
위상최적설계 기법을 이용한 후드 후변형 최소화 설계
Copyright Ⓒ 2020 KSAE / 180-03
This is an Open-Access article distributed under the terms of the Creative Commons Attribution Non-Commercial License(http://creativecommons.org/licenses/by-nc/3.0) which permits unrestricted non-commercial use, distribution, and reproduction in any medium provided the original work is properly cited.
Abstract
Vehicle quality is becoming a major requirement in the automotive market. The problem regarding the deformation of wide panels, such as the hood, is being raised as a representative example. In addition, deformation caused by hydraulic pressure in the paint line and gas lift leads to assembly and quality issues of parts. In order to solve this problem, a hood inner panel design is necessary. In this paper, we studied the inner panel design process in order to optimally design the frame shape of the inner panel by using the topology optimization, and optimally design the bead shape of the outer panel. Through this process, the paint deformation and gas lift deformation performance of the designed model and reference model were compared. The result showed that the designed model improved both performances without increasing the weight compared to the reference model.
Keywords:
Gaslift deformation, Hood inner panel design, Hood inner panel framework, Painting deformation, Topology optimization, Vehicle quality키워드:
가스리프트 후변형, 후드 내판 설계, 후드 내판 골조, 도장 후변형, 위상최적설계, 차량 품질1. 서 론
후드와 같은 넓은 판넬의 변형은 품질 문제로 연결될 수 있다. 품질 문제는 자동차 시장의 주요 요구사항이기 때문에 설계 단계에서 소비자의 요구 품질을 확보하기 위한 연구가 필요하다.
국내에서는 먼저, 하중 조건 별로 후드 내판의 설계 인자의 후드 후변형 영향도를 분석하는 연구가 수행되었다.1) 그리고 설계 민감도 해석을 이용하여 후드 내판의 최적 보강 경로를 구한 연구가 수행되었는데 보강 경로의 초기 형상 없이 최적의 보강 경로를 설계하였다. 설계된 후드 내판 모델은 기존 모델과 비교하여 무게의 증가 없이 1차 및 2차 모드에서의 동적 강성이 증가되었다.2) 또한 굽힘과 비틀림 하중을 동시에 고려한 연구도 수행되었다. 굽힘과 비틀림 성능에 가중치를 도입하여 다중 목적 최적 설계를 수행했으며, 후드의 곡률에 따른 최적 위상의 변화를 알기 위해 곡률이 큰 경우와 작은 경우에 대해 위상 최적화가 진행되었다.3)
해외에서는 Topology, Topometry, Topography, Size optimization을 순차적으로 수행하여 후드의 질량을 줄이는 설계 방법이 연구되었다. 굽힘 강성과 비틀림 강성, 그리고 3가지 닫힘상태에서 발생하는 하중 성능과 제조 가능성을 유지하면서 후드의 질량을 감소시켰다.4)
본 논문에서는 생산 공정 시 발생하는 도장 후변형과 가스리프트 변형의 품질 문제를 해결하기 위한 설계 프로세스를 제안하고자 한다.
먼저, 후드의 도장 후변형은 후드가 수용성 수지 도료에 들어가고 나올 때 생기는 도료 압력에 의해 발생하는 후드의 변형을 말한다. 후드의 전착 도장공정은 수용성 수지 도료가 있는 수조에 후드를 넣고 후드에 전류를 흘려 표면에 도막을 형성시키는 방법이다.
두번째로, 가스리프트 변형은 가스리프트가 후드에 설치되면 가스리프트의 가스압력에 의해 후드 내판에 생기는 국부적인 변형이다.
위상 최적 설계를 이용하여 위 변형들에 대한 하중 경로를 분석하고 내판의 골조 형상을 설계한 다음 형상 최적 설계를 내판 외곽의 비드 형상을 설계하여 내편 변형량을 추가적으로 개선했다.
2장에서는 후드 후변형 분석을 위한 해석 모델을 구축했다. 3장에서는 후드 내판 골조와 비드 형상을 최적 설계했다. 4장에서는 본 논문의 결과를 정리했다.
2. 후드 후변형 분석을 위한 해석 모델 구축
후드의 후변형 해석을 위한 모델을 해석 조건 별로 구축했다. 해석 조건은 도장 후변형과 가스리프트 변형이며, 두 가지 해석 모델 모두 ABAQUS의 Static에서 모델링 되었다. 해석 모델의 Element 크기는 6 mm이며 Element 개수는 총 95000개다. 후드의 내판과 외판은 2D sealer 요소로 결합했으며, 요소타입은 S4R과 S3이다. 해석은 경계조건 정의, 후변형 해석 그리고 해석 결과 분석 순으로 이루어진다.
2.1 도장 라인의 유압에 의한 후변형 해석 모델 구축
도장 라인에서 유압에 의해 발생하는 후변형 해석 모델을 구축했다. 이 모델의 구속조건은 후드가 도장 라인에 고정된 상태이다. 후드 래치와 가스리프트 지지점의 x, y, z 축 병진 방향을 구속하고, 클램프 체결점의 z 축 병진 방향을 구속했다. 각 구속 위치는 Fig. 1에 나타냈다.
도장 후변형에서의 하중조건은 시간과 후드에서의 위치마다 다르다. 해석 시간 30초대에서 입조하중이 입력된다. 입조하중은 후드가 전착 도료에 들어갈 때 생기는 압력에 의해 작용하는 하중이다. 이후에 120초대에서 출조하중이 입력된다. 출조하중은 후드가 전착 도료에서 빠져나올 때 생기는 압력에 의해 작용하는 하중이다. 최대 하중이 입력되는 부분은 후드 내판의 사이드부와 외판의 전면부이다. 하중 입력 값은 CFD 프로그램인 Star-CCM으로 정의된 하중을 사용했다.5) 도장 공정 중 후드 내판에 발생하는 압력은 Fig. 2와 같고, 후드 내판 각 파트의 위치는 Fig. 3에 나타냈다. 파란 실선은 후드 내판, 빨간 점선은 후드 외판, 노란 괘선은 후드 내판의 측면 부분의 압력이다.
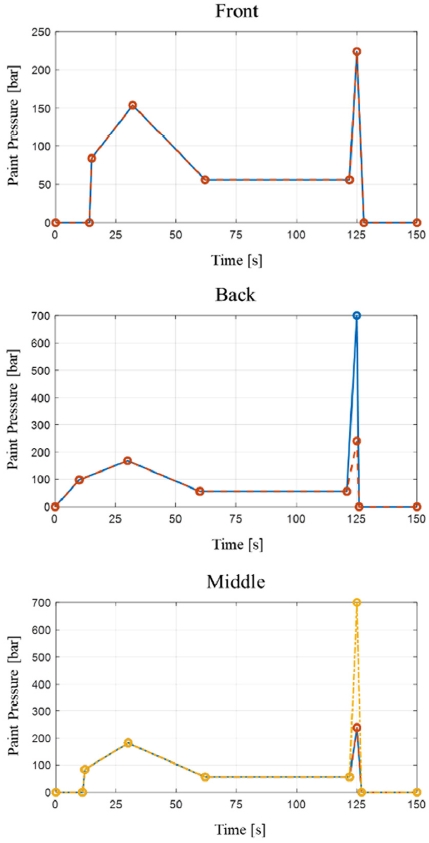
Load inputs of paint deformation analysis (solid(blue) line : inner panel, dotted(red) line : outer panel, ruled(yellow) line : inner side)
위의 경계조건으로 도장 후변형 해석을 ABAQUS에서 진행했다. 해석 결과 시간에 따른 후드 헤밍부의 변형량을 측정했고, 입조 시(해석 시간 32초)와 출조 시(해석 시간 125초)에서 최대 변형이 발생했다. 각 헤밍부의 해석결과는 Fig. 4와 같다. 따라서 최대 변형이 일어나는 시점인 출조 시의 하중을 기준으로 내판 골조 하중 경로 분석이 필요하다.
2.2 가스리프트에 의한 후변형 해석 모델 구축
가스리프트에 의해 발생하는 후드 내판의 후변형 해석 모델을 구축했다. 모델의 구속조건은 후드가 차체에 고정된 상태이다. 후드 래치의 x, y, z 축 병진 방향을 고정했고, 가스리프트 지지점은 x, y, z 축 병진 방향과 회전방향 모두 고정했다. 각 구속 위치는 Fig. 5에 나타냈다.
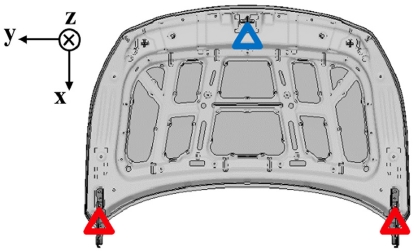
Constraints of gaslift deformation analysis (red : x, y, z-axis and rotation fixation, blue : x, y, z-axis fixation)
가스리프트 후변형 하중조건은 Bracket에 가스리프트의 최대 하중인 480 N을 입력했다. 입력된 하중의 위치는 Fig. 6에 나타냈으며, 이 하중은 x 축 방향으로는 479.49 N, y 축 방향으로는 0 N, z 축 방향으로 는 22.118 N 이 작용한다.
가스리프트 후변형 해석은 ABAQUS에서 수행했다. 그 결과 Fig. 7에서 볼 수 있듯이 가스리프트에 의한 후변형은 가스리프트 지지점 주변에서만 발생하는 것을 확인했고, 가스리프트 변형을 보완하기 위해서는 내판의 외곽부 보강이 필요하다.
3. 최적 설계 수행
본 연구에서는 후드 내판을 설계하기 위해 두 가지 최적 설계를 수행했다. 먼저 후드 내판 골조 형상을 설계하기 위해 위상 최적화 기법을 사용했다. 이 기법은 목적함수와 제한조건에 대해 각 요소 밀도를 판정하여 설계 위상을 도출하는 방법이다. 이 기법을 이용하면 후면형 해석의 경계조건에 대한 내판의 하중 경로를 예측할 수 있으며 내판 골조 설계에 반영할 수 있다. 내판 골조 형상이 정해진 다음 후드 외곽의 비드 형상을 최적 설계한다. 이 단계에서는 목적함수와 제한조건을 만족하는 최종적인 비드 형상을 도출한다.
3.1 위상 최적 설계
도장 후변형 성능과 가스리프트 후변형 성능에 대한 위상 최적설계를 각각 수행한 후, 두 모델을 고려하여 최종 내판 골조를 설계했다. 위상 최적 설계의 초기 모델은 후드 내판의 내부가 모두 채워져 있고, 외곽 비드가 모두 제거된 모델이다. 설계 범위는 내판 내부 전체이다.
도장 후변형에 대한 위상 최적 설계는 변형이 가장 많이 일어나는 헤밍부의 변형을 최소로 하고, Mass fraction을 초기 모델의 75 % 이하로 설계되도록 설계 문제를 정식화했다.
(1) |
가스리프트 후변형에 대한 위상 최적 설계는 Mass fraction을 최소로 하고, 가스리프트 지지점의 변형량이 Initial model의 변형량인 2.04 mm 이하고 설계되도록 설계 문제를 정식화했다.
(2) |
위상 최적 설계는 Optistruct의 Topology optimization을 이용하여 수행했다. 도장 후변형에서는 하중조건 중에서 후드에 가장 큰 압력을 받는 출조 시의 하중조건을 입력했고, 가스리프트 후변형 해석에서는 가스리프트의 최대 하중인 480 N을 입력했다. 위상 최적 설계 진행 결과 두 가지 후변형의 하중 경로를 파악했다. Fig. 9는 도장 후변형의 하중 경로이고, Fig. 10은 가스리프트 변형의 하중 경로이다.
하중 경로를 보강하여 내판 골조를 설계했고, 후변형 해석을 수행했다. Table 1은 위상 최적 설계의 해석 결과이다. 초기 모델 대비 도장 후변형 모델의 무게는 7.06 kg에서 5.69 kg으로 1.37 kg 감소했고, 변형량은 3.62 mm에서 2.69 mm로 0.93 mm 감소했다. 또한 가스리프트 모델의 무게는 5.48 kg으로 1.58 kg 감소했고, 도장 후변형량은 2.80 mm로 0.82 mm 감소했다. 이로써 내판 골조의 형상에 따라 도장 후변형량의 차이가 있음을 확인했다. 그리고 가스리프트에 의한 변형은 내판 골조에 영향이 없었지만 무게는 가장 적었다.
도장 후변형 모델의 하중 경로와 가스리프트 변형 모델의 하중 경로 그리고 제작 가능성을 고려하여 최종 후드 내판 형상을 도출했다. 도장 후변형의 하중 경로는 횡축 방향으로 나타났고 가스리프트 변형의 하중 경로는 격자 형태로 나타났다. 본 연구에서는 중앙부 3부분과 측면 2부분을 나누어 도장 후변형 횡축 하중 경로와 가스리프트 변형 종축 하중 경로를 Fig. 11과 같이 조합하였다.
3.2 비드 형상 최적 설계
후드 내판 내부 골조 형상을 도출한 후, 후드 내판 외곽비드 형상을 최적 설계했다. 설계 범위는 후드 내판의 외곽부이다.
도장 후변형에 대한 비드 형상 설계는 변형량을 최소로 하되 질량은 기존 모델보다 크지 않게 설계되도록 설계 문제를 정식화했다.
(3) |
가스리프트 후변형에 대한 설계 문제는 도장 후변형 설계 문제와 동일하게 정식화했다.
(4) |
Optistruct의 Topography optimization을 이용하여 도장 후변형과 가스리프트 후변형에 대한 최적 설계를 진행했다. 도장 후변형과 가스리프트 후변형의 응력 집중부를 합하고 이 부분에 강성 비드를 추가했다. 초기 모델은 외곽 비드가 모두 제거된 위상 최적 모델의 외곽 영역이다. 도장 후변형 해석과 가스리프트 후변형 해석을 통해 내판 외곽의 응력 집중부를 찾았고, 두 가지 해석 중 한가지라도 응력이 집중되는 부분에 강성 비드를 추가했다. Fig. 12는 도장 후변형 해석 결과의 형상 밀도이고, Fig. 13은 가스리프트 변형 해석 결과의 형상 밀도이다.
설계 결과 비드 형상과 후드 내판 형상을 도출했다. Fig. 14는 초기 기준 모델의 형상이고, Fig. 15는 최종적으로 도출된 후드 내판 형상이다. 여기서 도출된 모델과 위상 최적 설계 모델, 기준 차량 모델의 해석 결과를 Table 2에 정리했다. 가스리프트 변형은 1.50 mm로 위상 최적 설계 결과인 2.04 mm보다 0.54 mm 개선되었고, 초기 모델의 변형량인 1.59 mm 보다 0.09 mm 개선되었다. 그 다음 도장 후변형은 1.64 mm로 위상 최적 설계 결과인 3.08 mm보다 1.44 mm 개선되었고, 초기 모델의 변형량인 2.69 mm보다 1.05 mm 개선되었다. 비드 형상 최적 설계를 거치면서 비드가 추가되어 위상 최적 설계 모델보다 후드 내판의 무게가 0.22 kg 증가했지만 기준 모델의 무게 보다는 0.02 kg 감소했다.
4. 결 론
본 논문에서는 생산 도중 발생할 수 있는 후드 내판 후변형에 대한 품질 확보를 위해 설계 단계에서 내판 강성을 보강할 수 있는 설계 프로세스를 제시했다.
먼저, 도장 후변형과 가스리프트 변형 해석에 필요한 해석조건을 정의하여 해석 모델을 구축하였다. 그 다음, 위상 최적 설계와 비드 형상 최적 설계를 순서대로 진행했다. 위상 최적 설계에서는 후드 내판의 골조가, 그리고 비드 형상 최적 설계에서는 후드 내판 외곽의 강성 비드 형상이 도출되었다.
최종적으로 설계된 후드 내판은 기준 모델대비 성능이 향상되었다. 무게 증가 없이, 도장 후변형량은 46.8 % 개선되었고, 가스리프트 변형량은 5.66 % 개선되었다.
후드 내판 설계에 있어서 정동강성과 보행자 법규에 대한 고려도 포함하여 설계가 진행되어야 하지만 본 논문에서는 생산 공정에서 발생하는 품질 문제를 해결하기 위해 후드 내판의 변형량과 무게 감소에 대한 연구가 우선 수행되었다. 최종적으로 설계된 후드 내판 형상이 초기 형상에 비해 많이 변경되어 다른 모델이 되었으므로 도출된 형상의 실용화 적용을 위해서는 추후 정동강성과 보행자 법규에 대한 검토가 이루어져야 할 것이다.
Acknowledgments
이 논문은 2020년도 BK21플러스 사업에 의하여 지원되었음.
References
- J. H. Yoon, A Study on Hood Inner Panel Shape Optimization for Hood Deflection Minimization, Ph. D. Dissertation, Kookmin University, Seoul, 2015.
- T. H. Lee, D. G. Lee, J. G. Gu, S. Y. Han and J. G. Im, “Optimization of the Path of Inner Reinforcement for an Automobile Hood Using Design Sensitivity Analysis,” Transactions of the Korean Society of Mechanical Engineers - A, Vol.24, No.1, pp.62-68, 2000.
- S. Y. Han, S. H. Choi, J. Y. Park, J. S. Hwang and M. S. Kim, “Topology Optimization of a Vehicle’s Hood Considering Static Stiffness,” Transactions of the Korean Society of Machine Tool Engineers, Vol.16, No.1, pp.69-74, 2007.
- D. Costi, E. Torricelli, L. Splendi and M. Pettazzoni, “Optimization Methodology for an Automotive Hood Substructure (Inner Panel),” Proceedings of the World Congress on Engineering, Vol.3, pp.2390-2393, 2011.
- S. H. Park, J. R. Choi, N. K. Hur and C. S. Oh, “A Numerical Analysis Toward Flow Characteristics Around The Hood During Rotation Electro-deposition Painting Process,” Korean Society for Computational Fluids Engineering, pp.125-128, 2011.