정하였다.
또한 기존의 소음 측정 방법인 마이크로폰을 이용한 소음 측정방법의 문제점인 주변 소음 문제 소음 출처의 확인 어려움 등의 문제점을 보완하기 위하여 상대부품간의 마찰에 의한 소음 발생 시 전달된 진동을 감지하여 측정하는 진동 가속계(Accelerometer)를 이용한 방법으로 변경하고, IEPE(Integrated Electronic Piezo Electric)타입 가속도계를 Fig. 1에 보여지는 것처럼 로드 앤드(Rod End)부, 마운트 컵(Mount Cup)부, 그리고 스트라이크 캡(Strike Cap)부, 3곳에 장착하여, LMS사 소음진동 측정장비와 LMS Test Lab. Software를 이용하여 가속도 값을 측정하였다.10)
Define 단계에서는 차량의 사용 환경과 거동 조건 등을 정의하였다. 검토된 각 소음 유발인자로 판단되는 제어인자(Control Factors)들은 거동 속도(Velocity : Hz), 이동 거리(Stroke : mm), 로드 부 축 방향 기울어짐(Rod Tilting) 여부 등의 차량 관련 조건과 주변 온도(Temperature : °C)와 쇽 오일의 누유로 인한 로드 부 표면 존재 여부(Shock oil) 등의 부품 사용 환경 조건, 그리고, 그 외 부품이 사용된 정도의 내구 마모 및 변형 여부(New and Worn : %)에 따른 조건 등으로 검토하여 정의하였다. 이를 각각 수준별 제어인자를 구분하여 Table 1에 정리하여 나타내었고, 소음 발생에 영향을 미치는 것으로 판단되는 6개의 제어인자, 즉 4수준 1개, 3수준 2개, 2수준 3개를 선택한 후 최소한의 실험횟수로 최대한의 인자를 배치할 수 있는 L18 직교 배열표를 이용하여 Table 2와 같이 나타내었다.
2.2 결과 및 분석
본 시험에 사용된 시험편은 고정방식에 따라 두가지로 나누었고, 각각의 구분을 마운트 컵 고정방식을 타입 M으로, 로드 고정방식의 시험편을 타입 R로 표기하였다. L18 직교 배열표를 통한 시험순서와 조건으로 실시한 시험에서 얻어진 각 조건에서의 가속도 최고값을 정리하여 Table 3과 같이 나타내었다.
시험편에 따라서는 타입 R의 경우가 타입 M의 우레탄 범퍼에 대비하여 대부분의 조건과 로드 앤드 부에서 높은 가속도 값을 나타냈다. 로드 앤드 부에서 측정된 가속도는 쇽 업쇼버 압축 시에 우레탄 범퍼의 안쪽 내경 부의 찌그러짐 변형이 발생하여 로드 외경과 상대 마찰하며 발생하는 것으로 판단된다.
타입 R의 스트라이크 캡 부의 10 m/s2 이상의 가속도 값은 L18직교 배열표의 No 3, 6, 10, 14 실험조건에서 발생하였는데, 이는 공통적으로 내구 사용조건 Worn 50 %와 긴 스트로크 A의 조건을 가지고 있으며, 상대적으로 우레탄 범퍼가 전체적으로 압축되는 풀 스트로크 조건과 내구 사용 후 시험편의 조건이 소음 발생에 영향을 주는 주요한 인자가 되는 것으로 생각된다.
로드 앤드 부의 가속도 값에 대한 주 효과(Main Effect)를 ANOVA(Analysis Of Variation) 분산 분석을 통해 유의한 인자를 찾아내고, 최적 조건을 구하기 위하여 Minitab 상용프로그램을 이용하여 분석하였고, 타입 R 시험편 결과를 Fig. 2에 나타내었다. Fig. 2(a), (b)에서 보여 주듯이 시험결과에 따른 제어인자 간의 주 효과 분석에서 온도 인자의 경우는 고온 영역에 비해 저온 영역이 다소 영향이 없는 것으로 나타났다(P value= 0.855). 속도인자의 경우는 2.0 Hz와 같은 빠른 속도는 변별력이 없었으며(P value = 0.423), 쇽 오일의 로드 부 존재 여부도 영향이 적은 것으로 보여진다(P value=0.905). 반면, 실차와 유사한 부품의 위치 및 거동을 반영한 로드의 기울어짐 각도(Rod Tilting)와 스트로크 양(mm)은 소음 발생에 주요한 인자로 나타났다(각각 P value =0.009, 0.055).
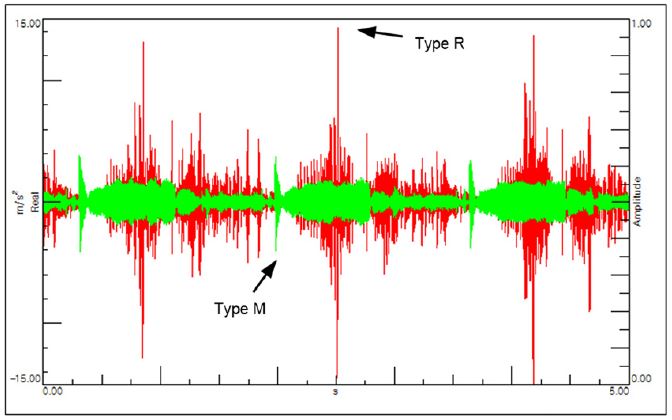
Example of data for accelerometer vs time from Rod end : Rod tilting, New sample, Vel. = 0.6Hz, Room temp., Stroke A
측정된 실험결과에서 분산분석을 진행한 결과에 따라 유효한 제어인자 이외의 영향도가 작은 것으로 판단되는 -25°C 저온조건, 내구사용조건 10 %, 속도 2 Hz, 쇽 오일 유무 등의 인자들을 제외시켰으며, Table 4와 같이 제어인자 매트릭스를 다시 설정하였다.
2.3 추가 시험 결과 분석
분산 분석 및 실험 결과 검토를 통해 얻어진 유효한 인자를 선정하여 Table 4와 같이 최대 3수준으로 구분하여 나타냈으며, 시험순서 및 조건 매트릭스를 Table 5에 나타냈다.
기존의 시험방법에 따른다면 시험인자 4수준 x 1개, 3수준 x 2개, 2수준 x 3개, 총 6개 제어인자 경우의 시험매트릭스는 시험편 당 108회 시험을 실시해야 하지만 다시 설정된 3수준 x 1개, 2수준 x 3개, 즉 총 4개 제어인자의 경우 시험편 당 24회의 시험을 실시하면 되는 것으로 총 시험횟수가 기존 대비 78 % 감소하였다.
이에 대해 기존의 시험 조건에 대비하여 감소된 시험 조건으로도 유사한 수준의 결과를 얻을 수 있는 지 비교하기 위해 추가 시험을 실시하였다.
최적화된 시험순서와 조건으로 시험된 시험 결과를 Fig. 4와 같이 각 가속계 부착 위치에 따라 비교하여 나타내었다. 그림 Fig. 4(a)에서 보듯이 마운트 컵부, 스트라이크 캡 부에 비해 로드 앤드 부에서 높은 가속도가 측정되었으며, 타입 R 경우가 타입 M 시험편에 대비하여 전체적으로 모든 조건에서 높은 가속도를 보였고, 스트로크 A가 짧은 하프 스트로크 B 대비 높게 나타나는 경향을 보였다. 이는 최적화 전 시험결과와 비교하여 유사한 경향을 보여주고 있는 것으로 판단된다.
Fig. 4(b)에서 보듯이 마운트 컵 부에서도 가속도 10 m/s2 이하 수준이지만 상대적으로 50 °C 온도조건에서 높은 값을 보였고, 그림 Fig. 4(c)의 스트라이크 캡 부에서 측정된 가속도 값은 각 조건에 상관없이 영향을 받지 않고 유사한 수준에서 측정되었다. 이는 우레탄범퍼의 압축 시 쇽 로드와 비비며 발생한 마찰 진동은 마운컵 부와 마찬가지로 스트라이크 캡에서는 측정의 변별력이 없는 것으로 보여진다.
3. 결 론
본 논문에서는 실험계획법과 분산분석을 통하여 현가장치 부품의 소음 제어 인자를 분석하여 유효한 인자를 선정하고, 시험조건 및 방법 최적화 연구를 진행하여 다음과 같은 결론을 얻었다.
- 1) 제어인자 중 시험편 사용내구 조건과, 고온 온도 조건, 틸팅 조건 그리고, 스트로크 조건 등이 소음을 발생시키는 데 영향을 미치는 주요한 제어인자로 판단된다.
- 2) 쇽 오일 유무, -25 °C의 저온 조건 및 2 Hz의 속도 조건 등은 영향이 적은 것으로 보여지며, 고온 50 °C 조건과, 풀 스트로크의 경우 그리고, 내구 50 % 후 부품의 경우는 소음 발생 영향이 가장 높은 조건으로 나타났다.
- 3) 로드 고정 타입 R 시험편에서 마운트 고정 타입 M에 대비하여 온도, 내구조건 상관없이 로드 앤드 부 가속도계에서 전체적으로 높은 가속도 값을 나타냈으며, 상대적으로 스트라이크 캡 및 마운트 컵 부의 가속도계에서는 10 m/s2 이하의 낮은 가속 값을 보였다. 이는 로드와 우레탄 범퍼의 마찰에 의한 소음의 경우 로드 앤드부에서 측정값이 유효한 것으로 판단된다.
- 4) 기존 제안된 제어인자 조건에서의 시험 매트릭스는 시험편 당 108회의 시험이 필요하지만, 최적화된 조건에서는 시험편 당 24회로 시험횟수가 감소하여, 전체 시험시간 및 비용이 절감될 수 있을 것으로 기대된다.
Acknowledgments
*A part of this paper was presented at the KSAE 2016 Fall Conference and Exhibition
References
- C. W. Han, H. J. Kim, Y. J. Yoo, and S. H. Park, “Relationships between Free Gaps and Abnormal Noises of Vehicle Stabilizer Links”, Transactions of KSAE, 25(1), p28-34, (2017).
- M. K. Son, T. Y. Lee, S. B. Lee, and S. Lee, “A Study of Cause Factors for Suspension Noise and Component Validation Test Optimization”, KSAE Fall Conference Proceedings, p222-223, (2016).
- S. G. Park, I. H. Yang, J. H. Yoon, J. E. Oh, and Y. Y. Lee, “Transfer Path Analysis and Estimation of the Interior Noise for the Driving Vehicle”, KSAE Annual Conference Proceedings, p2253-2257, (2009).
- C. Y. Bae, D. W. Lee, C. J. Kim, B. H. Lee, and B. C. Na, “The Study on Noise Analysis of Bush on Suspension System”, KSNVE Fall Conference Proceedings, p69-74, (2006).
-
J. V. Haver, “Structure-Borne Shock Absorber Noise: Non-Linear Noise Source Characterization in a Laboratory Environment”, SAE 951255, (1995).
[https://doi.org/10.4271/951255]
-
D. Bogema, P. Goodes, C. Apelian, and M. Csakan, “Noise Path Analysis Process Evaluation of Automotive Shock Absorber Transient Noise”, SAE 2009-01-2091, (2009).
[https://doi.org/10.4271/2009-01-2091]
- General Motors Korea Vehicle Engineering Technical Center, DFSS Fundamental Course & Advanced Course, (2015).
- J. S. Park, U. C. Jeong, J. E. Jeong, J. Y. Lee, and J. E. Oh, “A Study on the Vibration Reduction of Vehicle Suspension System Using Design of Experiment”, KSNVE Fall Conference, p553-554, (2012).
- J. E. Oh, J. J. Cha, K. T. Lee, and C. G. Chin, “Design of Muffle using Taguchi Method and Experimental Design”, Transactions of KSAE, 7(5), p121-129, (1999).
-
G. Y. Kim, S. S. Kim, Y. J. Lee, S. C. Park, and W. W. Jung, “Study on Durability and Reliability of Strut Type Suspension Noise based on Experimental Methods”, JMST, 26(1), p21-29, (2012).
[https://doi.org/10.1007/s12206-011-1010-y]